É stata annunciata lo scorso novembre l’uscita della F-Cell GLC Mercedes-Benz, un veicolo elettrico con cella a combustibile a idrogeno e tecnologia a batteria convenzionale ibrida plug-in per veicoli elettrici (PHEV), segno che l’auto del futuro è qualcosa che sta già accadendo adesso. Anche SAPA partecipa al cambiamento, grazie al Metodo One-Shot® e all’alleggerimento dei suoi componenti.
Fare parte di un cambiamento non è soltanto emozionante, ma ha a che fare con il gesto creativo.
L’idea di vedere nascere qualcosa che prima non c’era, immaginarla ancora prima che esista è un lusso che fa parte del nostro lavoro, anche se spesso ce ne dimentichiamo.
É quello che sta succedendo ora : il settore automotive sta cambiando, il suo rinnovamento non è più una periodica necessità di aggiornarsi ma un dovere per stare al passo con la ricerca tecnologica e le soluzioni più moderne.
L’esempio di Mercedes ne è la prova.
Il Suv F-Cell GLC è l’unico al mondo a non emettere CO2 durante il funzionamento ed è in grado di funzionare anche a idrogeno puro, possiede quattro modalità operative, che dipendono anche dalla scelta del programma di guida selezionato.
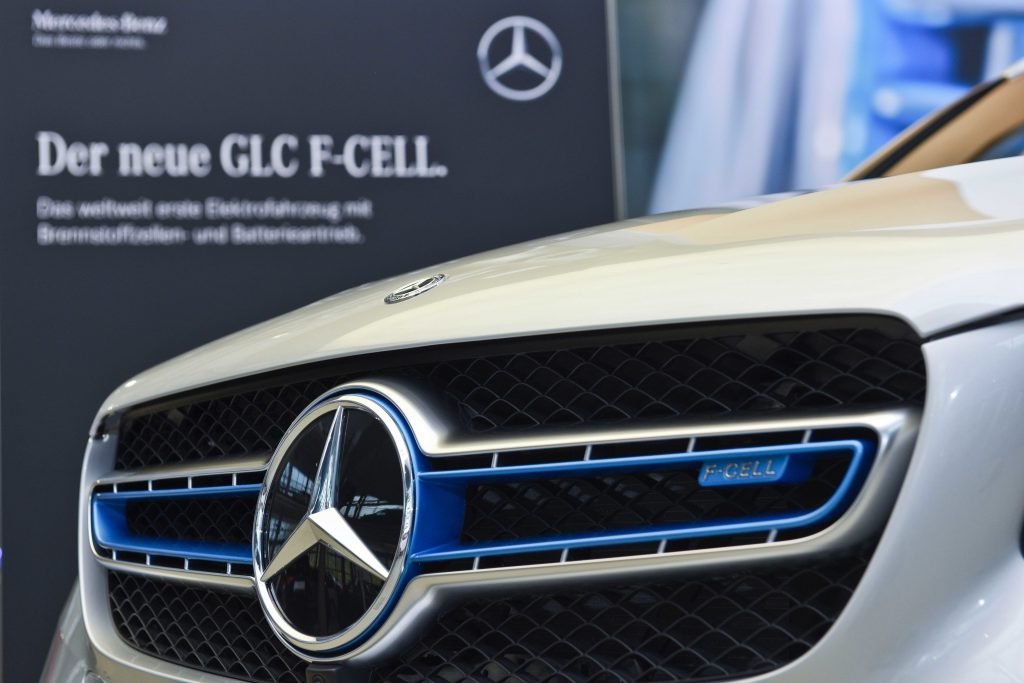
Immagino ne avrai sentito parlare.
Si tratta di una vera rivoluzione di cui sono felice che SAPA faccia parte, avendo contribuito con l’ideazione e la produzione del paraurti per questo specifico modello.
Del resto, sono convinto che non sia più possibile tirarsi indietro: il mercato sta percorrendo una direzione precisa. Oggi si cammina a passo spedito verso la riduzione delle emissioni, si lavora per trovare materiali meno inquinanti, le soluzioni alternative (come ad es. l’elettrico) iniziano a non essere più sperimentazioni ma alternative necessarie.
Da anni la nostra azienda sperimenta e attua soluzioni che, pur mantenendo alta la qualità del componente, tenga conto di questo rinnovamento interno del settore, risolvendo diversi problemi produttivi con cui ogni giorno siamo obbligati a scontrarci.
Le modalità per rinnovarsi sono molteplici. Quello che SAPA ha deciso di fare è concentrarsi su diversi aspetti, uno fra tutti: la riduzione dei passaggi produttivi.
Abbiamo cercato di agire sul processo ideando un vero e proprio metodo, il Metodo One-Shot®, che si pone l’obiettivo di razionalizzare le fasi di lavoro, riducendole al numero minimo di passaggi.
Per farlo, cerchiamo prima di tutto di automatizzare l’intero processo.
Puoi immaginare che i risultati siano immediati, in particolari in termini di risparmio di tempo.
Il Metodo One-Shot® è infatti conosciuto come il più veloce al mondo per realizzare componenti con:
- Minor Peso
- Maggiore Efficientamento Economico
- Alti Standard Qualitativi
Alla luce di questa scelta, fa parte della politica di SAPA quella di non appoggiarsi a fornitori esterni (ove è possibile, naturalmente), tagliando anche sul trasporto.
Ti porto l’esempio di uno dei nostri componenti brevettati One-Shot®.
Questo è il caso del One-Shot® Engine Beauty Cover in cui il processo tradizionale richiede:
- 3 operazioni di stampaggio per singolo componente: più costi di attrezzature, quindi più superficie occupata, più costi fissi e variabili;
- Più fornitori per un solo cover (in particolare per la parte del PUR schiumato): maggiori difficoltà di gestione e controllo del processo;
- Maggiori costi di trasporto e quindi maggior impatto ambientale
A questo vanno poi aggiunti un aumento del rischio, a una diminuzione del controllo del processo e a un aumento incontrollato degli sprechi.
Col Metodo One-Shot®, invece, questo non avviene perché il componente viene realizzato in un unico colpo di pressa (con un tempo ciclo di 60 secondi contro i 180 del processo tradizionale!), oltre a innumerevoli altri vantaggi come:
- Aumento della produttività del 300%;
- Un solo stampo, invece che 3 stampi: nel processo standard serve 1 stampo per il guscio rigido e ben altri 2 stampi di PUR;
- Il tempo ciclo passa da 180 secondi (necessari per stampo cover + stampo insonorizzante) a soli 60 secondi;
- Non c’è più bisogno di fissaggio con starlock perché ancorato chimicamente, quindi nessun bisogno di un operatore che li fissi sul cover o di un macchinario apposito;
- Maggiore sensazione di lusso, grazie a meno sfregamenti e rumorosità.
Sono quattro i componenti brevettati One-Shot® che presentano queste caratteristiche rivoluzionarie e innovative:
- One-Shot® Window Frame
- One-Shot® A Pillar Bicolor
- One-Shot® C lower Pillar
- One-Shot® Beauty Cover
Tutti sono già industrializzati e a breve SAPA ne presenterà un quinto in anteprima, il One-Shot® Aerodynamic Shields.
Per far sì che il cambiamento non ci trovi impreparati , credo che essere il cambiamento sia l’unica soluzione.
Mi rendo conto che non sia facile abbandonare ciò che si è sempre fatto, ciò che nel tempo ci ha premiato, che ha dato risultati, che è prevedibile, per qualcosa che invece si pone come un’alternativa nuova e potenzialmente potrebbe sfuggire al nostro controllo.
Ma se vogliamo davvero contribuire in maniera attiva al nuovo e non aspettare che sia qualcun altro a farlo al posto nostro, sono convinto che osare sia l’unica soluzione.
A presto.
Giovanni Affinita,
Executive Director e membro del Consiglio di Amministrazione di SAPA
Se vuoi scoprire come avere componenti più leggeri e approfondire tutti i vantaggi del Metodo One-Shot®, compila il modulo qui sotto.
Verrai ricontattato entro 24 ore!