This question is keeping car makers around the world awake. But are you sure this is the right question?
As you know, the annual Geneva Motor Show took place a couple of weeks ago.
I followed very attentively the reports on the novelties and the previews, and I came across an article that made me think a lot and I would like to talk about it today.
I was at home and I was scrolling on my iPad after an intense day at work. Finding the time after dinner to set my mind free to look at the things that I’m interested in is a real booster.
I came across an article published by Quattroruote that told about two car models that will support FIAT in the challenge of reaching zero emissions in Europe, i.e. the new FIAT 500 and Centoventi. I guess you have heard about them.
While I was scrolling through those lines, something incredible happened to me, it’s hard to describe it. On my skin I had the same sensation of when you do paragliding.

You are safely buckled up, the first times you have a teacher with you, you know the direction of the wind, your target point and you know the technique. You may also have put your fears aside, you don’t think about the risks so that you can jump freely.
But still, you jump into the void.
Do you see what I mean?
We are asking ourselves a lot of questions on the future of cars and, I believe, rightly so.
Yet, even though our world rests on calculations and numbers, forecasts are about things that are yet to happen, and we cannot imagine what they will be like in detail.
Will the electric car be a success? What will its market diffusion be like? What target customer will be most interested in this innovative breakthrough in the sector? When will we be able to say that we have “switched to electric cars”?
A lot of questions, a lot of curiosity and a lot of doubts. But this is not all.
We also have a certitude: the car of the future will have to be more lightweight and less polluting.
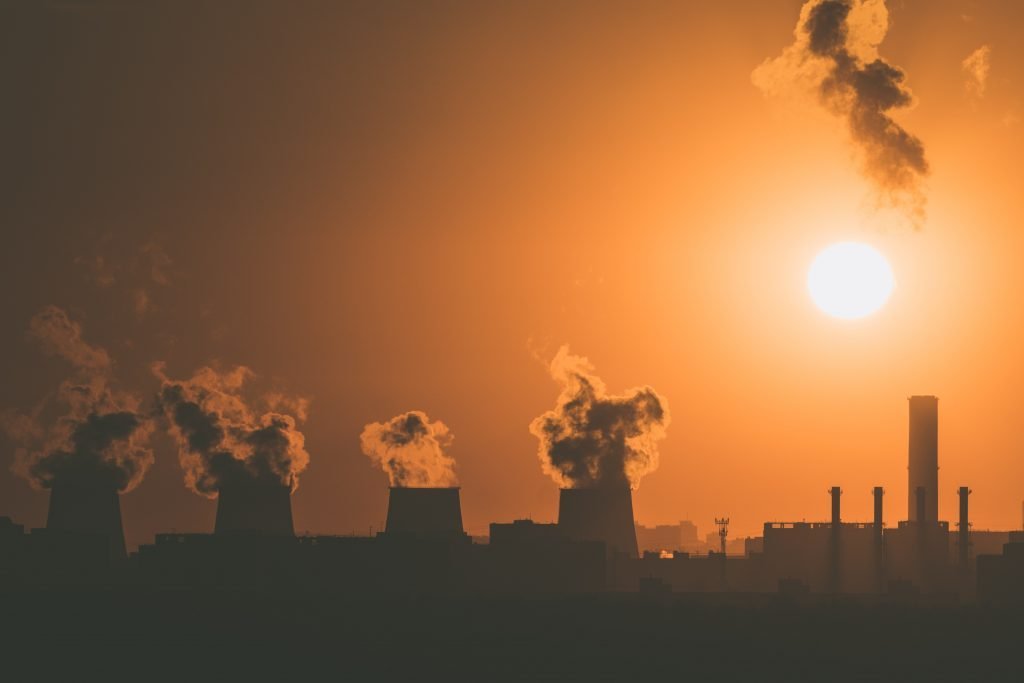
Natural resources and the sustainability requirements of our planets stress this out.
Is the full electric option a viable option?
Probably yes, but we also need to consider that:
- In 2018, Volkswagen registered record sales of diesel engine cars, hence competition also comes from consumers’ habits and preferences;
- Electric cars have limitations that haven’t yet been overcome such as high cost, autonomy, battery disposal, recharge stations, the need for unlimited energy production etc;
- If electric is the future, the future is not happening right now: it is an alternative that still needs time, it’s not immediate.
So, what is the answer to the question that I asked at the beginning in a willingly provocative way?
Maybe debating is not the answer. And maybe we are not asking the right question.
Because, if our objective is to reduce the car’s weight and have it to consume less, then maybe we need to ask ourselves what are the solutions that allow us to achieve this and then create the conditions to meet the Horizon 2020 objectives
Are you following me? Trust me, I’m sure you will find something very interesting for your work.
Switching to electric cars does not seem to be the solution to structural problems today.
Once the objective has been set, there are different ways to reach it.
I’d like to quote an example that pertains me personally: for months now, SAPA has been taking part in a project called LIFE BIOBCOMPO together with CRF, FCA and SOPHIA and with the support of the European Union; the project aims at reducing CO2 emissions by 8% by June 2021
How?
By lightweighting parts and by deploying composite materials, by substituting conventional mineral fibres with bio-based fibres that promote the use of more sustainable resources.
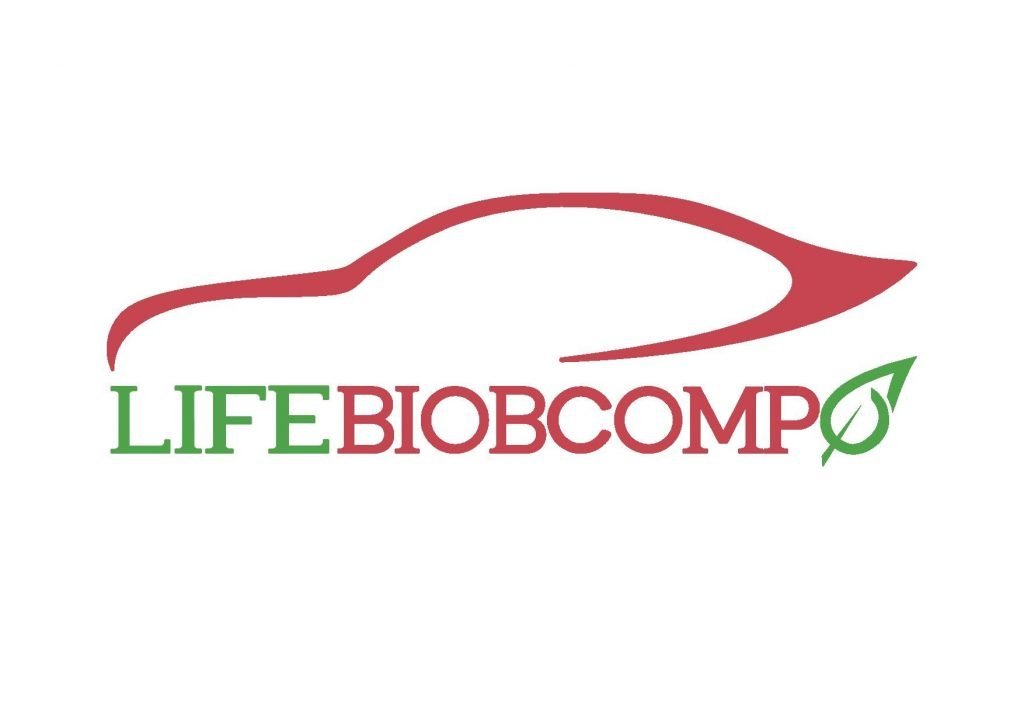
The idea of working on the part already in the designing phase by researching a production process that makes it smarter and that produces less waste is also the foundation of the One-Shot® Method that was patented by SAPA and is already industrialised.
As a matter of fact, it is the world’s fastest production process to create car parts with:
- Less weight
- Less waste
- In shorter time;
- High quality standards.
Let me give you a concrete example to explain what I am referring to.
The engineers of the “Innovation Engineering” department of SAPA have updated the Engine Beauty Cover production process.
As you know, in the traditional process the following things and phases are needed to obtain the result:
- 3 different moulds to mould the pieces
- Injection of foamed PUR carried out by external suppliers
- Assembly and joining of the pieces with star locks and washers.
We also need to bear in mind that the PUR injection phase is three times slower than the moulding phase.
By applying the One-Shot® Method, our engineers were able to eliminate the assembly phase of the pieces and reduce the moulding and the PUR injection to just one phase.
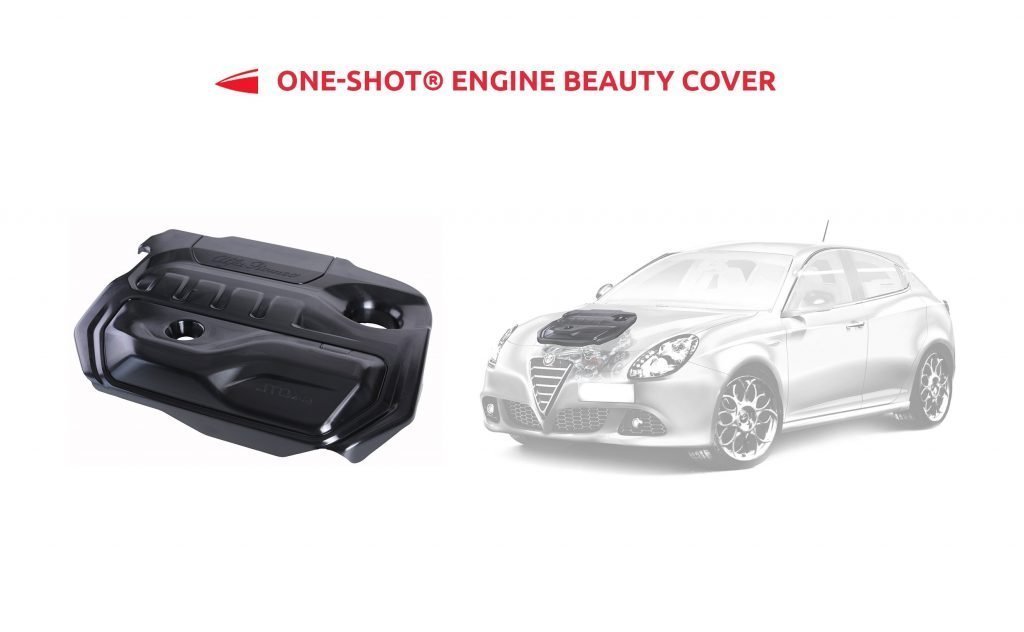
You may be wondering what the consequences of this choice are, here they are:
- 300% productivity increase;
- One single mould instead of 3: in the standard process, 1 mould is needed for the hard shell and 2 more are needed for the PUR;
- The cycle time is reduced from 180 seconds (needed to mould the cover + soundproof moulding) to 60 seconds;
- Joining with star locks is no longer needed because the part is joined chemically, so no operator and no dedicated machine are needed to join the part to the cover;
- Improved luxury sensation thanks to reduced rubbing and noisiness.
What am I trying to say? Well, it’s easy.
The patented One-Shot® method is an alternative to the traditional system and offers the possibility to reach the same objectives of waste reduction, part lightweighting and shortening of production times that the electric technology wants to reach.
As a matter of fact, when one hears the words waste and pollution, one immediately thinks of fuel but there is also another kind of pollution created by long production processes and non-optimised systems.
Keeping in mind the example that I quoted earlier, the Engine Beauty Cover created with the One-Shot® Method is produced with just one mould and in just one production island, hence the costs and waste that derived from transporting the part and injecting foamed PUR are eliminated.
And this is not yet all.
Because it is an innovative system that takes account of the ongoing changes in the automotive sector the One-Shot® Method conjugates really well with electric technologies.
I’d like to quote the One-Shot Aero Shield as an example – it is the latest part patented by SAPA.
Like many other parts produced with the One-Shot® Method, the underbody shield is produced in one single go, in one single production phase.
The innovative technology used allows us to use a carbon peroxide cloth, which is highly resistant – it can withstand 500 degrees to substitute aluminium, thus improving the technical performance of the part.
Because it is produced in just one shot, it does not need aluminium rivets, which risk absorbing or reflecting electrostatic discharge. So, it is perfect for electric cars.
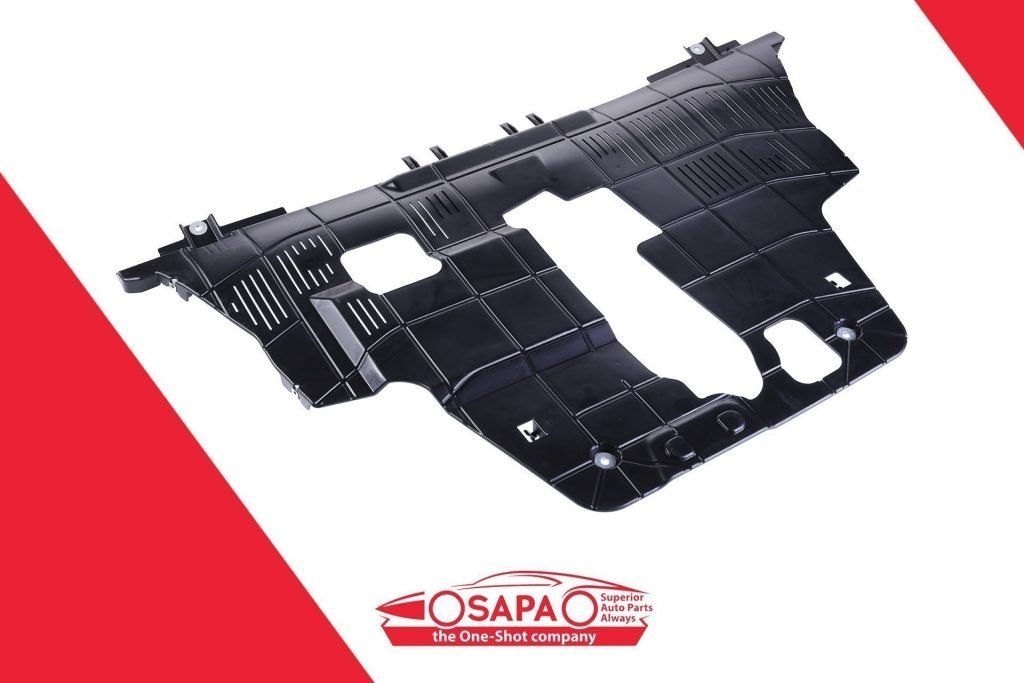
So, is the future of cars electric? We cannot tell.
Of course, sustainability requirements and the need to find solutions that transform cars are very real and urgent.
Like good paragliders we must choose the best tools, prepare for the journey and let ourselves be guided by the most favourable winds.
Only in this way can we succeed.
Kind regards,
Giovanni Affinita
Executive Director and Member of the Board of Directors at SAPA
If you’d like to find out more about the One-Shot® Method and all the patented parts, which are more lightweight, less polluting and which guarantee high quality performance, please fill in the form below.
WE’LL GET BACK TO YOU WITHIN 24 HOURS!