The One-Shot® Method is not only the world’s fastest method to produce car parts. It is also the only one that allows you to produce non-stop, hence with a short lead time, which will make your customers happy.
If you are one of those people who design car parts every day and look for solutions that best meet the requirements of your car maker, then this article is for you.
If you are an unhappy, frustrated car maker, or curious to find ways to improve your company’s results, then this article is for you, too.
If you love your job so much as to set out and look for innovative options to optimise your processes and obtain better guaranteed results, then I have what you are looking for.
Please continue reading: I am sure that you won’t regret it.
Today we are going to talk about the Dream.
I know what you’re thinking: here we go with the nth idealistic article that wants to lecture me how to do my job better.
OK, this is not what I’d like to talk to you about here.
What I am talking about, is the big Dream that since ever unites all of us who work in the field of production. I wrote Dream and I wrote it with a capital D for a reason.
Of course, you could argue that there are many dreams tucked away somewhere, especially for people with a great vision in our sector.
Yet, if you think about it, there is one unreachable objective, the one that is considered as the solution to all problems, the one that unites all those for whom trade on a large scale has become their life mission, the one that made us wish for yet another toy-car, yet another toy when we were children.
Do you remember “The Chocolate Factory” story?
Maybe as a child you saw the film or read the book.
Willy Wonka was a candy manufacturer who dominated the world market. His chocolate factory was a mystery for the whole town; it was a mystery how he could produce an amount of chocolate candy close to infinity.
Reproducing the deliciousness that came out of his factory was impossible, especially the recipe of the candy that never dissolved in your mouth.
This was his secret.
And this is the dream that I would like to talk to you about today: endless productivity.
The idea of infinity, longing for something that never ends dates far back in the history of humanity. What I would like to talk to you about today is the actual possibility of doing so, thus turning your work method but especially your results upside down.
This is what happened to us and this is what I’d like to tell you about.
The One-Shot® Method
You’ve probably already heard about it, I will describe it in few words: the One-Shot® Method is the revolution within the automotive sector in terms of car part production.
The reason is easy.
It is currently the fastest method to produce car parts with:
- Less weight
- Less waste
- High quality standards.
The One-Shot® Method rests on the idea that any process can be shortened by optimising the production phases. Clearly, this is not easy, but it is the result of hard study, tests and trials that SAPA’s “Innovation Engineering” secret department has carried out with remarkable results.
SAPA’s most ambitious objective is to reduce the number of work phases to just one, wherever possible.
This method was patented for this very reason: One-Shot® is our work method and this approach can be applied to several and different products.
I imagine that you are wondering what this means practically. Please let me explain.
Imagine that you can obtain the same part but in much shorter time in comparison with the traditional method.
By reducing the production line, the first consequences will be:
- Less need for specialised workers, so the final cost of the part decreases;
- Less occupied space: if you optimise the process, you will need only one machine, so you will be able to replicate the process anywhere and you can invest on other useful machines;
- Exponential increase in production, so you can meet the client’s requirements;
- Shorter delivery time, hence, no more delays and hence a solution for most of your issues in this respect;
- No more downtime, which means that you will always meet delivery deadlines;
- Diminished use of back-up machines: if you have less machines to coordinate, the error risk will decrease, and you will have a leaner process that meets the customer’s expectations in a better way.
The case of the One-Shot® Engine Beauty Cover
I would like to quote an example.
At SAPA we have developed and patented several parts with the One-Shot® Method.
In particular, the One-Shot® Engine Beauty Cover was created in one single moulding phase, which replaced the traditional method in which 3 moulds and the support of external suppliers for the foamed piece are needed.
In the traditional method, namely, we have:
- 3 moulding operations for each part: more tooling costs, more occupied surface and therefore more fixed and variable costs;
- Several suppliers for one single cover: difficulties in managing and controlling the process;
- More transport costs hence higher environmental impact.
Plus: higher risks, reduced control over the process and an uncontrolled amount of waste.
By applying the One-Shot® Method, on the other hand, SAPA’s engineers obtained the same results in terms of product performance quality but in just one step: the moulding phase and the addition of PUR were reduced to just one step, and the assembly phase of the pieces was eliminated.
What this entails concretely:
- 300% productivity increase;
- One single mould instead of 3: in the standard process, 1 mould is needed for the hard shell and 2 more are needed for the PUR;
- The cycle time is reduced from 180 seconds (needed to mould the cover + soundproof moulding) to 60 seconds;
- Joining with star locks is no longer needed because the part is joined chemically, so no operator and no dedicated machine are needed to join the part to the cover;
- Improved luxury sensation thanks to reduced rubbing and noisiness.
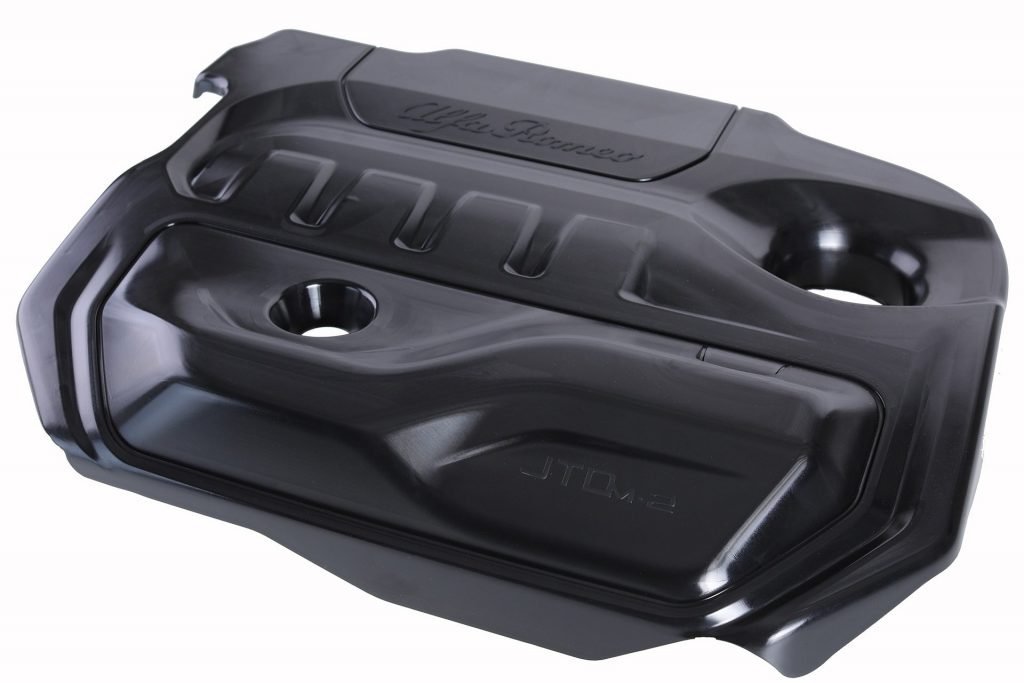
Less weight and more sustainability.
Do you see what applying these advantages in your daily work can do for you?
There is more.
The One-Shot® Method was created also with another objective in mind that actually pertains process optimisation.
I am referring to the idea of creating more lightweight parts right from the design phase.
Nowadays the market is increasingly focusing on more environmental-friendly products and more in general, I believe that nowadays we must take these trends and needs into account as they concern not only our work but our daily life, too.
SAPA has decided to invest in research also for this reason and all the products produced with the One-Shot® Method are characterised by less weight and sometimes by the use of composite and less polluting materials.
If you think about it, creating a product in fewer steps directly results in decreased waste.
Let’s go back to the Engine Beauty Cover produced with the One-Shot® Method: with the traditional production methods, the injection of foamed PUR was carried out by external suppliers and this was clearly an additional phase that resulted in the use of means of transport and in higher energy consumption.
With the One-Shot® Method, on the opposite, this is not the case because the whole production is condensed in one single work station.
Just to quote another example: for the new Aeroshield – SAPA’s latest One-Shot® product, on which we decided not to use polyethylene, which is normally used on low-cost parts; instead, we decided to revert to another material and another technique.
That is to say that instead of thermoforming, we went for Back Injection moulding, which joins the polypropylene to a carbon fibre cloth: one single step to obtain a mixed and ultra-high-quality material.
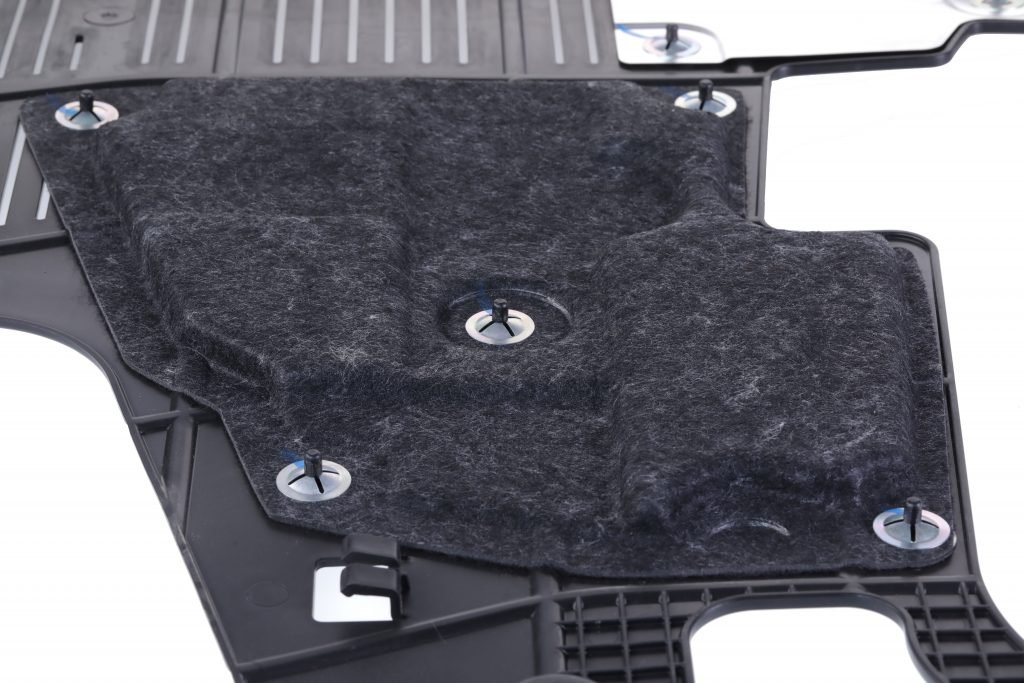
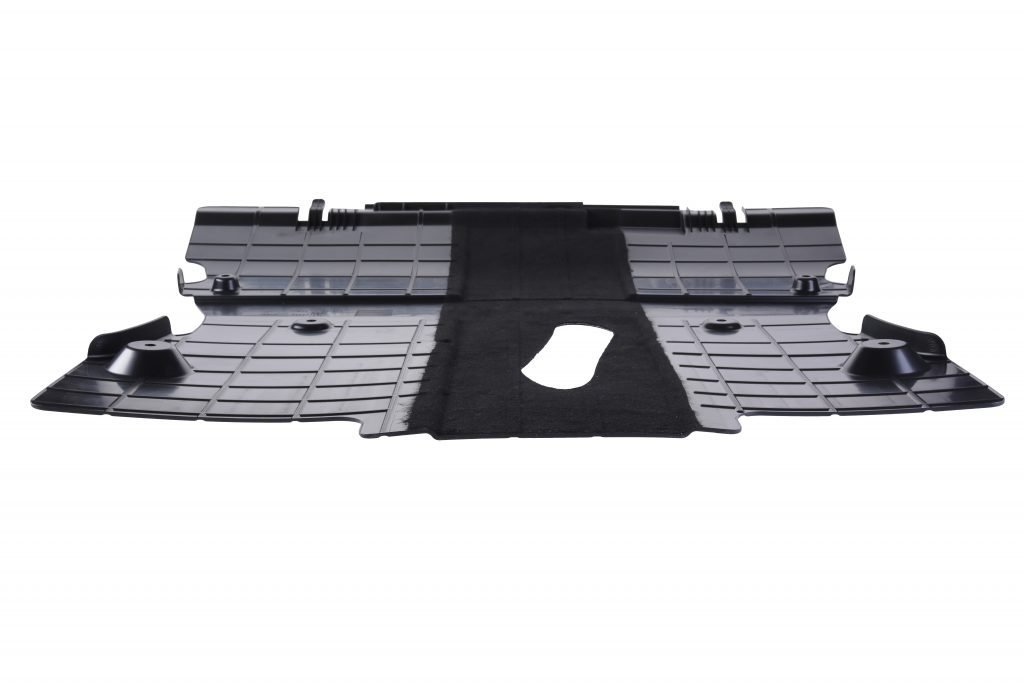
In a way, the One-Shot® Method takes the concept of lean production even further.
I know what you’re thinking: what about product quality?
As I was saying earlier, quality performance is fully certified, and this is what makes us competitive at international level.
Quality must keep up with quantity, otherwise we lose our challenge, otherwise the One-Shot® Method would fail.
And because we are so sure, we have created a new guarantee, the One-Shot® Guarantee.
What is it?
When you request a quote, you will receive two offers from us: one with the One-Shot® Method, the other with the traditional method but the tooling costs will be borne by us.
If the One-Shot® solution does keep its promises, the back up with the traditional method will be paid by us. This means zero risks for you, with a guaranteed alternative solution.
As you can see, we trust the One-Shot® Method so much that this “agreement” is a guarantee for us, too.
This is our spirit and our way of working.
Just last year, in December 2018, we were awarded as Supplier of the Year by FCA. We were proud and even more assured about going down this certainly not-for-granted and certainly not easy path!
The One-Shot® Method is the secret ingredient to achieve unlimited production.
But, unlike Willy Wonka, we have decided to share it with you.
Because we know that it can be useful to you, it can sky-rocket the quality and the concrete results of your work, because we believe that this solution caters for the needs of sustainability for our planet.
Because it is an alternative, and as such it can make a difference.
Kind regards,
Giovanni Affinita
Executive Director and Member of the Board of Directors at SAPA