Dies ist die Geschichte von Angelo Affinita – vom unerfahrenen Zimmermann zum Begründer der SAPA – und wie er, schon als junger Mann, die Anfänge des One-Shot®-Prozesses zum Leben erweckt hat
Ort: Santa Maria a Vico, ein kleines Dorf in Kampanien, in der Provinz Caserta.
Wann? Um die 60er Jahre.
Protagonisten: Angelo Affinita (mein Vater) und der Vater von Angelo (mein Großvater).
In der Affinita Tischlerei. Ein Tag wie jeder andere.
Vielleicht.
“Komm endlich mal weg von deiner fixen Idee? Ingenieure verstehen rein gar nichts!”
Fast hätte er es laut ausgerufen.
Angelo Affinita war im Familienbetrieb, in der Schreinerei von Fenstern und Türen bei seiner Arbeit.
Sein Vater, zwei Schritte von ihm entfernt, starrte ihn mit wütendem Gesicht an, sichtlich erschüttert. Er hatte die Geduld verloren.
Es war Abend geworden, und am Ende eines harten Arbeitstages hatte sich der Schweißgeruch ihrer Körper mit dem des Holzes vermischt.
Kein sehr angenehmer Geruch, aber ihre Aufmerksamkeit war gerade auf etwas ganz anderes gerichtet.
Sie waren allein und die Stille, die mehr Lärm zu machen schien als die Maschinen, die in der Werkstatt liefen, hielt einige Minuten lang an.
Angelo Affinita war ziemlich verwirrt, die Gedanken in seinem Kopf überschlugen sich und er suchte nach einer passenden Antwort.
Jene Antwort, die seinen Vater überzeugen würde. Etwas zu verändern, zu verbessern und nach vorne zu schauen.
Aber keine Antwort schien ihm gut genug.
Somit wandte Angelo seinen Blick in Richtung Tür und mit langsamen, zitternden Schritten gewann er den festen Boden zurück, der sie trennte.
Er legte seine Hand auf den Türknauf und indem er seine Handfläche fest darauf drückte, zog er ihn nach hinten und öffnete die Tür.
Er ging hinaus.
Wie konnte es passieren, dass Angelo und sein Vater, die immer eine gute Beziehung, ohne jeden Streit, miteinander hatten, eine so hitzige Diskussion führten?
Wir gehen an dieser Stelle einmal kurz einen Schritt zurück.
Beim Lesen dieser Geschichte wirst du dich sicher fragen, was das alles mit der Firma zu tun hat, die Kunststoffteile für Autos verkauft.
Und warum sollte das alles vor allem dich interessieren, der du ein vielbeschäftigter Ingenieur bist, der jeden Tag Autos baut?
Eine berechtigte Frage. Aber gib mir einen Moment und ich verspreche dir, dass es sich lohnen wird.
Um nämlich diese Frage beantworten zu können, solltest du den Grund kennenlernen, warum Angelos Vater die Ehre der Ingenieure, sagen wir es ruhig so wie es war, beleidigt hat. Um ehrlich zu sein, in diesem Moment hasste er sie sogar.
Du musst wissen, dass die Tischlerei Affinita in diesen letzten Monaten einen starken Aufschwung erlebte.
Die Auftragslage ging stark nach oben.
Seit einigen Monaten waren die Produktionsaufträge dermaßen angestiegen, dass das anfängliche Freudenlächeln…
…sich in eine Grimasse der Besorgnis verwandelt
hatte …
…und zu einer echten Verzweiflungsmiene geworden war.
Wie konnte es geschehen, dass ein Mehr an Bestellungen der Affinita-Zimmerei so viele Probleme bescherte und die Beziehung zwischen Angelo und seinem Vater beeinträchtigte?
Ich werde es dir sofort erklären.
Angelo und sein Vater standen in diesem Moment vor zwei großen Hindernissen.
Und ich wette, das sind zwei Probleme, die dir sehr vertraut vorkommen werden…
PROBLEM NUMMER 1:
DAS NERVIGE PROBLEM, SICH AUF ALLGEMEINE ZULIEFERER VERLASSEN ZU MÜSSEN

Wie du dir gut vorstellen kannst, ist die Erklärung einfach: Eine Tischlerei ist eine Firma wie jede andere.
Sie erbringt eine Dienstleistung oder erstellt ein Produkt, das auf dem Markt gegen Geld ausgetauscht wird. Je mehr Aufträge eine Tischlerei erhält, desto mehr Produkte muss sie auch liefern.
Aber dahinter verbirgt sich eine Falle:
Die Tischlerei hat, wie jedes andere Unternehmen, Lieferanten, von denen sie beliefert werden müssen.
Und genau das war für Angelo und seinen Vater das Problem.
Seltsamerweise haben viele Autohersteller der heutigen Zeit genau das gleiche Problem.
Denn mehr Aufträge zu bekommen bedeutet gleichzeitig auch mehr Aufträge an die Zulieferer zu vergeben.
Daraus folgen zwei Dinge:
→ Die Zulieferer erhöhen die Preise
Die Affinita Tischlerei wurde von solchen Lieferanten beliefert, die im Grunde gar nicht auf Schreinereien spezialisiert waren.
Was bedeutet das? Es bedeutet in Wahrheit, dass ein Anbieter, der auf verschiedenen Märkten verkauft, nicht über das Know-how, die Maschinen und das geeignete Personal verfügt und auch nicht verfügen kann, wie es eigentlich für einen speziellen Fachsektor nötig wäre.
Und wenn dieser Anbieter sich in Zeiten größerer Nachfrage mehr auf den einen als auf den anderen Auftrag konzentriert, wissend dass er nicht alle Kunden gleichzeitig bedienen kann, so kann er nur eines tun: seine Preise erhöhen.
Dieses führte im Falle der Affinita-Tischlerei dazu, dass ihre Gewinnspanne so stark herunterging, dass sie sich fragen mussten, ob es sich wirklich lohnt, für mehr Kunden zu arbeiten.
Es ist das gleiche Problem, das viele Autohersteller zur Zeit erleben.
Viele Anbieter von Kunststoffteilen sind gleichzeitig auch Hersteller von Haushaltsgeräten. Das bedeutet, dass ihre Maschinen NICHT auf die Herstellung von Kunststoffteilen spezialisiert sind.
Und nicht nur das, denn auch die Mitarbeiter können verständlicherweise nicht in derart vielen unterschiedlichen Bereichen ausgebildet sein.
Und was folgt daraus?
Vielleicht weißt du es schon…
→ Verzögerte Auslieferungen.
Kein speziell geschultes Personal für einen Fachbereich zur Verfügung zu haben, ist genau das Problem und dies führt unweigerlich zu Verzögerungen.
Selbst schon wenige Tage Verzug verursachen Probleme.
Denn eine große Nachfrage bedeutet auch verwaltungstechnisch viel Aufwand und verspätete Lieferungen, wenn auch nur wenige Tage, werfen die gesamte Lieferkette um.
Die Produkte wurden also zu spät ausgeliefert.
Und Verzögerungen bedeuteten verärgerte Kunden und höhere Produktionskosten.
Ich wette, dass auch dir aus heutiger Zeit derartige Probleme bekannt sind.
Und diese Probleme sind die Folge eines einzigen Hauptschuldigen.
PROBLEM NUMMER 2: DIE BEDEUTUNG VON INVESTITIONEN IN DIE FORSCHUNG
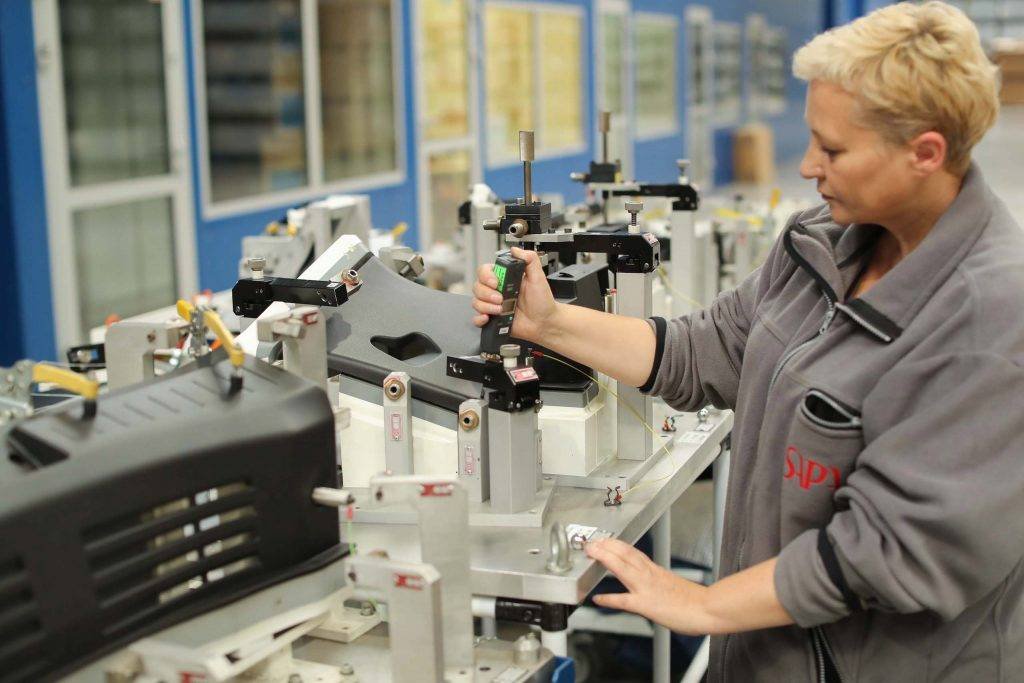
Die sechziger Jahre erlebten ein enormes wirtschaftliches und industrielles Erwachen und sogar in einem kleinen Dorf, wie dem von Angelo Affinita, war der Innovationsgedanke angekommen.
Die Kunden verlangten nach immer fortschrittlicheren und leistungsfähigeren Produkten, in immer kürzeren Lieferzeiten.
Allerdings waren die Lieferanten der Schreinereien weit davon entfernt, ihr Geld in neue Technologien zu stecken.
Denn oft bedeutete Forschung, in etwas zu investieren, ohne eine sichere Rendite zu erhalten. Das heißt, es mussten Risiken eingegangen werden.
“Diese technischen Sachen brauchen wir nicht” . Das waren die klassischen Gedanken derer, die damals eine Firma besaßen.
Und Angelos Vater war einer von ihnen.
Sowohl Angelo als auch sein Vater waren erstklassige Handwerker, fast schon Künstler, aber leider nicht schulisch ausgebildet.
Eines war Angelo jedoch klar: Man muss Neuerungen zulassen.
Dank eines alten Freundes hatte Angelo das verstanden. Dieser Freund nämlich hatte als einer der wenigen in dieser Zeit beschlossen, nach der Schule ein Studium zu beginnen und hat sich an der Fakultät für Ingenieurwesen eingeschrieben.
Angelo, der ein guter Beobachter war, lernte aus den Gesprächen mit diesem Freund, dass die Welt mit großen Schritten auf Innovation zuging und es galt hier mitzuhalten.
Er beschloss, ohne es den Vater wissen zu lassen, eine echte kleine, interne Forschungsabteilung zu errichten, die als Keimzelle dessen, was heute die Abteilung “Engineering Innovation” bei SAPA repräsentiert, anzusehen ist.
Die Auseinandersetzungen mit seinem Vater dauerten wochenlang an, aber Angelo gab nicht auf, und so schuf er selbst und mit Hilfe seines Freundes und einiger Handwerker, ohne das Wissen seines Vaters, Serienfenster und Serientüren, die ausgewählten Kunden angeboten wurden.
Es wurde ein Erfolg: Die Optimierung der Arbeitsprozesse und der Produktion beschleunigten die Gesamtproduktion und die Gesamtkosten konnten reduziert werden. Es verbreitete sich wie ein Lauffeuer.
Die Anzahl der Kunden stieg weiter an und jetzt konnten wirklich alle von ihnen zufriedengestellt werden.
Von diesem Moment an vertraute Angelos Vater seinem Sohn vollkommen und gemeinsam haben sie der innovativen Philosophie, die heute von SAPA in jeder Hinsicht repräsentiert wird, Leben eingehaucht.
Eine Philosophie, die die Erforschung und Optimierung von Prozessen als die beiden tragenden Säulen ihres Unternehmens betrachtet.
Und nach Jahren des Experimentierens und Ausprobierens liegt heute das Ergebnis vor, das wir “ One-Shot Methode®” nennen.
One-Shot® Prozess, das All-in-One Verfahren, das gleichbleibende Qualitätsleistung garantiert:
-weniger Gewicht
-weniger Kosten
– höhere Produktivität
bei der Herstellung von Autokomponenten
Dank dieser neuen Methode, die wir entwickelt haben, ist es uns gelungen, weltweit viele positive Auszeichnungen zu erhalten.
Wie beispielsweise das Projekt der “Super Dashboards”, das mit FCA und mit den Federico II Universitäten von Neapel und Salerno realisiert werden konnte, was der Artikel im Sole 24 Ore bezeugt.
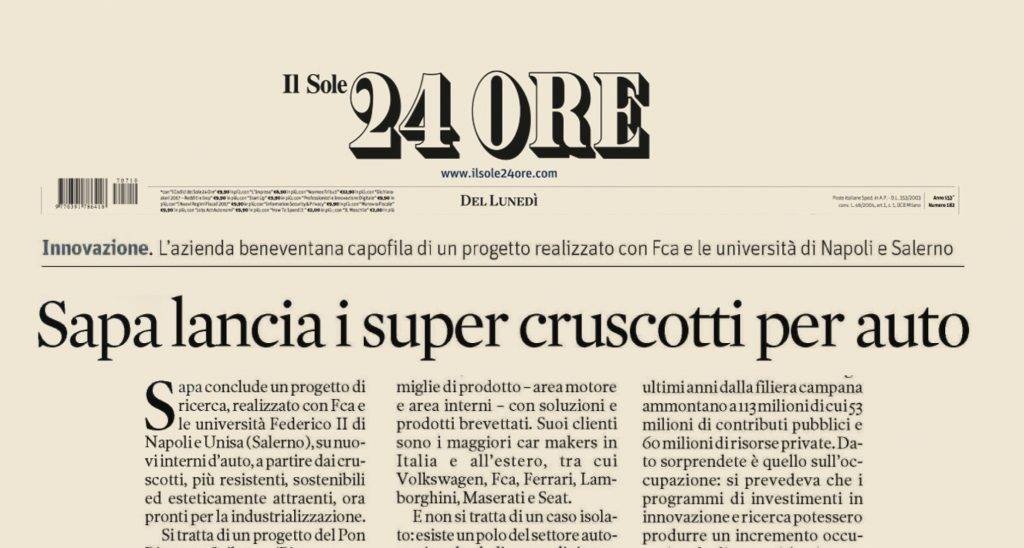
Auch beim Detroiter Innovation Award konnten wir eine Auszeichnung entgegen nehmen, eine Veranstaltung, auf der diejenigen Technologien prämiert werden, die im Automobilsektor den Unterschied machen. Wir haben dort mit unserem neuen Patent teilgenommen und haben, direkt nach dem Patent von Ford, unter ca 70 Teilnehmern den 2. Platz erreicht. Hier ein Artikel, der darüber berichtet hat:
Ein praktisches Beispiel des One-Shot® Verfahrens, mit dem uns die Realisierung eines Produktes gelungen ist? Ich erkläre es dir!
Wir konnten den One-Shot® Prozeß an einem schwierigen Bauteil, nämlich dem Kofferraumdeckel, den wir One-Shot® Window Frame genannt haben, anwenden.
Mit diesem Verfahren konnten die Produktionsphasen auf ein Minimum heruntergefahren werden und demzufolge auch die Produktionskosten drastisch gesenkt werden, was einen geringeren Endpreis zur Folge hat. Das geringere Gewicht, das erreicht wurde, wird zu einem immer wichtigeren Aspekt, da die neuen Umweltvorschriften diesbezüglich zunehmend strenger werden.
Zum Ende der 90er Jahre ging es mit einer konsolidierten Technologie los, die leider nie auf aktuellen Stand gebracht wurde
Bislang ist es so, dass der Stickstoffstrom, der in die Gussform eingespritzt wird, zur Entleerung des Zylinders mit dem Kunststoffmaterial führt, das gemäß dem Wärmeaushärtungsverfahren abkühlen und aushärten muss.
Ein Kühlvorgang, der vor allem an den Heckscheiben zu erheblichen Verformungen führt.
Überleg doch einmal: nach so viel Mühe und Arbeit muss man am Ende erkennen, dass die starken Verformungen des Bauteils Probleme beim Zusammenbau verursachen. Das ist schon sehr frustrierend.
Unser Lösungsvorschlag geht dagegen in eine andere Richtung, nämlich dahin dass wir einen thermoplastischen Kühlungsprozesses anwenden.
Ich zeige dir einige Bilder, auf denen die einzelnen Schritte des Arbeitsprozesses zu sehen sind. Einige sind identisch mit dem klassischen Gasentleerungssystem, andere geben bereits eine neue Richtung an.
Das für den Luftdurchtritt vorgesehene Loch ermöglicht es, das Bauteil ohne größere Verformungen und mit höherer Geschwindigkeit zu entleeren und zu kühlen.
Ein industrialisiertes System, das bereits von Volkswagen übernommen wurde und dir auf jeden Fall viele Sorgen abnehmen kann.
Die Lösung
Auf den Bildern konntest du sehen, dass indem der Stickstofffluss angehalten und ein kleines Loch gemacht wird, geht die Luft, sobald ich sie durchlasse, nicht in die Stickstoffkontrolleinheit, sondern in den Kanal und entweicht dann aus dem Loch, das ich geschaffen habe.
Der Vorteil
Der Innenraum wird durch Luft gekühlt und nicht per Wasserkühlsystem. Auf diese Weise haben die Deformationen viel geringere Ausmaße und liegen bei 1mm.
Solche Verformungen haben, wie du weißt, sehr unangenehme Folgen.
X Probleme bei der Montage und der Anordnung der Teile
X ästhetische Probleme aufgrund des nicht perfekten Zusammenbaus
X Lärmprobleme als Folge des schlechten Zusammenbaus
Wenn der Grad der Verformungen sich unterhalb eines Millimeters bewegt, dann gibt es entschieden weniger Probleme, wenn nicht gar keine.
Die ganze Mühe, die du in deine Arbeit gesteckt hast, wandelt sich von Frustration in Befriedigung. Das ist nicht schlecht.
Dank des Einfallreichtums und der Intuition eines jungen, unerfahrenen Zimmermanns ist es SAPA gelungen, einen immer höheren Stellenwert in Bezug auf Forschung und Innovation einzunehmen und Produkte wie den Window Frame zu erschaffen.
Forschung und Innovation sind zu den Grundpfeilern des Unternehmens geworden, so wie es sich Angelo Affinita immer erträumt hatte.
Zwei Faktoren, die wir dir gern zur Verfügung stellen möchten, dir, dem Ingenieur, der tagtäglich mit der Entwicklung neuer Autos beschäftigt ist.
Und das ist nur der Anfang.
Ich danke dir, dass du dir diese kleine Anekdote über den Ursprung des One-Shot® durchgelesen hast.
Es war mir ein Vergnügen, sie mit dir zu teilen.
Giovanni Affinita
Chief Sales Stratege und Mitglied des SAPA Verwaltungsrates