The new Aero Shield designed and produced with the One-Shot® Method reveals a revolutionary secret: underbody shields can be lighter and more resistant. And they can make you save € 3.5 million over five years.
Today I would like to tell you about something that – I’m sure, will leave you speechless.
If you are wondering why I have decided to share this discovery with you, well, it’s very simple.
First of all, it’s because no-one can understand the deep dynamics that push us to seek to improve every day better than you do, since we share the same passion for our work. Secondly, I am sure that in these lines you will find something valuable for you, something that can solve a lot of big or small issues that you have in your work.
I would like to start out by quoting an idea. It’s not mine; I borrowed it from a comic strip I read a long time ago and that I saw the movie of just last week.
I was sitting in the kitchen after dinner. My mind was still very busy: you know, one of those days when you just can’t unwind. In that period, we were talking to a customer in relation to a new part and I wanted to find the perfect solution for their requirements.
I remember turning on the television to distract my mind and end the day.
His inimitable mask was right there on the screen in front of me and made me think of that story.
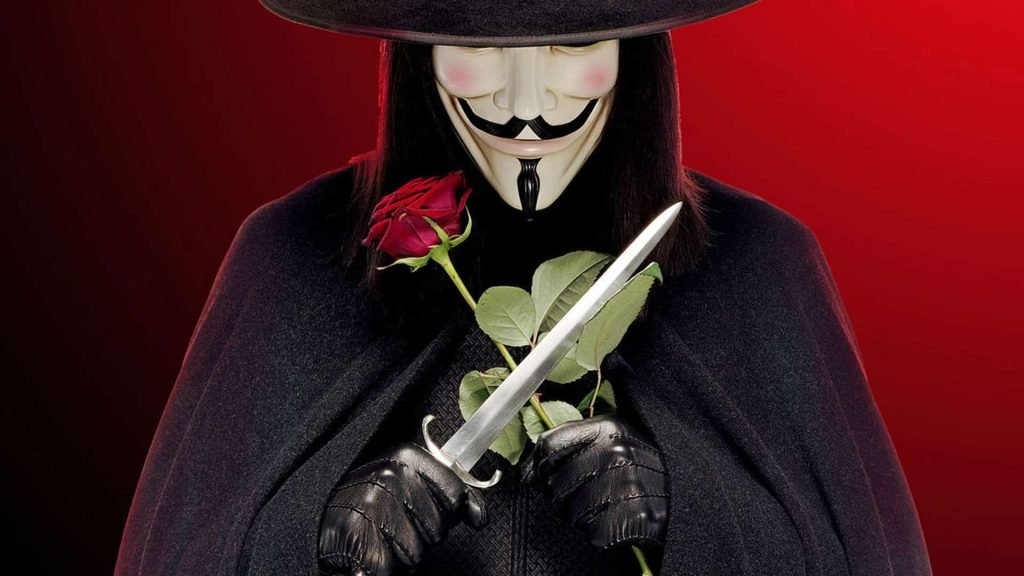
Do you recognise it?
It’s V’s face, the protagonist of V for Vendetta.
I loved that story and it was a pity that the film was already well into the story.
In fact, it was a good thing because thanks to what I saw in that very part of the film I got an idea.
Together with the engineers of the Innovation Engineering department, we had been asking ourselves questions about the Aero Shield, a part that you know very well.
As you know it is a functional part of the car.
Because of where it’s positioned, it does not have any aesthetic impact, but it is fundamental to protect the car. For this reason, it needs to have some crucial features:
- Heat resistance, since it is located next to the exhaust pipe where a temperature of 120° C can be reached;
- Aerodynamics, to reduce friction with asphalt or terrain;
- Resistance to anything on the ground that it may be hit by.
In the traditional method, the aerodynamic shield is a part that is regularly used and is produced by thermoforming.
This part is usually thermoformed in order for it to be very thin (1.8 mm), so that this big part is easier to handle while it is being installed on the vehicles. Additionally, the thermoformed shield is very lightweight. And you know how critical this aspect is today.
The material used is polyethylene, which is generally deployed for household products. On cars, on the other hand, it is normally used for low-cost parts that are not expected to need to have extraordinary heat and mechanical performances.
So, you realise that this is a big risk when it comes to a part that needs to be resistant.
Once the part is created, the thermoformed sheet is put in a cutting machine and after this, the metal sheets are mechanically applied also with a series of aluminium rivets.
The rivets are then secured by the operators – usually two operators are needed every 18 rivets, so this means a large deployment of human resources. And the Aero Shield three-phased production process proves to be quite long. If you think about it, you need 180 seconds to produce the thermoformed part. But this is an unfinished product and still needs further processing: cooling, cutting, assembly of the heat shields and assembly with star locks.
This means that the full cycle time is 420 seconds. We realised that we had to radically change the method of production for this part.
As I was saying, we needed to innovate this part. Our company history taught us to optimise processes and make them leaner and to always invest in innovation.
The One-Shot® Method patented by SAPA is an example of this attitude: to date it is the world’s fastest method to produce car parts with:
- Less weight
- In shorter time;
- More productivity.
The One-Shot® Method is a working system of its own, it is applicable to several parts and it allows us to produce more lightweight parts from the design phase. And not only that.
This result is obtained by optimising and automating the entire process, thus reducing the number of phases, which consequently makes the process quicker. Secondly, this caters for more sustainable production and reduces waste.
To sum up: we had a problem, i.e. we needed to innovate the Aero Shield; we had a solution: the implementation of the One-Shot® Method. We were missing the solution to bridge the gap. And in this respect, I was helped by one of the most famous scenes of the film V for Vendetta.
Consider V as a fighter with a mask who is on the side of justice and fights for justice for the whole duration of the film.
Only two characters make it to the final duel: him and his enemy.
As V is about to kill him, he says these words to his enemy:
“Behind this mask there is more than just flesh. Beneath this mask there is an idea and ideas are bullet-proof.”
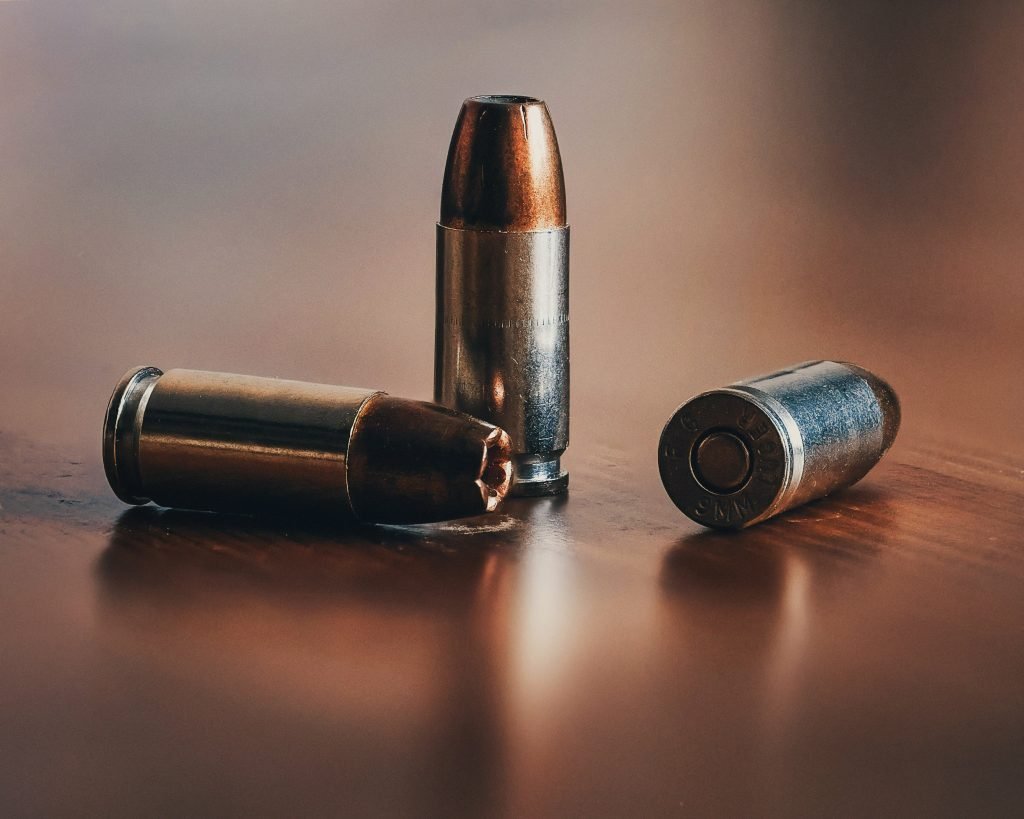
That sentence was for me.
Why?
First of all because SAPA’s logo is a bullet. Secondly: I was looking for a good idea, a resistant idea that is completely out of the ordinary.
I was looking for an idea that is different to anything that had already been thought before.
Thirdly, our Aero Shield needed to be more resistant: it needed to be bullet-proof itself. So?
Firstly, we needed to change the material that it is produced with.
We decided to use a carbon peroxide cloth, which is highly resistant – it can withstand 500 degrees, and substitutes aluminium, thus improving the technical performance. This allowed us to go for Back Injection moulding, which consists in using a reverse mould with the heat cavity on the fixed part and with traction of the fixed part. This eliminates the need for the aluminium sheet and for the rivets: in short, everything is produced in just one shot.
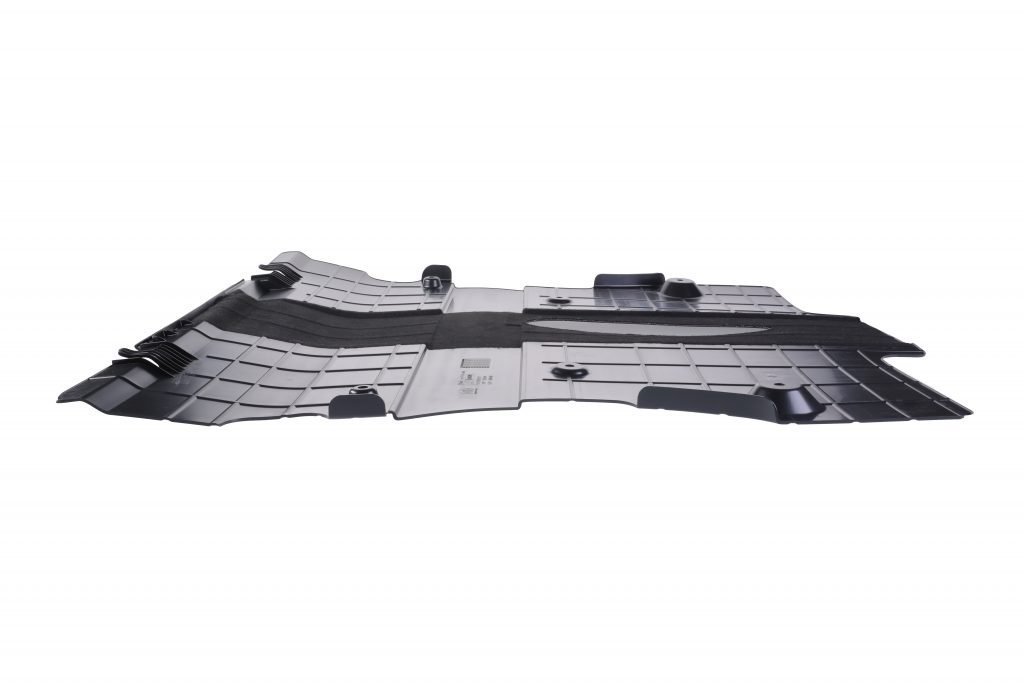
A bullet-proof idea.
This is the One-Shot® Method.
What does applying the One-Shot® Method to the new and improved Aero Shield entail?
- Better quality and a robust, standardised and GUARANTEED process: the machine-based process is 100% guaranteed, while the operator-based one has higher risk of there being differences among the pieces.
This means that you no longer need to worry about imperfections, and you can save on specialised workers. - High production capability and high volumes: 85-second cycle time means that you can produce 40 parts per hour = 206K parts per year against the 47K parts per year with the traditional method.
This means that you will have endless productivity with no down-time. - Fully automated and co-moulded process that eliminates the risk of error and the potential noise issues deriving from assembly.
An innovative investment in technology for you and your car maker - Waste reduction: because it optimises the process phases, the One-Shot® Method is a more environmental-friendly alternative.
You won’t need to worry about finding new solutions that are in line with the Horizon 2020 standards, because this is the ultimate solution for you.
The positive consequences of the One-Shot® Method don’t just end here. As a matter of fact, this method:
– eliminates the risk of human error: by eliminating the assembly phase, there is no risk of error. There is no longer any need for Poka-Yoke machines to control the operator.
– reduces costs and can make you save up to €3.5 million over five years and increase productivity by 500%.
– can be applied to electric cars: because the part does not need aluminium rivets that may absorb or reflect electrostatic discharge, it can be easily used on the new electric vehicles.
Let me guess. You are wondering what the weakness of the process is. In terms of the results obtained, it has no weaknesses. Of course, creating this technology hasn’t always been easy. The most ambitious objective (and, I have to say, the most difficult one to achieve) was eliminating assembly, and this took many days of study and of tests.
We could solve this issue by opting for moulding.
In terms of costs, the One-Shot® Aero Shield allows us to reach a 500% increase in production and to save up to €3.5 million over five years. It is in any case an investment.

In short, the advantages of the One-Shot® Aero Shield are:
- One single piece that does not require assembly.
- Lightweight part in line with the Horizon 2020 standards.
- It can be used on electric cars.
- Productivity increases by 500% in comparison to traditional thermoforming.
- € 3.5 million savings over five years.
- Underbody shield is injected and not thermoformed.
- Quieter cars, and you will no longer need to worry about securing the rivets and about the comfort of your customers.
- More resistant part thanks to the use of carbon fibre.
- Automated processes, which means guaranteed savings both on manpower and on the Poka-Yoke control system.
I won’t reveal how V’s story ends, as I don’t want to spoil it for you in case you haven’t seen it.
But me being here today writing about this story proves that good ideas really are bullet-proof, and they stand the test of time.
Kind regards,
Giovanni Affinita
Executive Director and Member of the Board of Directors at SAPA
If you’d like to know more about the new One-Shot® Aeroshield and if you’d like to have more LIGHTWEIGHT AND more resistant underbody shields and eliminate thermoforming for good, fill in the form below.
WE’LL GET BACK TO YOU WITHIN 24 HOURS!