More and more aspects of our lives are being reoriented to become ECO-FRIENDLIER, and the automotive industry is also demanded to do its bit.
Is this an impossible endeavour? Not at all.
Sunday morning reading the papers and having breakfast at the café. A ritual to honour, especially when – after an extremely long winter – summer starts to treat us to hot and slow days that pre-announce holidays.
I have just received my coffee and I enjoy its aroma for a moment before drinking it in one shot, as I like to do. My eyes spot an article where the words Barbie and Lego bring me back to my childhood in no time. I start reading the article.
The beginning is sharp: “No more Barbie nor Lego”. It captivates me.
In the States, the zero-waste movement has affected the toy industry, which is worth around $89 billion – not exactly peanuts! A movement of parents committed to environmental issues began to propose new and alternative toys and to refuse plastic toys, except for the second-hand ones.
My coffee is still hot, my hand is on the cup, but my mind is too busy to enjoy the coffee.
As a matter of fact, besides using plastics as the main material, the toy industry also must factor in that their products are disposable by nature: it is normal that a child leaves a toy behind to play with a new one. Of course, if this is just a whim, it can be avoided, but looking for a toy that is more suitable for the child’s age while the child grows, is part of the natural growth process.
The question is already on the tip of my tongue; I drink my coffee over it.
As I put down the cup, I can formulate it better: caffeine has entered my system.
Will this happen to the automotive sector as well?
And if so, when?
But most importantly, will we be ready?
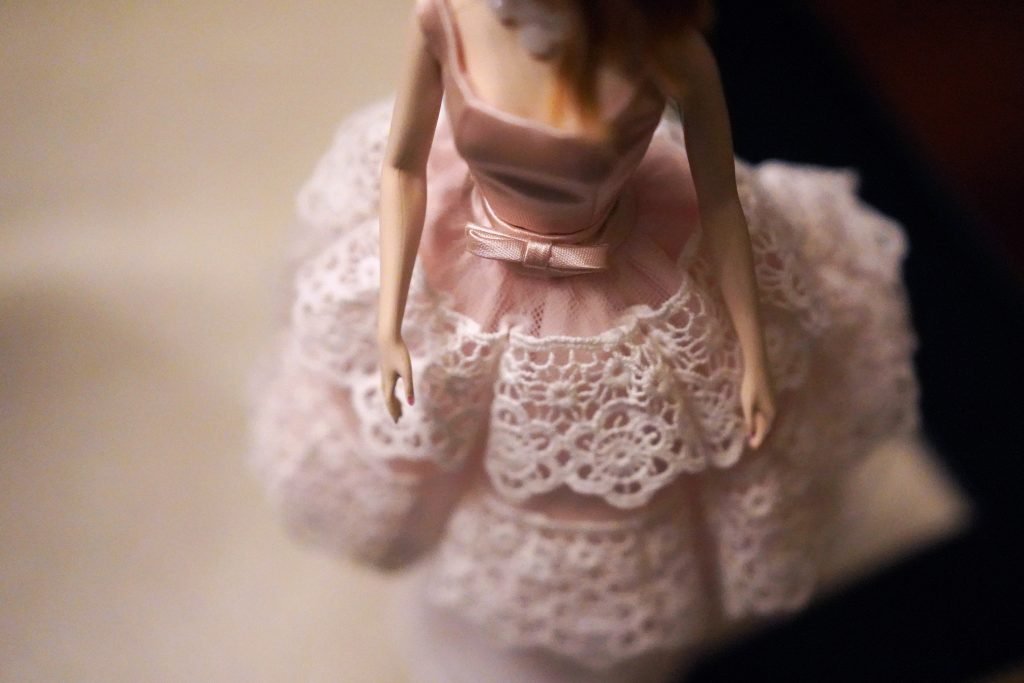
It is clear that something is changing, something very big.
What strikes me the most is not the issue in itself – which my company and myself have already been asking ourselves questions about, but rather realising that iconic and successful brands are rethinking their products.
Somehow, they are questioning themselves, and this is the sign of irreversible change.
The article concludes by quoting some of the concrete commitments that the most important businesses in the sector decided to make: Lego committed to marketing sustainable building blocks by 2030, Mattel has already added instructions how to recycle the toy parts once no longer used and Hasbro will start using only recycled plastics as of this year. The idea is therefore to keep the product unaltered in its essence and to work exclusively on the materials used. The objective is clear: in first place, leaving the nature of the product unaltered, and in the second place, not losing the trust of loyal customers.
An intuition that resonates a lot with me.
SAPA, as a matter of fact, specialises in moulding plastic parts for the automotive sector: we have been working for years on lightweighting the parts starting from the designing phase.
How do we do that?
I am keen on explaining this because it could be very helpful for you.
The first solution we’ve found is the One-Shot® Method, maybe you’ve already heard about it. It is currently the world’s fastest production system to create car parts. It guarantees certified quality standards with:
- Less weight
- In shorter time;
- Less waste.
How is this possible? By simplifying production phases as much as possible and, in some cases, by getting to produce the part in just one shot, thanks to innovative moulding machines.
In this way the part:
– is more lightweight because it is designed and created using less material, so this helps you make your boss happy;
– is more sustainable because less plastics is used and because work was concentrated in just one production island, and this is in line with the Horizon 2020 standards.
– is produced in shorter time than with the traditional method because the entire process was optimised; this in turn avoids delivery delays and favours what we call “infinite productivity”.
For us the One-Shot Method is not only a convenient and revolutionary solution but a real work philosophy.
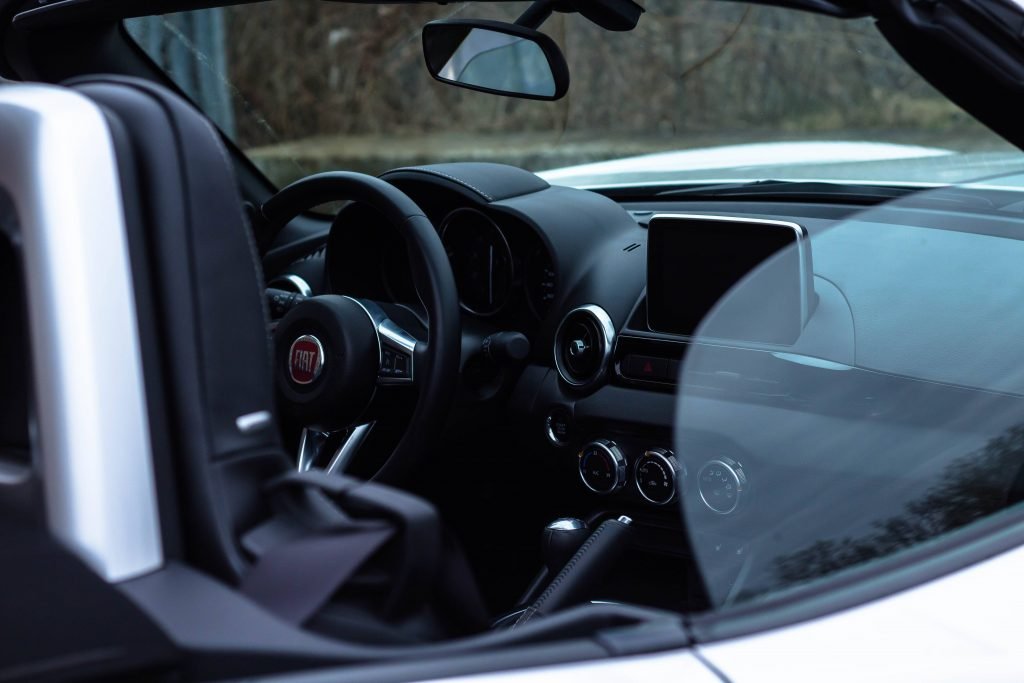
Clearly, this is not the only possible solution, nor the only one we implement.
SAPA has been taking part in the LIFE BIOBCOMPO project for about one year, together with SOPHIA, CRF, FCA and with the support of the European Union; the project aims at reducing CO2 emissions by 8% by 2021.
This research rests on the idea of developing thermoplastic low-density materials and of using bio-based fibres. It is common understanding that a 10% reduction in the vehicle’s weight has the potential of saving 6-8% of fuel and since a lighter object needs less energy to accelerate than a heavier one, more lightweight materials clearly provide for a better way to optimise fuel consumption and to reduce greenhouse gas emissions.
The objective of the LIFE BIOBCOMPO project is not only to reduce vehicle emissions but to produce such lightweight composites at costs that are compatible with the customer’s requirements and to make sure that the new materials will be completely recyclable at the end of their life cycles.
As I was saying earlier, for me this is no new topic but one that becomes more urgent by the day because it affects many sectors of our lives and for this reason, it requires 100% of our attention.

Just to quote another example: at SAPA we have installed around 10,000 m2 of solar panels over five plants, which results in a decrease in CO2 emissions by around 4,500 T.
As I was saying earlier, the One-Shot® Method is an outlook that encompasses not only our way of working but it is also our way to look at the world.
We committed to this outlook and we didn’t have to wait long for the results: last November the One-Shot Method was presented at the IZB in Wolfsburg for the first time and it aroused the interest and the attention of the stakeholders and of the press.
I believe that today we can’t avoid looking at our work in a different way.
It is certainly not an easy challenge to face.
But this does not mean that it is an impossible one.
Kind regards,
Giovanni Affinita,
Executive Director and Member of the Board of Directors