DAS NEUE ONE-SHOT® AEROSCHILD ENTHÜLLT EIN REVOLUTIONÄRES GEHEIMNIS: DEINE UNTERBODENSCHUTZTEILE KÖNNTEN LEICHTER UND STABILER WERDEN UND KÖNNEN DIR INNERHALB VON 5 JAHREN 3,5 MILLIONEN EURO AN EINSPARUNGEN BRINGEN.
Heute habe ich dir etwas zu erzählen, das Dich mit Sicherheit sprachlos machen wird.
Wenn Du Dich fragen solltest, warum ich mich entschieden habe, diese Entdeckung zu teilen, nun ja, der Grund ist einfach.
Erstens, weil niemand besser als Du, der wie ich mit Leidenschaft diese Arbeit tut, um den Prozess, der uns antreibt, uns von Tag zu Tag zu verbessern, genau verstehen kann.
Zweitens bin ich sicher, dass Du auf diesen Seiten etwas finden wirst, das wirklich zu Dir passt, das Dich von vielen Problemen und Ärgernissen im Zusammenhang mit Deiner Arbeit befreien kann.
Ich möchte von einem Konzept ausgehen.
Es ist nicht mein Konzept, ich habe es mir aus einem Komikheft ausgeliehen, das ich vor langer Zeit gelesen habe und dessen Verfilmung ich zufällig gerade letzte Woche gesehen habe.
Nach dem Abendessen saß ich in der Küche.
Ich war immer noch sehr angespannt. Bestimmt kennst du auch solche Tage, an denen Du einfach nicht abschalten kannst?
Damals hatten wir es mit einem Kunden zu tun wegen einer neuen Komponente und ich wollte die perfekte Lösung für seine speziellen Wünsche finden.
Ich erinnere mich daran, dass ich den Fernseher eingeschaltet habe, um mich von diesem Gedanken abzulenken, um den Tag in Ruhe zu Ende zu bringen.
Seine unverwechselbare Maske tauchte vor mir auf und brachte die Geschichte wieder in Erinnerung.

Erkennst du ihn wieder?
Er ist das Gesicht von V, dem Protagonisten von V in Vendetta.
Ich habe diese Geschichte geliebt, aber es war wirklich schade, dass der Film seiner Zeit schon sehr weit voraus war.
Aber wenn ich richtig darüber nachdenke, muss ich sagen, dass das vielleicht doch eine gute Sache war, denn in diesem Moment war genau das, was ich dort sah, der Auslöser für meine Idee.
Seit einiger Zeit haben wir uns zusammen mit den Ingenieuren der Abteilung Innovation Engineering über das Aero Shield Gedanken gemacht, eine Komponente, die Du auch gut kennen wirst.
Wie Du weißt, handelt es sich um eine funktionale Komponente des Autos.
Aufgrund seiner Positionierung besitzt sie in der Tat keinen ästhetischen Reiz, ist aber zum Schutz des Fahrzeugs unerlässlich. Aus diesem Grund erfordert sie einige grundlegende Merkmale:
- Wärmebeständigkeit, denn es befindet sich in der Nähe des Auspuffrohres, wo an die 120 Grad Betriebstemperatur erreicht werden;
- Aerodynamik, um die Reibung auf Asphalt oder im Gelände zu reduzieren;
- Widerstand, gegen alles, was ihn vom Untergrund aus treffen kann.
Bei der traditionellen Methode wird diese Komponente in der Regel als aerodynamischer Schutz verwendet, der im Thermoformverfahren hergestellt wird.
Normalerweise wird das Teil im Thermoformverfahren hergestellt, um die Materialdicke sehr gering zu halten, so dass es bei der Fließbandmontage einfacher ist, ein Teil dieser Abmessungen (1,8 mm) weiterzuverarbeiten.
Abgesehen davon, dass es besonders leicht ist. Und du weißt, wie grundlegend heute dieser Aspekt ist.
Als Material wird Polyethylen verwendet, das in der Regel zur Herstellung von Produkten für den Haushalt verwendet wird.
In Autos wird es bei Low-Cost-Komponenten eingesetzt, an die keine hohen mechanischen und thermischen Leistungsanforderungen gestellt werden müssen.
Du wirst auch verstehen, dass es bei einem Bauteil, das langlebig sein muss, immer ein Risiko gibt.
Sobald das Stück hergestellt ist, wird die thermogeformte Platte auf eine Schneidemaschine gelegt und unmittelbar danach werden die Metallplatten mit einer Reihe von Aluminiumnieten mechanisch aufgebracht.
Die Nieten werden dann von den Monteuren befestigt, in der Regel werden zwei Personen auf je 18 Nieten benötigt, was einen hohen Arbeitsaufwand bedeutet.
Kurz gesagt, der Prozess der Herstellung eines Aero Shield, in seinen drei Phasen, ist ziemlich langwierig.
Bei genauerer Betrachtung dauert die Herstellung des thermogeformten Bauteils 180 Sekunden, aber es handelt sich nur um ein halbfertiges Produkt. Es sind noch eine Reihe weiterer Prozesse erforderlich: Bauteilkühlung, Schneidtechnik, Montage des Wärmeschutzes, Starlock-Montage.
Wenn man alles zusammennimmt, beträgt die Gesamtzykluszeit 420 Sekunden.
Wir haben erkannt, dass es notwendig ist, die Fertigungsweise dieses Bauteils grundlegend zu ändern.
Wie ich bereits sagte, es bedurfte einer Neuauflage des Bauteils.
Unsere Firmengeschichte hat uns gelehrt, Prozesse zu optimieren, sie zu rationalisieren und immer in Richtung Innovation zu gehen.
Ein Beispiel dafür ist das von SAPA patentierte One-Shot®-Verfahren: Es ist bis heute das schnellste System der Welt zur Herstellung von Automobilkomponenten mit:
- Weniger Gewicht
- Weniger Ausführungszeit
- Mehr Produktivität
Die One-Shot®-Methode ist ein realistisches Arbeitssystem, das auf verschiedene Komponenten anwendbar ist und die Erstellung leichterer Teile bereits in der Konstruktionsphase ermöglicht. Und nicht nur das.
Zu diesem Resultat tragen die Optimierung und die Automatisierung des gesamten Prozesses sowie die effektive Reduzierung der Arbeitsschritte bei, was als erste Konsequenz zu einem wesentlich schnelleren Ergebnis führt.
Zum anderen trägt es dazu bei, dem Aspekt der Nachhaltigkeit mehr Aufmerksamkeit zu schenken, indem es die Abfallentstehung deutlich reduziert.
Kurz gesagt, wir hatten ein Problem: die Notwendigkeit der Erneuerung des Aero Shield; wir hatten eine Lösung: die Anwendung der One-Shot®-Methode. Was uns aber fehlte, war die Verknüpfung dieser beiden Faktoren.
Und genau in diesem Moment kam mir eine der berühmtesten Szenen des Films V für Vendetta zur Hilfe.
Betrachte V als einen maskierten Kämpfer, der auf der Seite der Gerechtigkeit steht und der während des gesamten Films darum kämpft, respektiert zu werden.
Zum letzten Duell kommen nur sie beide, er und sein Feind.
In dem Moment, als V im Begriff ist, seinen Gegner zu töten, sagt er diesen Satz:
“Unter dieser Maske verbirgt sich nicht nur Fleisch und Blut, unter dieser Maske steckt auch eine Idee. Und Ideen sind kugelsicher.”
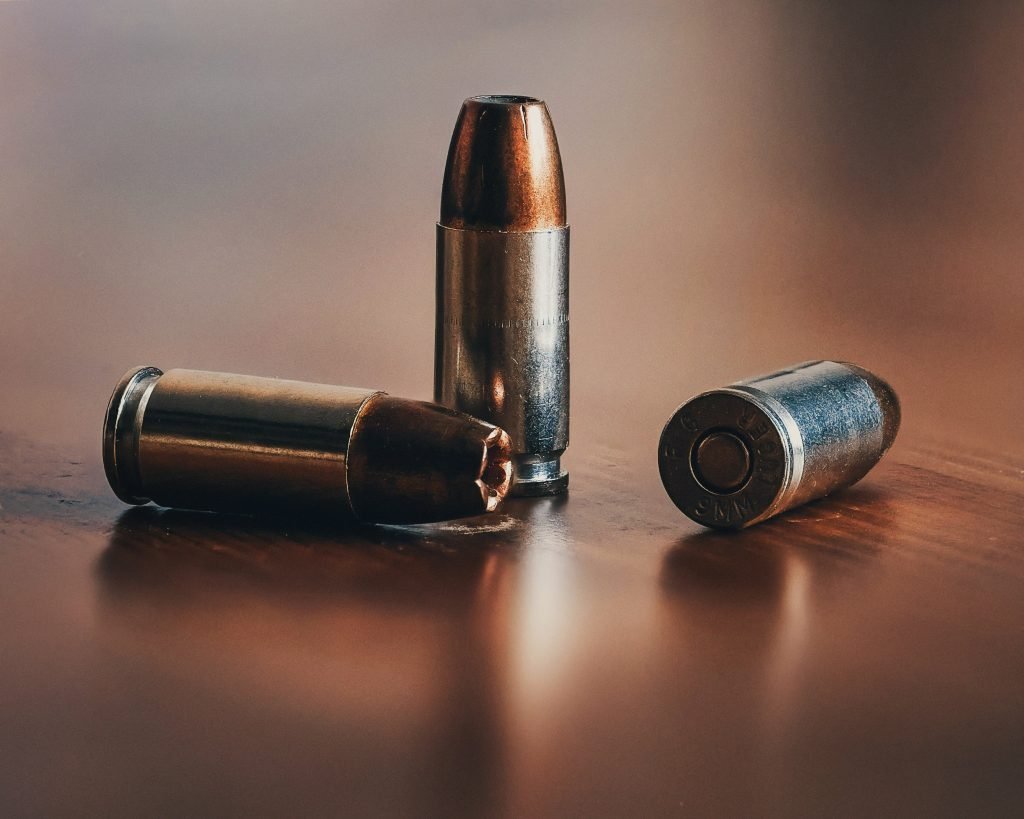
Das war ein Spruch wie für mich gemacht.
Warum?
Zunächst einmal, weil das SAPA-Logo ein Projektil ist. Zweitens war ich auf der Suche nach einer guten Idee, einer starken Idee, die sich völlig vom Alltäglichen abheben sollte.
Wir suchten nach einer Idee, die sich von allem, was bereits im Vorfeld erdacht worden war, unterschied.
Punkt drei: Unser Aeroschild musste stärker sein, es musste selbst kugelsicher sein.
Also?
Zunächst einmal mussten wir das Material ändern, mit dem wir es herstellen wollten.
Wir haben uns für ein Gewebe aus Preox entschieden, das eine sehr hohe Festigkeit besitzt, in einem Temperaturbereich von über 500 Grad liegt und das Aluminium ersetzt, wodurch die technische Leistungsfähigkeit deutlich verbessert wird.
Dadurch konnten wir auf ein Back Injection Moulding-Verfahren zurückgreifen, das darin besteht, eine invertierte Form mit der Hitzekammer auf dem immer fixierten und in Traktion befindlichen Teil herzustellen.
Das bedeutet, dass es nicht mehr nötig ist, das Aluminiumblech oder die Nieten zu applizieren, denn in der Praxis wird alles auf einen Schlag erledigt.
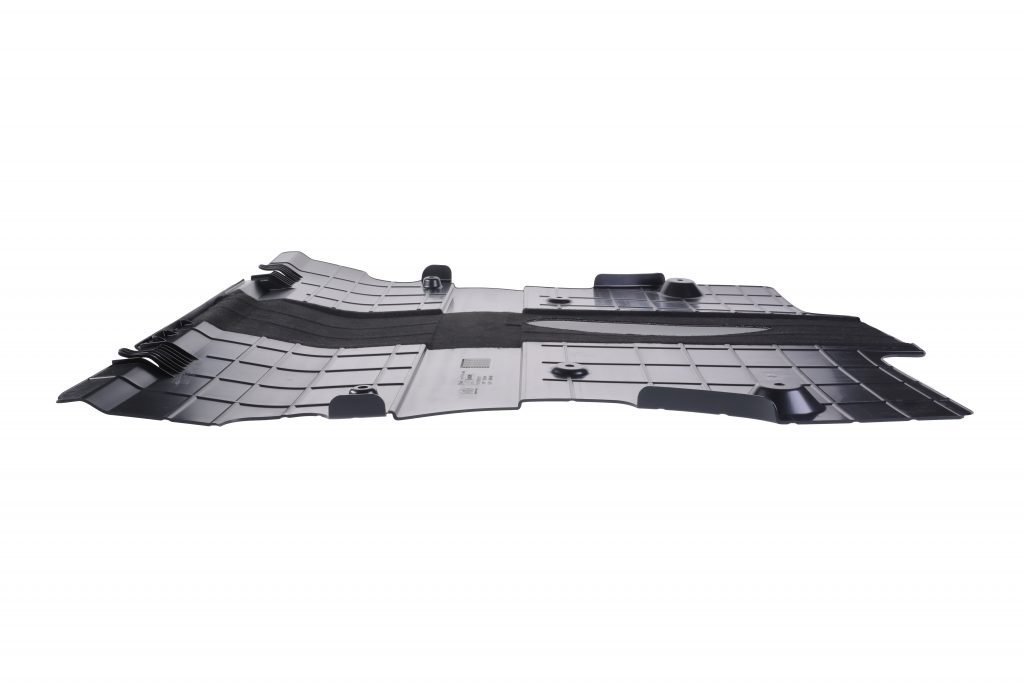
Eine kugelsichere Idee.
Das ist die One-Shot®-Methode.
Was bedeutet nun die Anwendung der Methode in Bezug auf die Aero Shield Innovationen?
- Mehr Qualität, ein stabiler, standardisierter und GARANTIERTER Prozess: Der Maschinenprozess ist zu 100% zertifiziert, während der Prozess mit dem Bediener eine geringere Qualität und eine größere Wahrscheinlichkeit hat, dass Unterschiede zwischen den einzelnen Teilen auftreten. Das bedeutet, dass Du Dir keine Sorgen mehr um Schwachstellen machen musst und Du sogar Fachkräfte einsparen kannst.
- Große Produktionskapazität und große Produktionsvolumen: 85 Sek. Zykluszeit bedeutet, 40 Stück/Stunde = 206 K Stück/Jahr zu produzieren, im Vergleich zu 47K Stück/Jahr bei der traditionellen Methode. Das heißt, die Produktivität ist unbegrenzt und es gibt keine Anlagenstopps.
- Vollautomatisierter und co-gedruckter Prozess, der sowohl die Fehlerquote als auch die mit der Montage verbundenen möglichen akustischen Störungen aufhebt. Eine innovative technologische Investition für Dich und Deinen Automobilhersteller.
- Reduzierung der Abfallentstehung: Durch die Optimierung der Phasen ist die One-Shot-Methode eine ökologischere Alternative. Du musst dir keine Sorgen mehr machen, neue Lösungen zu finden, die den Horizon 2020-Standards entsprechen, denn dies ist die ultimative Lösung für Dich.
Noch sind wir mit den angenehmen Folgen der One-Shot®-Methode nicht am Ende angelangt.
In der Tat, denn dieses System:
– eliminiert das Risiko von menschlichen Fehlhandlungen, da die Montagephase entfällt und somit auch die Gefahr von Fehlern ausgeschlossen ist. Du brauchst nicht einmal mehr eine Poka-Yoke-Maschine, um die Arbeit zu überprüfen.
– senkt die Kosten, sodass in 5 Jahren 3,5 Millionen Euro eingespart werden können und die Produktivität auf bis zu 500% gesteigert wird.
– ist ausgabefähig für das Elektroauto: da das System ohne Aluminiumnieten auskommt, welche in der Lage sind, elektrostatische Entladungen leicht zu absorbieren oder zu reflektieren, kann es für die neuen elektrischen Modelle verbaut werden.
Lass mich raten.
Du fragst dich, was wohl der Schwachpunkt dieses Prozesses ist.
In der Ergebnisbetrachtung gibt es keinen.
Natürlich war es nicht einfach, eine solche Technologie zu entwickeln. Das ehrgeizigste Ziel (und, ich gestehe, auch das schwierigste) war es, die Zusammenbauarbeiten zu eliminieren, und es kostete uns viele Tage des Studiums und der Tests.
Der Formprozess hat es uns ermöglicht, diesen Arbeitsschritt aufzulösen.
Was die Kosten betrifft, so kannst Du mit dem One-Shot® Aero Shield eine Produktion von 500% erreichen und so 3,5 Millionen in 5 Jahren einsparen. Aber es ist dennoch eine gute Investition.
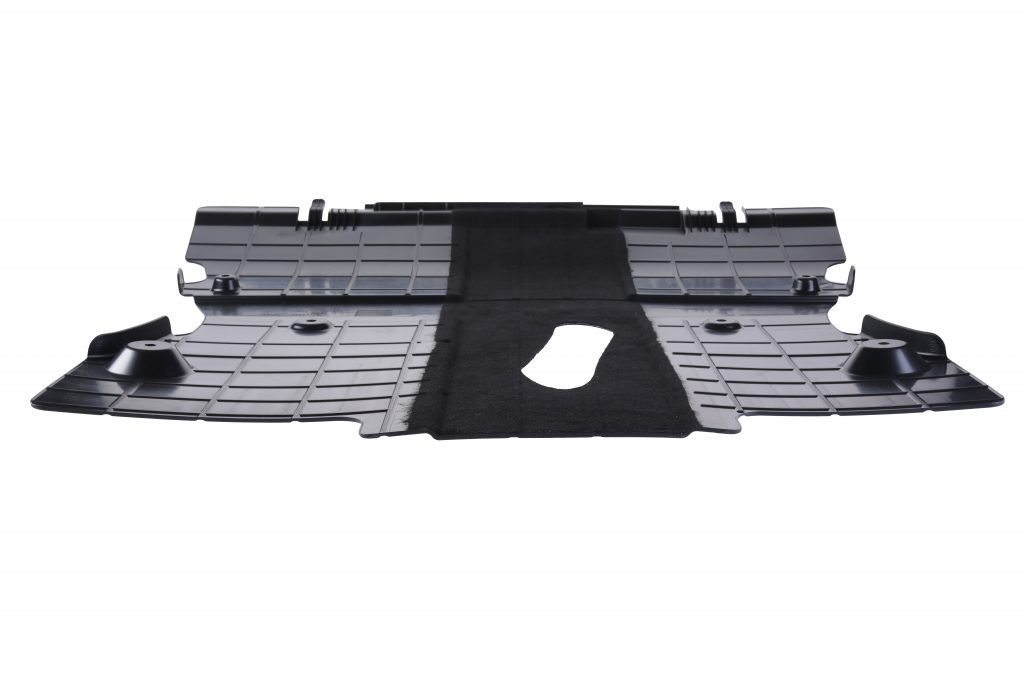
Alle Vorteile des One-Shot® Aero Shield zusammengefasst:
- Monolithisches Teil ohne Montageaufwand
- Leichtbaukomponente nach den Horizon 2020 Standards
- Geeignet für neue Elektroautos
- Produktivität von +500% im Vergleich zu herkömmlichen thermogeformten Verfahren
- Einsparung von 3.5 Mio Euro in 5 Jahren
- Unterbodenschutz eingespritzt und nicht thermogeformt
- Leiseres Auto, keine Sorgen mehr um Befestigungsnieten und den Fahrkomfort Ihrer Kunden
- Stabileres Bauteil durch Preox
- Automatisierter Prozess, d.h. garantierte Einsparungen sowohl bei der Fertigung als auch bei der Prozesssteuerung Poka-Yoke
Ich werde dir nicht sagen, wie die V-Geschichte endet, ich will dir deine Überraschung nicht nehmen.
Dass ich heute hier bin, um Dir davon zu erzählen, bedeutet natürlich, dass gute Ideen kugelförmig sind und über die Zeit hinweg unbeschädigt bleiben.
Bis bald.
Giovanni Affinita,
Geschäftsführender Direktor und Mitglied des Verwaltungsrats der SAPA
WENN DU MEHR ÜBER DEN NEUEN ONE-SHOT® AEROSCHILD ERFAHREN UND LEICHTERE, STABILERE UNTERBODENSCHUTZTEILE ERHALTEN MÖCHTEST, INDEM DU DAS THERMOFORMEN ENDGÜLTIG AUFGIBST, FÜLLE BITTE DAS FOLGENDE FORMULAR AUS.
DU WIRST INNERHALB VON 24 STUNDEN KONTAKTIERT!