The One-Shot® Method is the world’s fastest method to produce car parts; it is a patented method and it was designed to reduce the number of phases and to optimise production processes. At the workshop organised by Meusburger in Pescara, Engineer Mr Innocenzo Macchiarolo told about the evolution of this innovative method.
Some time ago, SAPA attended an important event that took place in the city of Pescara.
It was a workshop organised by Meusburger, the leading supplier at international level of high-quality products for mould, tools and machines manufacturers, which encompasses several brands: Meusburger, PSG, WBI, Segoni.
It is a prestigious company and with its €291 million turnover and plants all over the world, it plays an important role at international level.
SAPA was invited to give a speech on its experience with the One-Shot® Method, which, as you know, is unique in the automotive sector.
Why am I talking about this?
Meusburger and SAPA operate in different sectors.
However, the uniqueness of the One-Shot® Method was recognised as an important example of:
- Process optimisation
- Lightweighting of the parts
- Production speed
- Attention to waste reduction
- Exponential increase in productivity (for some parts, it may go up to +500%).
I’ll explain myself better, please bear with me as I am sure that you will find something important for your work.
As I was saying, to date the One-Shot® Method is recognised as being the world’s fastest method to produce car parts with:
- Less weight
- Less waste
- High quality performance.
The first direct consequence of this is that the parts patented by SAPA with this method possess all these characteristics
I am talking about the five already industrialised products: One-Shot® Window Frame, One-Shot® C-Lower Pillar, One-Shot® Bicolor A Pillar, One-Shot® Engine Beauty Cover and the very new One-Shot® Aero Shield.
The characteristic that makes the One-Shot® Method even more special, though, is its transferability, that is to say that it can be applied to any part and it allows you to obtain the guaranteed results that are typical of the Method itself.
Here is a simple example.
Try and think of all the issues connected with eyesight: short-sightedness, long-sightedness, strabismus, astigmatism and anything else you can think of.
Each and every one of these issues require the use of a corrective system: eye glasses.
Clearly, the lenses are chosen on the basis of the individual needs, but the tool used is always the same.
For example, let’s take short-sightedness, which causes the image of faraway objects to be out of focus, while the same objects are neat and in focus if seen from nearby. In order to correct this, you need lenses that are adjusted in a way as to sharpen the vision of faraway objects.
Similarly, to correct long-sightedness, which is basically the opposite thing – in that you have difficulties seeing nearby objects neatly, you need glasses. In this case, however, the lenses will be adjusted to solve this particular issue.
In short, the One-Shot® Method works according to the same principle.
You can apply it to internal parts, external parts, parts around the engine area etc. Will the results be the same?
In terms of numbers, definitely not. But in terms of production speed, lightweighting of the parts and waste reduction, absolutely yes.
And this is the reason why a company very different to SAPA invited us to speak at a training workshop.
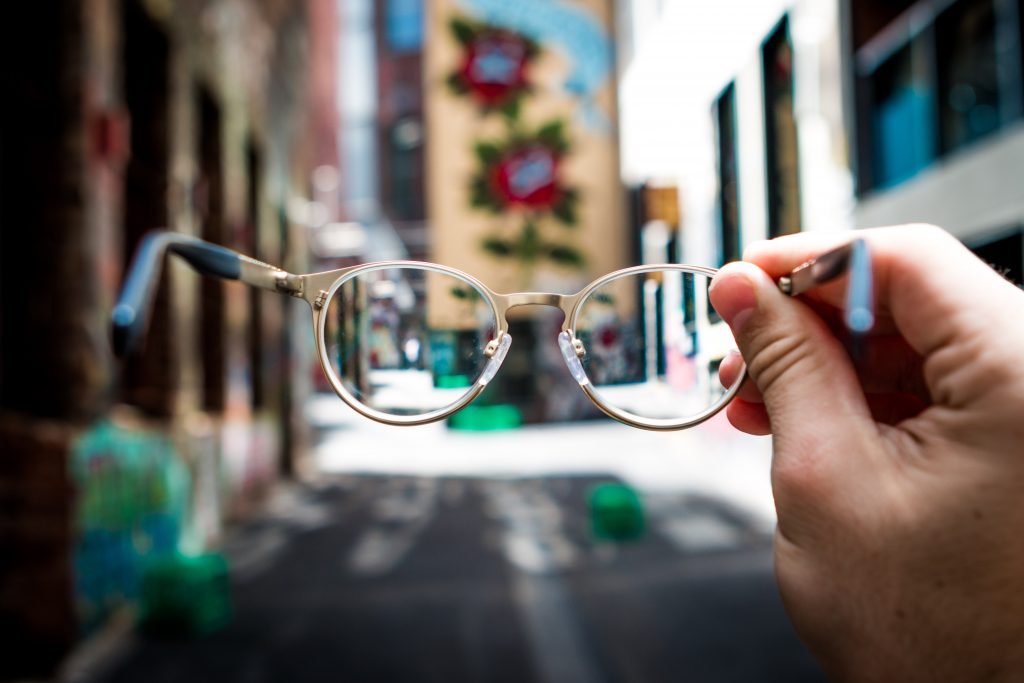
The experience of the latest years and the results that we have achieved (for example, being awarded by FCA as Best Supplier of the Year last December) led SAPA to invest in this method even more, and because of the characteristics I described above, this method can be said to have overcome the very idea of lean production.
How is this possible?
Imagine that you can obtain the same part but in much less time in comparison to the traditional method.
By reducing the production line, the first consequences will be:
- Less need for specialised workers, so the final cost of the part decreases;
- Less occupied space: if you optimise the process, you will need only one machine, so you will be able to replicate the process anywhere and you can invest on other useful machines;
- Exponential increase in production, so you can meet the client’s requirements;
- Shorter delivery time, hence, no more delays and hence a solution for most of your issues in this respect;
- No more downtime, which means that you will always meet delivery deadlines;
- Diminished use of back-up machines: if you have less machines to coordinate, the error risk will decrease, and you will have a leaner process that meets the customer’s expectations in a better way.
Can you see how many concrete advantages this method brings to your daily work?
I would like to give you a preview of some parts of the Workshop. You can request the full video by filling in the form at the bottom of this page.
Engineer Mr Innocenzo Macchiarolo, who spoke on behalf of SAPA at this important event, said something that we often say at SAPA:
People and the team make the difference. Building solid teams and making people feel part is the winning strategy.
We believe in people and we believe that sharing and is the first step towards growth.
Kind regards,
Giovanni Affinita
Executive Director and Member of the Board of Directors at SAPA