Grazie al Metodo ONE-SHOT®, la Jeep Renegade è oggi l’unico modello al mondo ad avere un montante a bi-iniezione, il One-Shot® A Pillar Bicolor. Questo processo elimina i problemi di sicurezza e le imperfezioni legate all’assemblaggio dei componenti, riducendo l’impatto ambientale.
Questa storia inizia a Roma, sul Lungotevere.
Erano circa le sei del pomeriggio, camminavo spedito: avevo un appuntamento e volevo arrivare con un po’ di anticipo. Lo sguardo fisso sui piedi mi aiutava a concentrarmi su quello che avrei voluto dire durante l’incontro.
Forse per quello non mi accorsi di un gruppo di ragazzi che ingombravano il passaggio, guardavano tutti nella stessa direzione.
Chissà quante volte sarà capitato anche a te di avere la testa altrove.
Non avevo notato un dipinto di papaveri, farfalle e lucertole che colorava la muraglia sopra al fiume, distruggendo il grigio della città.
“Certo, qualcuno con una bella mano è passato di qui”, pensai. E andai oltre.
L’aneddoto potrebbe finire qua, ma c’è dell’altro.
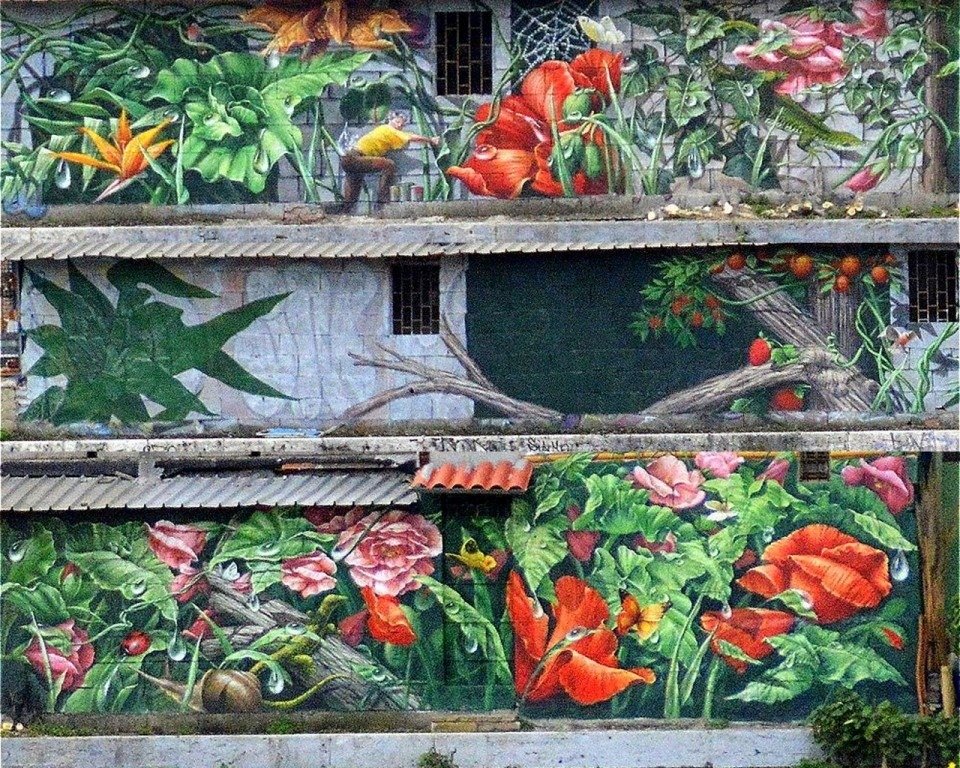
Di certo ti starai chiedendo cosa c’entri questa storia con il primo montante a bi-iniezione, ideato e testato dalla nostra azienda.
Te lo spiego subito.
Quello scorcio mi aveva colpito.
Scoprii che quella parete così curata non era che la baracca di Laura Galletti, una ex grafica milanese divenuta clochard per scelta.
Aveva dipinto di bellezza uno spazio ristretto, trasformandolo con piccole attenzioni in qualcosa di unico e inimitabile. Un bel luogo dove stare.
Questa storia mi è tornata in mente qualche tempo fa, quando Jeep si è affidata a noi per una richiesta un po’ particolare.
Lo stimolo è venuto dal modello della Jeep Renegade, un’automobile maestosa con un montante laterale alto estremamente ampio, che rischiava però di dare un aspetto opprimente all’abitacolo.
E sai bene quanto sia essenziale creare un luogo di viaggio confortevole e esteticamente curato.
Il nostro reparto di ingegneria si è messo subito a lavoro per trovare la soluzione più adatta che potesse conciliare la bellezza dell’auto con la sua prestanza.
Inizialmente abbiamo pensato di stringere il montante anteriore con un inserto di plastica. Questa soluzione, però, non risultava efficace a livello di sicurezza, in particolare qualora ci fosse lo scoppio dell’airbag.
È stato allora che l’idea si è fatta spazio: un montante stampato a bi-iniezione che permettesse di creare pezzi bi-colore e non assemblati.
Come è possibile? Ti starai chiedendo.
Ecco il procedimento:
Per prima cosa viene stampata la parte grigia. All’interno dello stampo sono stati creati dei chiodi, che provocano la presenza di piccoli fori sul pezzo. Quando il pezzo è pronto viene preso dal manipolatore, lo stampo ruota e si richiude.
Un estrattore, arretrando, crea un cilindro più largo ai fori.
A questo punto viene stampata la parte nera che quindi non si aggancia solo meccanicamente, ma il polipropilene si attacca chimicamente (circa a 200 gradi), infilandosi nei fori.
In questo modo, quando viene iniettata la parte nera, si crea una testa di fungo nella parte interna del pezzo e i due componenti risultano collegati meccanicamente.
In parole povere?
Quello che ieri dovevi stampare con due diversi stampi e poi assemblare in un secondo momento, oggi avviene – come diciamo noi – in un solo colpo. Nasce così il One-Shot® A Pillar Bicolor.
Ecco cos’è il Metodo ONE-SHOT®: la possibilità di semplificare, ottimizzare, velocizzare la produzione dei componenti auto. Con i seguenti, piacevoli, effetti collaterali:
- i tuoi componenti saranno più leggeri, migliorando la dinamica e la stabilità dell’autovettura;
- il monolito a bi-inezione non necessita di assemblaggio: in questo modo ridurrai il rischio di imperfezioni nel momento dell’accoppiamento;
- gli scarti verranno ridotti, diminuendo l’impatto ambientale.
Questa tecnica è stata quindi applicata al modello Renegade, a oggi unica automobile ad avere questo tipo di montante.
L’unicità è data anche da un altro risultato: far ruotare uno stampo da 120 quintali all’interno di una macchina da 1500 tonnellate, quando solitamente si usa stampare la plastica con tavolo rotante e su macchine di piccole dimensioni.
L’obiettivo è stato dunque raggiunto: migliorare l’abitacolo e risolvere il problema dell’airbag.
Ma non solo.
Ci siamo accorti che il sistema di stampa a bi-iniezione con tavola rotante consente di ridurre i costi poiché montaggio e assemblaggio avvengono in un unico passaggio: il componente che si ottiene è infatti monolotico.
In situazioni “normali” sarebbe necessario stampare e poi unire i pezzi o con ultrasuoni o con lama calda oppure con vibrazione. Proprio per questo, il pezzo risulta più leggero: non è più necessario creare i piolini per la sovrapposizione delle diverse componenti.
Infine, avere un elaborato monolitico in bi-iniezione garantisce una maggiore precisione, a differenza dell’assemblaggio classico che richiede sempre una previsione di tolleranza.
Questo è l’unico sistema, dunque, che ti permette di:
- racchiudere due processi in uno, riducendo i tempi di produzione e accorciando i tempi di consegna;
- eliminare il passaggio dell’assemblamento, questo ti permetterà di abbattere i costi;
- creare un componente ad hoc, ponendo così una particolare attenzione all’estetica del prodotto, che sai quanto sia un valore essenziale, quando si tratta di automobili.
A questo bisogna aggiungere che il prodotto risulta migliorato anche in termini di precisione e leggerezza.
Ovviamente lo stesso procedimento è replicabile anche su altri modelli di automobili.
Un esempio potrebbe essere la mensola posteriore della Panda, che SAPA produce già da diversi anni: la bi-iniezione permetterebbe di risparmiare la saldatura e la manodopera.
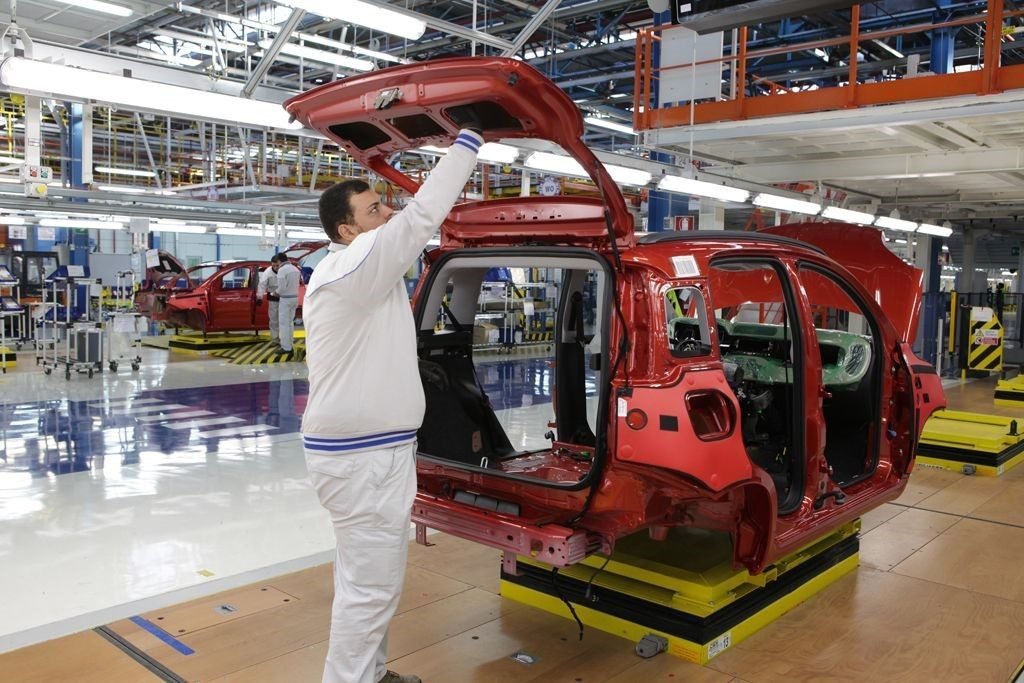
Certo, ti starai chiedendo quali siano i punti deboli di questo processo così innovativo.
Per quanto riguarda il risultato, nessuno.
L’unico apparente ostacolo riguarda la necessità di avere una pressa di ultima generazione, una tavola rotante perfettamente efficiente e quindi un investimento economico importante da parte dell’azienda: i costi relativi a questo prodotto ammontano circa a 800 mila euro (macchina 500 mila, tavola rotante 200 mila, gruppo satellite 100 mila) per introdurre una produzione di due anni.
Per riprodurre questo prodotto è necessario investire.
In SAPA l’abbiamo fatto, non soltanto in ottica di ottimizzazione futura, ma soprattutto come strumento di ricerca che sta alla base del nostro lavoro, del nostro impegno e del metodo ONE-SHOT®.
Il Metodo ONE-SHOT® è infatti il metodo più veloce al mondo per produrre componenti auto, l’unico che ti garantisce le stesse performance di qualità per i tuoi componenti auto con:
– meno peso
– meno costi
– più produttività
Da sempre ci accompagnano ricerca e innovazione, la spinta al sogno originario di mio padre, Angelo Affinita, i principi che guidano le nostre scelte e la nostra azienda.
Così come la piccola casa di Lucia Galletti sul Lungotevere, vogliamo che i nostri prodotti siano anche portatori di bellezza e di confort, che il nostro lavoro quotidiano possa davvero incontrare le esigenze di tutti.
Grazie di avere dedicato un po’ di tempo a leggere questo articolo.
Giovanni Affinita
Chief Sales Strategist e membro del Consiglio di Amministrazione di SAPA
VUOI SAPERE DI PIÙ SU COME APPLICARE IL MONTANTE BI-COLORE PER OTTENERE PEZZI PIÙ LEGGERI IN MENO TEMPO?
SCRIVI A CUSTOMERCARE@SAPAGROUP.IT, UN SAPA GENIUS TI RISPONDERÀ ENTRO 24 ORE.