2020 has started. Yet some car makers are still stuck with the traditional production method (and its inevitable and well-known issues). Why? The answer is simple: they have at least one of the five behaviours you’re about to read about. But the solution for them and for you is already here.
I met many of them, and I will meet many more.
Today it is my job; in the past, it was the natural consequence of “being born here”.
Try and retrieve the oldest memories you have.
Done?
Good. Where were you? Maybe in a park or at kindergarten. At your cousin’s birthday party?
It is a nice exercise, isn’t it? Digging deep in your memory means meeting again faces, places and voices that were hidden God knows where.
Well, I was here. Here at the factory, I mean. I grew up on “bread and cars”. This is the air I breathe since ever. In my oldest memories, I am here with my mother and father.
I am the youngest of three children and I was really small when the SAPA machine was already going full speed. My parents worked a hell of a lot and I spent my days here with them.
You can imagine that the factory seemed like a magic circus to me.
I was lucky enough to be able to observe my parents for a long time and from near: I looked and still look at what my older siblings do, I still try and learn as much as possible from the men and women that work for us and that are the engine of our company.
For this reason, I said that I met many of them, I was talking about engineers.
At SAPA we work in this sector since generations, side by side with them, because it is them that we want to offer answers to.
WHAT DOES IT MEAN TO BE PROCESS SPECIALISTS IN THE AUTOMOTIVE SECTOR?
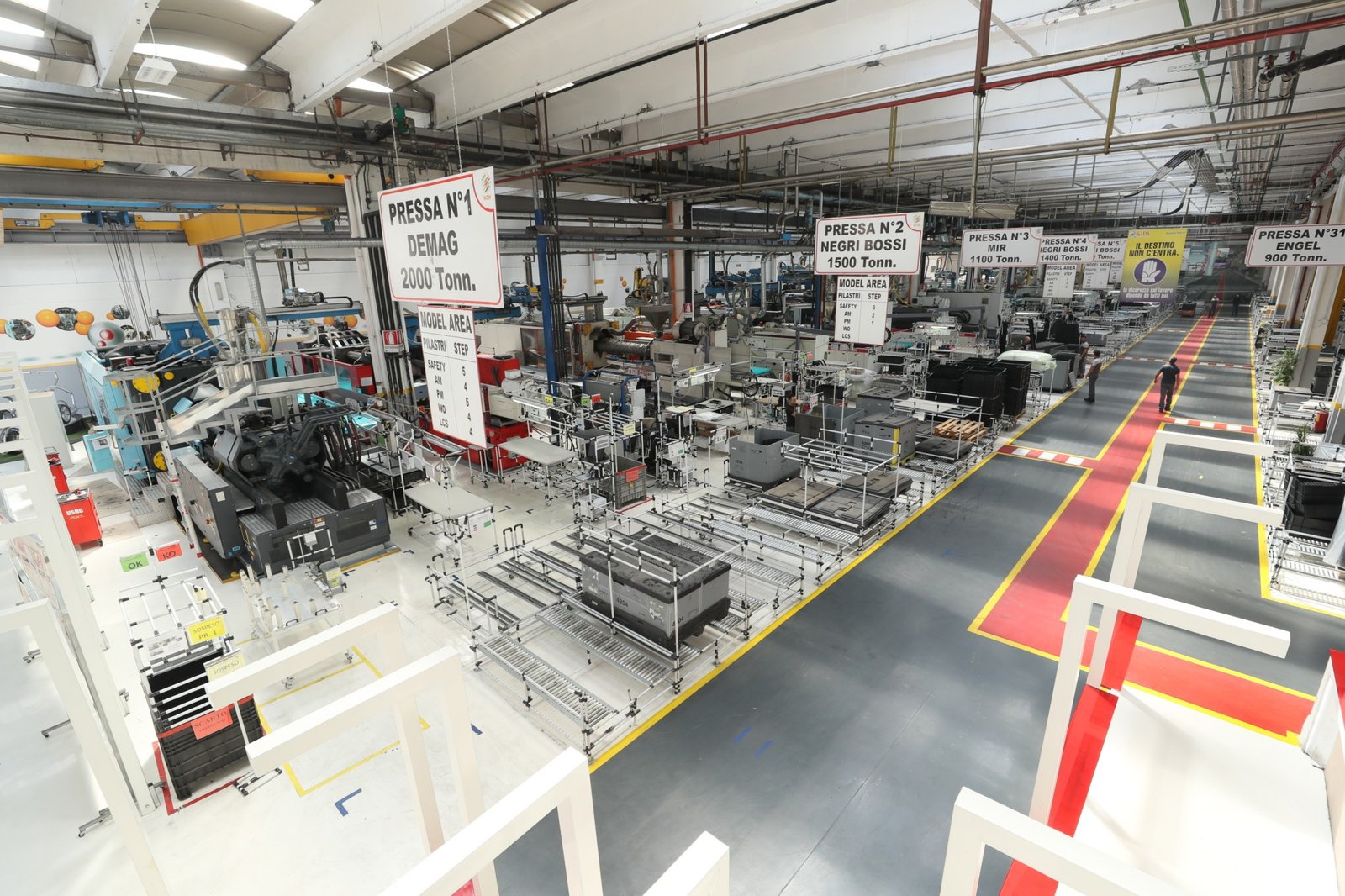
Our job substantially consists of solving their problems. Your problems.
To do so, one thing is indispensable: knowing them well.
I mean the engineers and the problems they face.
In this way we became Process Specialists.
Making this industrial choice means focussing your skills and experience and centring them around the product. It means improving your product knowledge, it means giving it your all and become the point of reference that stands out in a given market niche.
And in this way, by correcting course and taking care of our resources, we became what we are today: Process Specialists that developed an open and honest dialogue with customers and that are able to offer what the market needs.
Do you know what? I have noticed that there are five recurrent behaviours among the car makers that keep complaining – and rightly so, about downtime, delays, deformations and insufficient budgets.
That’s right: there are five common mistakes that the engineers that cannot free themselves of the nuisance that the traditional method imposes upon them make.
I will reveal them to you immediately, but let’s make a deal first: promise that you will be honest in giving your answer.
OK, I trust you.
THE CHECKLIST OF THE CAR MAKER THAT IS CHAINED DOWN TO THE TRADITIONAL METHOD
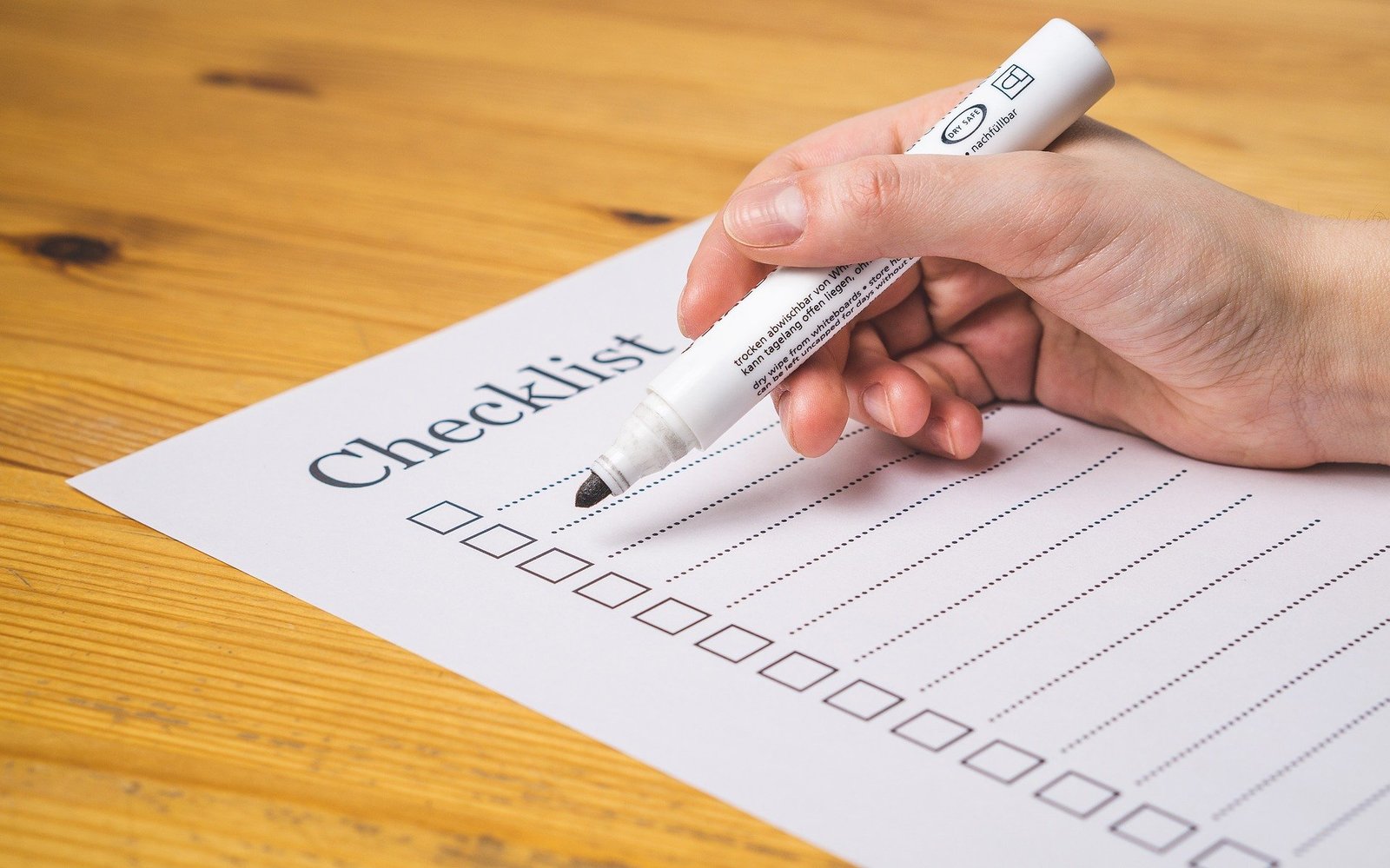
So, tell me, do you see yourself in any of these behaviours?
- You believe in the traditional production method as if it was your only God.
- You have allowed others to convince you that a faster and better performing way to produce car parts does not exist.
- You accept delays and production downtime even though they keep causing immense issues for you.
- You consider electric cars as the only hope to reduce emissions.
- You are resigned to being slowed down by the same issues that you are faced with every single day.
If you have answered yes to at least one of these scenarios, I have a question for you.
Have you realised that it is for this very reason that your work is not as smooth as you’d like it to be (and as easy as it could be)?
You see, you and I have common problems and common enemies.
Which ones? Car weight, production costs, emissions values that need cutting. You’ve understood, I don’t need to add anything.
I gave myself a headache trying to find solutions that can be useful.
We have spent years researching, carried out many tests, failed countless times, encountered many issues and thrown away many prototypes because they did not meet the standards we were aiming for.
Finally, after many failures, efforts and sweat we managed to come up with the best solution: the Method that guarantees (literally: ask us about the One-Shot® Guarantee) that you’ll reach the budget, cycle time, lightweighting and recyclability objectives that were given to you.
A NEW AND BETTER PRODUCTION METHOD EXISTS
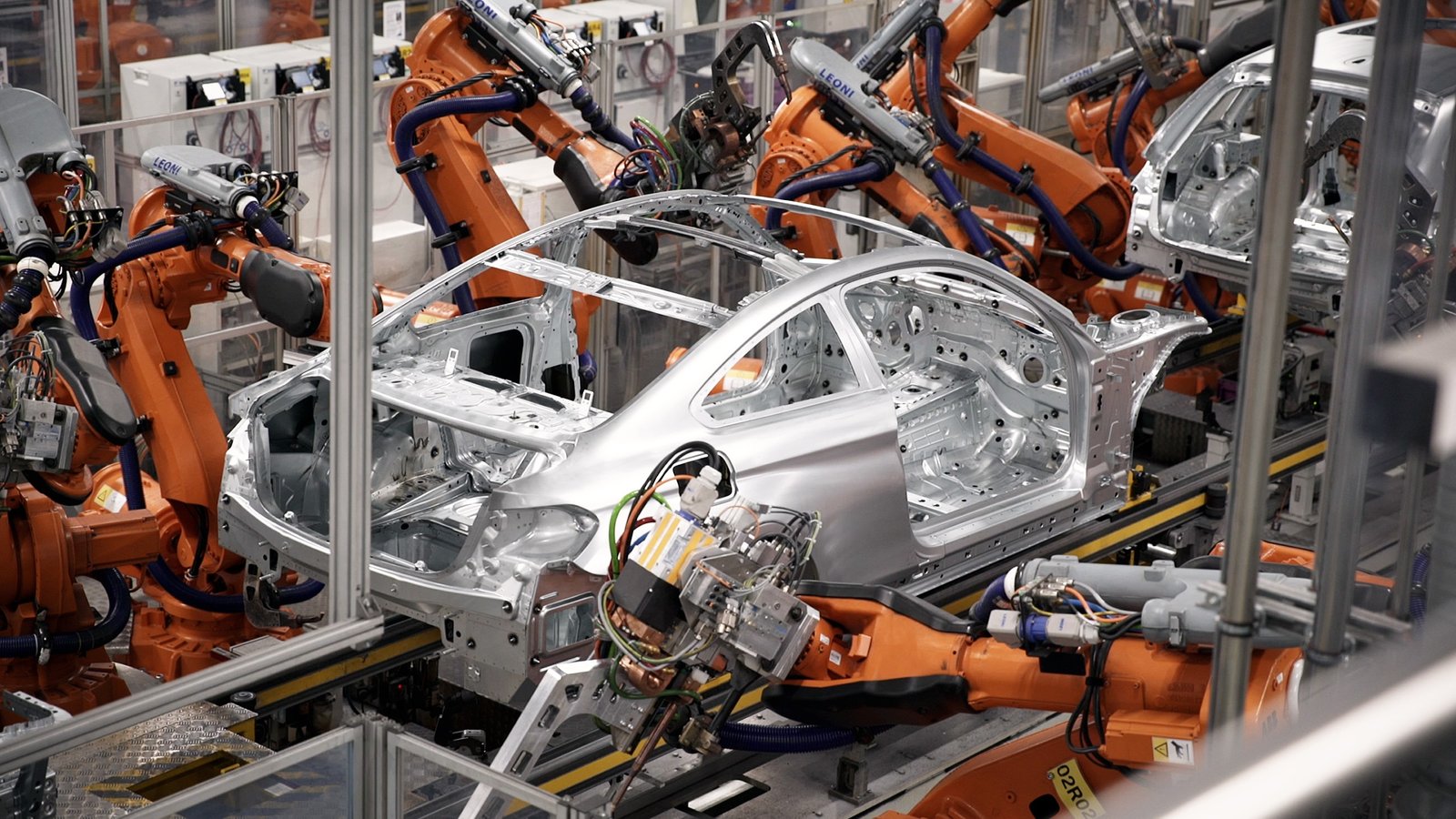
The One-Shot® Method is the world’s fasted patented method to produce car parts. It rests on a very simple idea: we compressed all the steps of the traditional car part production method into one all-in-one method.
What does this mean?
It means that we can do in just one step what you used to be doing in 3-4 steps, and this has very positive consequences, as you can imagine.
- Shorter time
- Less weight
- Less waste
- Guaranteed sector standards
And this in turn means:
- Cycle time up to 900% faster and 300% productivity increase
- Lower costs and better commercial performance on your budget
- Lower emissions, more lightweight and recyclable parts in line with Horizon 2020
Imagine the consequences of using your budget better and increasing production:
It is possible if you know how to do so.
The ball is in your court.
You can let there be delays, costly downtime and excessive emissions that slow down your work (and that prevent you from being promoted).
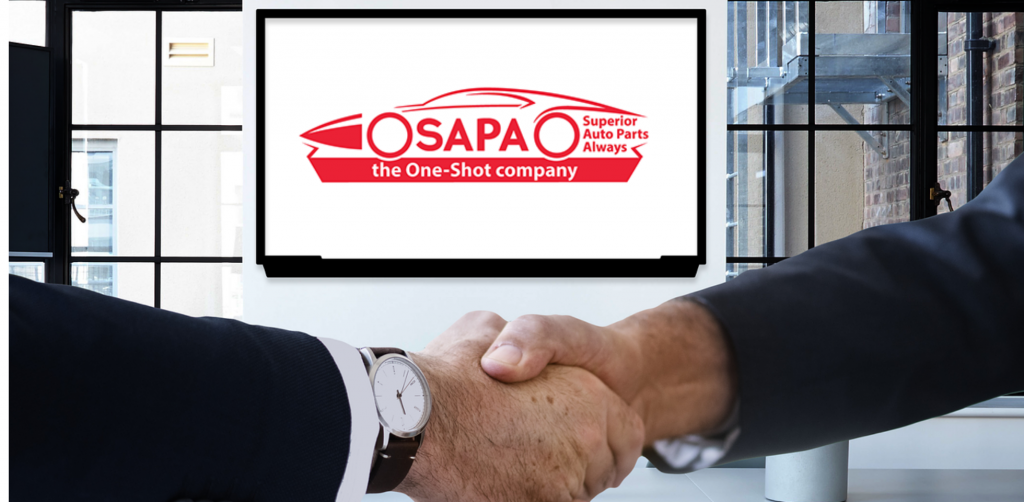
In sum, you can carry on pretending that an alternative to the traditional method does not exist.
The difference is that now you know it exists. And some are already enjoying the advantages it guarantees.
The engineers of Volkswagen, Jeep, FCA, Ferrari and many other important car makers that we work with already know how to obtain infinite productivity, commercial performances on their budgets, production time cut in half and recyclable, more lightweight components that help reduce emissions.
As a matter of fact, the parts produced with the world’s fastest method are already in use on over 350,000 cars in the world.
Allow me to tell you: The One-Shot® Method is the ace that you can put on the table at the next company meeting.
Discover more by filling in the form at the bottom of the page.
Kind regards,
Giovanni Affinita
General Manager and Member SAPA’s Board of Directors
Obtain cost reduction and infinite productivity now: Let’s evaluate together the application of the One-Shot® Method to the project you are working on.
Fill in the form below. We’ll get back to you within 24 hours