The 23rd conference On plastics was held on 15 november, with the title: “SMART CITY: materials and technologies for mobility and habitat”.
Innocenzo Macchiarolo, technical and r&d director at sapa participated in a round table and a debate, with numerous experts, on the latest trends and on the secrets of the cars and mobility of the future.
We have always imagined the car of the future in a certain way.
Something between a DeLorean of the film Back to the Future and a Ford Anglia 105 E in Harry Potter: it can fly and resist to numerous adversities, from enemies to heavy rains and missiles; but most of all it is super-fast.
So fast that it challenges time.
When we were little, we drew the car of the future with all the possible comforts, like automatic doors, two small wings so it could fly and an extra tank for food supplies.
Do you remember?
The Year 2000 was the future and it seemed to us to be far away, so far away that we could use our imagination effortlessly and freely, anything goes.
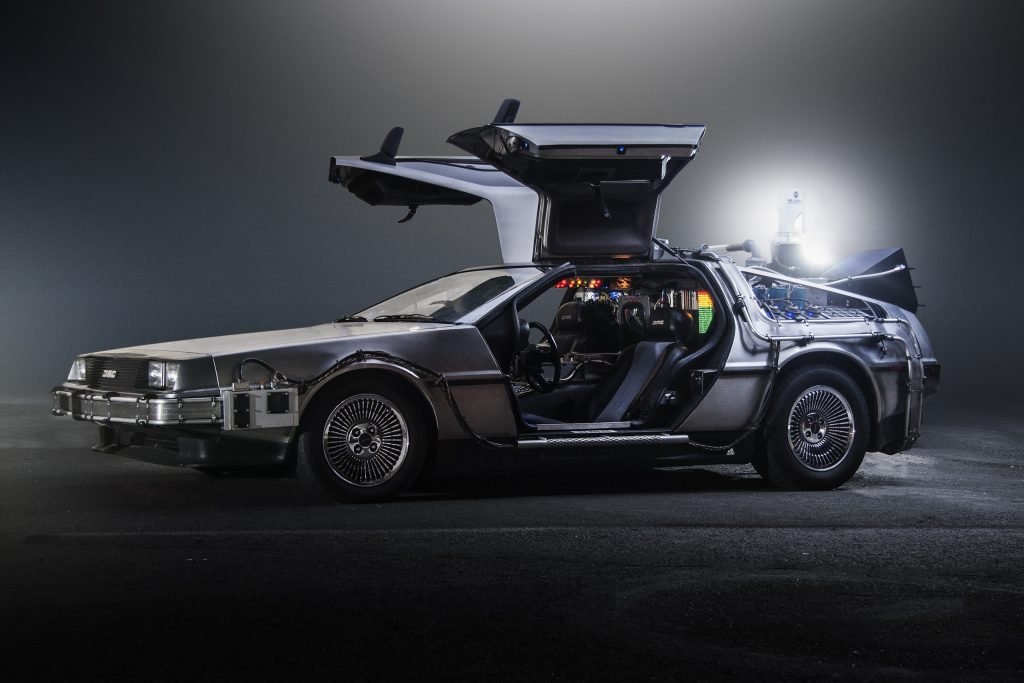
And then the future actually arrived a while back and maybe it is worth asking ourselves what has changed and what is changing.
This is exactly what we did in Parma on 15 November at the Conference on Plastics that this year was titled “Smart City: Materials and Technologies for mobility and habitat”.
SAPA was invited to participate in a round table on the topic “From smart cities to smart mobility: technologies and solutions that make cars fit for the future”.
Innocenzo Macchiarolo, Technical and R&D Director at SAPA, in his speech talked about SAPA’s practical commitment towards innovation and in particular, about the attention to the environmental impact of production that SAPA has been demonstrating for quite some time.
An example of this commitment was the development and patenting of the One-Shot® Method, currently the world’s fastest method to produce car parts.
The rationale of this innovative idea is namely to reduce the number of production phases to the minimum, to produce lighter parts and to keep high quality standards.
With the One-Shot® Method it is very often possible to obtain a part in just one step.
If you are wondering what this all means concretely, well, it’s very simple.
The direct implications of this solution are first and foremost better cost efficiency. This method rests namely on automated processes that aim at reducing the risk of human error.
Additionally, another important result is that waste is reduced and the car is made lighter. This is perhaps the focal point on which one should concentrate, not only in view of Horizon 2020 but also in view an improved respect for the environment, which nowadays has become mandatory. You know that the car manufacturing industry is making a lot of efforts to adapt to the new standards for the future and at SAPA we responded to these challenges by creating the One-Shot® Method. Here is our secret.
Let me give you an example to explain what I mean:
Our One-Shot® C Lower Pillar.
With traditional methods, this item is produced by hand by specialised workers, because, as you know, traditional methods foresee a foaming process inside the mould.
This necessarily results in a higher cost.
With the One-Shot® Method on the other hand, the results are very different indeed:
- 1,000 C Lower Pillars can be produced daily, instead of 40;
- 80 seconds cycle time, against the 12 minutes of the traditional process;
- 40% savings – that can be invested in other parts.
Practically:
- Better quality and a robust, standardised and GUARANTEED process: the machine process is 100% certified while a process based on a human operator yields lower quality and has a higher risk of differences among the pieces.
This means that you will no longer have to worry about imperfections and you can save on the cost of specialised workers.
- High production capability and high production volumes: Producing 1,000 C-Lower Pillars per day means fulfilling a demand for 500 sets per day, or 120,000 cars per year.
This means that you will improve the quantitative performance of your business.
- Process and technology applied for the first time to big pieces like the C-Lower Pillar
So, this is an innovative investment in technology for you and your car maker.
- Less costs: if you draw a business case and you analyse manual production vs automated production – even in the case of equal cost of manpower, automated production costs less.
That is to say: you can invest in other parts that you have issues with.
I must admit that this solution is making us very proud.
I am aware that it is not easy to change one’s habits for something totally new. But looking for solutions that fit in the new automotive landscape remains paramount.
After all, the car of the future is not something that is yet to come, but something that is already happening.
We are ready.
Kind regards,
Giovanni Affinita,
Executive Director and Member of the Board of Directors at SAPA