It’s only a few days to the end of the year and 2020 could really be a landmark for the people that work in the automotive industry. Technological innovation and research are pushing towards a necessary change, but what does this mean concretely? Here is what GiovaNNI AFFINITA, SAPA’s EXECUTIVE DIRECTOR replied.
Have you ever observed the railway?
I don’t mean from the platform, but from near, as in if you ignored the metallic voice telling you not to go down on the rails and did go down.
If you look at the railway from down there, the rails at some point just disappear, and when I was a child, I really could not accept this.
Once I walked along the rails for a bit, I was with a friend of mine and we must have been 13 years old, tops. We walked a lot until we got to a point where this strange thing was no longer happening.
Because of the route and of the shape of the area, the rails took a strange turn and they were visible for many kilometres ahead.
Of course, the further we looked, the thinner the rail lines became but we could see that all that iron under our feet was going somewhere and did not just disappear.
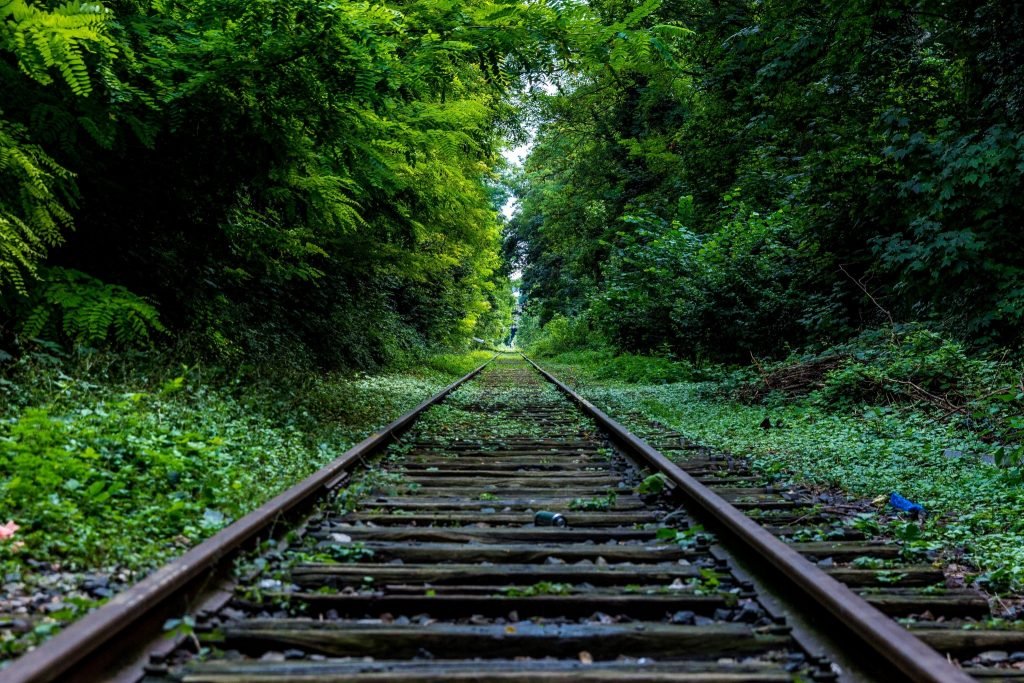
There is a reason why I’m telling you about this.
I think that this image perfectly summarises the current situation in the automotive industry, and by adjusting our look we can see what lies ahead in the future.
Is it so important that we know in advance?
Well, if you want your work to be acknowledged and if you don’t want to work twice as hard to reach your objectives (and want to make your boss happy), knowing what comes next is very advantageous.
At SAPA, we often talk about the visionary engineer, meaning that we like to think that we address people who are capable and have the courage of seeing what is currently but a mere forecast..
I think this is an important characteristic that makes a difference. Do you hear me?
Why you don’t need to be afraid of electric cars.
Many people say that the future of the car will be electric.
Just a few days ago we heard the news that Opel is developing an Opel Corsa e-Rally for Adac Opel e-Rally Cup; BMW organised a press conference at the new Competence Centre in Munich to analyse BMW today’s batteries and those of tomorrow and they said that they will be able to double their energy density by 2030, and by consequence the autonomy of the vehicles.
I could also tell you about the DS3 Crossback E-Tense, which is now available in full electric version: in short, the push towards electric cars is undeniable.
“Electric” is synonym with zero emissions, light weight and less waste. It encompasses a new concept of car and it brings one’s imagination to the future, especially for those who don’t work within the automotive sector, as they often associate these characteristics with “the new cars”, whereas the traditional cars already possess these characteristics, too.
What do I mean with this?
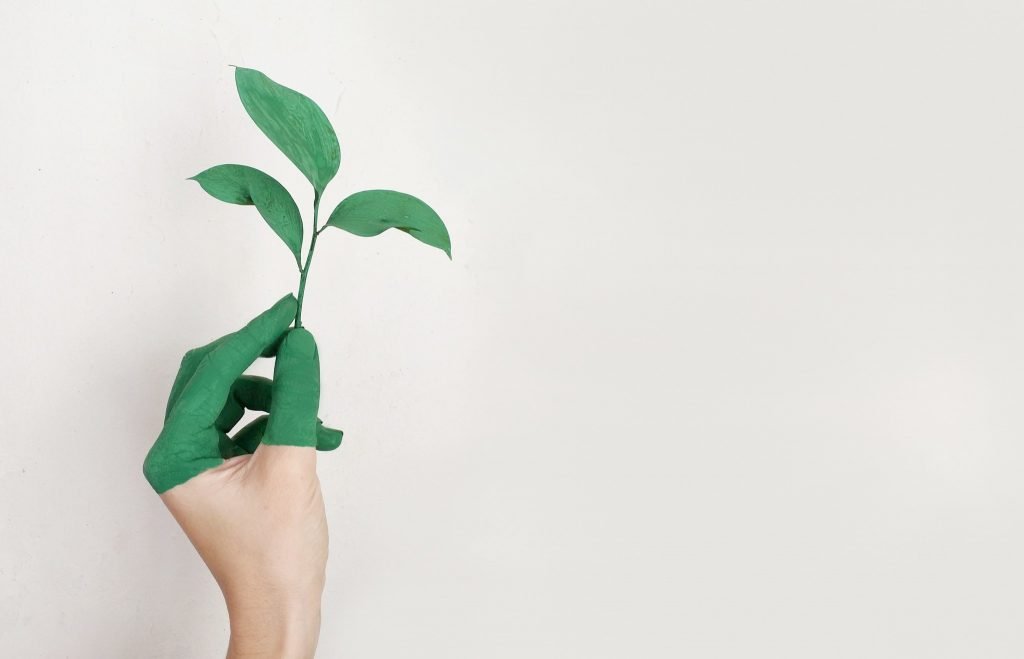
You know that electric cars have certain issues and maybe these are the reasons why this technology hasn’t soared yet and probably it won’t become the only option on the market. I am talking about costs, disposal issues, battery design and all the other issues that you know well about.
So, the question becomes: what can I do in the meantime?
There’s a lot you can do.
As we were saying earlier, the car market requirements in 2019 go towards reducing weight and waste. Do we need to wait for electric cars to reach these objectives? Most certainly not.
SAPA has started working on these aspects several years ago. Talk about rails, perspective and future direction!
It took much research and high investment but our efforts were successful in the end and we were able to create the One-Shot® Method, which reaches these objectives already in the designing phase.
Today the One-Shot® Method is recognised as the world’s fastest method to produce car parts with:
- Less weight
- Less waste
- Shorter time;
- Certified part quality.
The One-Shot® Method is a patented method.
What does this mean?
In the first place, that there is a patent number. And that it can be applied to all the parts made of advanced polymers and it is exportable – with the same advantages and the same results, to any production plant that you may decide to produce at.
This is possible because SAPA decided to make production leaner by dramatically reducing the number of phases.
The term One-Shot was chosen precisely for this reason: many parts are produced in just one press stroke; therefore, the traditional method was completely innovated.
Practically, most of the results that are associated with electric cars can be reached for the cars you’re producing right now as well, by lightweighting the parts from the design phase, by reducing waste caused by the many production steps, by delivering faster, and hence saving money.
Nobody would believe me when I said that the future of the car is made of plastic
I remember some years ago when the news came out that Mazda was researching the use of bioplastics for the car body: it was very surprising.
Mazda was not the first to do so (do you remember the collaboration between Ford and Heinz?), but they were the first ones to give notoriety to this issue.
And this issue was never exhausted, on the contrary it has become more and more topical.
Pollution is certainly the hot topic of the latest years and I am sure that it will remain high up on the list for a long time to come.
Our sector must take this proactive interest in environmental issues into account; I believe that this is a responsibility of those who want to produce cars.
SAPA internal research department, which we call Innovation Engineering, was created with the aim of anticipating – wherever possible and following these trends and to try and implement them.
The use of bioplastics and hybrid materials is certainly nothing new for SAPA.
The largest project that SAPA is involved in is called LIFE BIOBOCOMPO and aims at reducing CO2 emissions by 8% by June 2021.
The project began one and a half years ago and is now in the development phase, and with the support of the EU it aims at introducing composite materials in production.
You can keep up to date on its dedicated website and you can request more information from our Customer Care office.
Of course, the future is made of plastic, it is made of bioplastic!
How we can guarantee endless productivity for your car parts.
Over the past three years, we saw a huge change in the traditional setup of the automotive industry.
The companies that have always been considered as the automotive giants gave up this role to become something even bigger: several mergers and acquisitions created more complex industrial groups that aim at providing a more sophisticated offer than in the past.
The car today is no longer considered as an ideal and necessary item and it no longer defines one’s social status.
By consequence, this creates a distinction between those who use the car to go from A to B and those who use it as a luxury item.
The consequence of this evolution is that those who work in this sector must continue to sell cars but to do so they must become more competitive and reduce costs.
To survive one sole characteristic is necessary: uniqueness.
As you may know, SAPA is a family business that, in spite of a strong growth, has decided to keep some characteristics that are very important to us: in the first place, a strong connection with the local community, being a family run business and having an offer that can really make a difference.
When we started to work in this sector, creating a market for ourselves was particularly difficult for this reason: we were good, our product worked, and it was of good quality. But we were just like everyone else.
Why would anyone choose us over the known and trusted suppliers?
When our engineers began to work on the One-Shot® Method we decided that we would do something completely new, otherwise might as well leave it.
It took time, many trials and a lot of determination.
We started from the traditional method and we studied its limitations and we tried to improve it.
Reducing a whole process to just one press stroke means:
- Faster production, and therefore endless productivity.
- Less scraps, therefore higher environmental friendliness.
- Automated process and therefore reduced risk of human error.
- Fewer costs and the possibility to free up part of your budget to invest elsewhere.
In theory, it seems advantageous. But what will ACTUALLY happen to your daily work?
- IT IS PATENTED AS THE WORLD’S FASTEST METHOD TO PRODUCE CAR PARTS: this will maximise production and you will no longer have downtime
- MORE LIGHTWEIGHT PARTS: no more sleepless nights worrying about meeting the Horizon 2020 standards, you can dedicate the time you gain (yes, you will gain time) to new projects.
- PRODUCTION TAKES PLACE IN JUST ONE PRODUCTION AREA, WITH ONE SINGLE MOULD: this will make you save time and reduce waste significantly
- YOU’LL STILL HAVE HIGH QUALITY STANDARDS: you will able to guarantee a groundbreaking product that your customers love
- CAN BE APPLIED TO ANY TYPE OF PART: this will certainly impress your boss and it also means that you will no longer have to search far and wide for new solutions
- IT IS EXPORTABLE TO ANY PLANT AND DOES NOT NEED BEING ADJUSTED: your production line will stay the same and your parts will still have the quality standards that your customers require.
- HIGH DEGREE OF TECHNOLOGICAL AUTOMATION: you can reduce the human error margin (distraction, tiredness) and you will deliver on time while also keeping up to date with the sector innovation.
Clearly, such a process also brings along savings on costs, which is maybe the main reason why companies create ways of collaborating and huge groups that can carry the production costs.
If you look ahead on those rails and you look at how this industry is changing, it is possible to prepare for what’s coming and hence to stand out.
These are the solutions that we have found, and I am very happy to share them with you: if you weren’t there, what I do would be pointless.
I hope I have awakened your curiosity!
Kind regards
Giovanni Affinita
Executive Director and Member of the Board of Directors at SAPA
Would you like to find out more on the applications of the ONE-SHOT® METHOD that fit your requirements and have endless productivity?
Fill in the form below. we’ll get bacK TO YOU WITHIN 24 HOURS