Der nach der One-Shot®-Methode hergestellte A Pillar- Bicolor entsteht in nur 70 Sekunden und kombiniert Aufbau und Montage in einem einzigen Prozess mittels eines Bi-Spritzgusssystems. Auf diese Weise wird die Abfallquote reduziert und es entstehen leichtere Komponenten. Genau das ist unser Lösungsansatz.
Ich muss es an dieser Stelle gestehen.
In den Ferien habe ich mir eine Auszeit genommen. Ich habe einfach mal nicht nachgedacht, denn im Alltagsablauf innerhalb des Jahres – das weißt du besser als ich – ist das nahezu unmöglich.
Da gibt es Termine, Treffen mit Kunden, neue Komponenten, die getestet und industriell umgesetzt werden müssen, unvorhergesehene Ereignisse, durch die die Arbeit oft behindert wird, kurz gesagt, ein heilloses Chaos.
Ich habe in diesen Tagen versucht, meinen Kopf frei zu bekommen, aber ich habe mich trotzdem weiter auf dem Laufenden gehalten.
Erst vergangene Woche fiel mir ein Artikel in der Fachzeitschrift Quattro Ruote in die Hände, in dem es um den Jeep Wrangler ging, ein Automodell, das mir bestens bekannt ist.
Ich war ziemlich erstaunt, weil SAPA vor einiger Zeit beim Jeep die technische Umsetzung einer Komponente übernommen hat, über die ich gleich berichten möchte. Ich bin mir sicher, dass es dich auf jeden Fall interessieren wird.
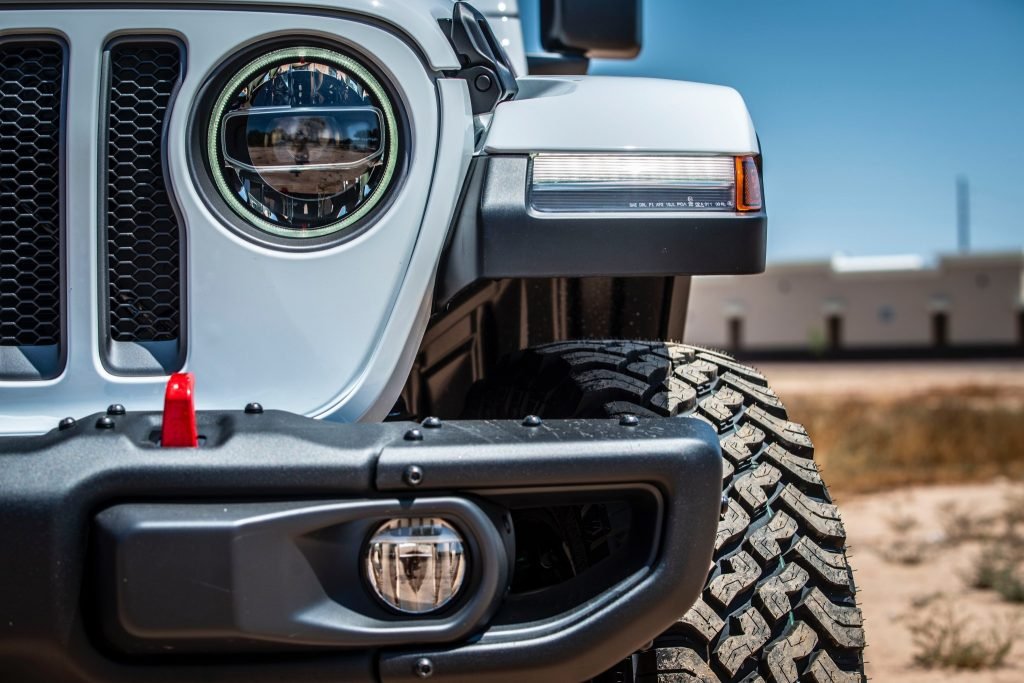
In dem Artikel ging es darum, dass die FCA-Gruppe eine Lösung zur Reduzierung der Stoßvibrationen gefunden hätte, die bei einigen Modellen des Jeep Wrangler aufgetaucht sind.
Der Hersteller hat einen neuen Stoßdämpfer entwickelt, der im Falle von Übertragungsunterbrechungen bei hohen Fahrgeschwindigkeiten die am Lenkrad wahrgenommenen Vibrationen durch eine Stabilisierung der Lenkung minimieren soll.
Wie ich bereits vor einiger Zeit berichtet habe, hat sich Jeep mit einer speziellen Anfrage an uns gewandt, die mit dem, was bei dem Wrangler-Modell eingetroffen ist, in engem Zusammenhang steht.
Angeregt wurden wir jedoch vom Renegade-Modell: ein majestätisches Auto mit einer extrem breiten hochgezogenen Mittelsäule, die jedoch ein bedrückendes Erscheinungsbild innerhalb des Fahrgastraums entstehen ließ.
Und du weißt selbst genau, wie wichtig die Gestaltung eines komfortablen und ästhetisch ansprechenden Fahrzeuginnenraumes für den mobilen Gebrauch ist.
Unsere technische Abteilung hat sich sofort an die Arbeit gemacht, um nach der am besten dafür geeigneten Lösung zu suchen, die sowohl die Eleganz des Fahrzeugs als auch seine Fahrleistung unter einen Hut bringen konnte.
Ursprünglich war geplant, die vordere Säule mit einem Kunststoffaufsatz zu fixieren.
Aus sicherheitstechnischer Sicht war diese Lösung jedoch ungeeignet, insbesondere im Falle des Auslösens des Airbags.
Mit anderen Worten, wir standen vor einer Reihe von Problemen, die wir in Angriff nehmen mussten und die herkömmliche Methodik schien uns dabei nicht weiterzuhelfen zu können.
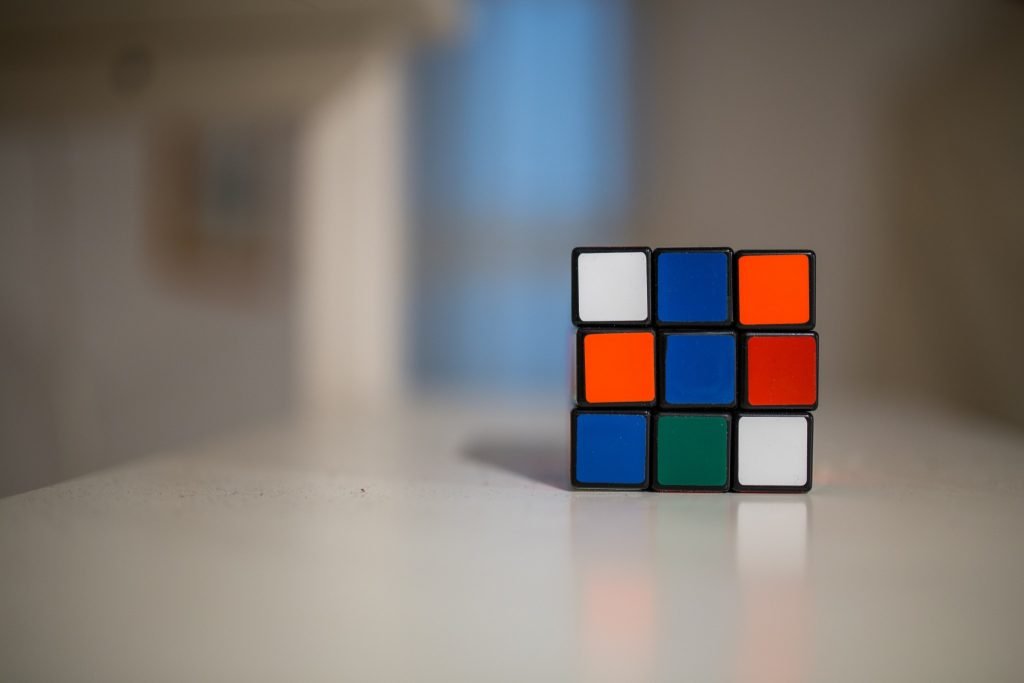
Warum die traditionelle Methode nicht dazu geeignet ist, die Probleme in Bezug auf eine leichtere Bauweise der Komponenten zu lösen
Wie du weißt, werden die Teile bei der traditionellen Methode durch den Einsatz von zwei Pressen übereinander gesetzt, schwarz auf grau, und zwar unter Zuhilfenahme von Haltestiften, die dann per Ultraschall oder mit einer Heißschneideklinge oder aber im Vibrationsverfahren verschweißt werden.
Danach werden unter Einsatz von zwei Maschinen, eine mit einer Kapazität von 100 Tonnen und die andere mit einer Kapazität von 300 Tonnen, zwei Spritzgussformen hergestellt, wobei die Pressen von zwei Maschinenführern bedient werden.
Im Grunde genommen handelt es sich dabei um eine mechanische Verkopplung, bei der die beiden getrennt voneinander hergestellten Komponenten übereinander platziert werden.
Das monolithische Teil ist demzufolge relativ wuchtig.
Dies führt zwangsläufig zu Montageschwankungen und kleinen Unregelmäßigkeiten, die, wenn sie gebündelt auftreten, mit bloßem Auge sichtbar wären.
Bei anderen Bauelementen können diese nahezu unmerklichen Abweichungen zu noch wesentlich störenderen Folgen wie Vibrationsbewegungen und Geräuschbildung führen.
Ich werde im Folgenden versuchen, die Probleme aufzuführen, die wir mit der traditionellen Methode nicht lösen konnten:
- Sicherheitsaspekt: Es war von entscheidender Bedeutung, den notwendigen Platz für ein eventuelles Auslösen des Airbags zu schaffen;
- Gewichtsproblem: Es war notwendig, die Endkomponente mit einem leichteren Gewicht auszuführen;
- Komfortproblem: Die große Frontsäule ließ den Fahrgastraum erdrückend wirken und erforderte zu ihrer Ausführung zwei Maschinenbediener;
- Ästhetisches Problem: Oftmals waren kleinste Unebenheiten schon mit bloßem Auge sichtbar.
In dieser Phase entstand schließlich folgende Konzeptidee: eine per Bi-Injektion hergestellte Säule, die die Realisierung von zweifarbigen Teilen ermöglichte, die nicht zusammengebaut, sondern als eine einzige Komponente ausgeführt werden konnten.
Für dich mag das vielleicht ein wenig verrückt klingen, aber lass es mich dir erklären.
Die Revolution der One-Shot®-Methode mit nur einem einzigen Pressenhub
Wie ich bereits erwähnt habe, hat unsere Abteilung “Innovation Engineering” mit der One-Shot®-Methode eine bisher kaum vorstellbare Technologie entwickelt.
Tatsächlich erfordert der neue Bicolor A Pillar im Inneren der Druckmaschine eine Drehvorrichtung mit einem zweiten Satellitenspritzzylinder, der die zweite Farbe einspritzt.
Was gestern noch mit zwei verschiedenen Gussformen und in zwei Pressmaschinen gedruckt und dann später montiert werden musste, geschieht nun – wie wir so schön sagen – in einem einzigen Rutsch.
Die so entstandene Komponente ist tatsächlich ein monolithisches und leichteres Bauteil: Es ist nicht mehr nötig, die Halterungen zum Überlagern der entsprechenden Bauelemente anzubringen.
Und eine derart aufwändige monolithische Bi-Injektion garantiert in jedmn Fall eine höhere Präzision, nicht zuletzt deshalb, weil hier, im Gegensatz zur klassischen Fertigung, keine weiteren Maschinenbediener eingesetzt werden müssen, durch die immer ein gewisses Abweichungsrisiko gegeben ist.
So entsteht der One-Shot® A Pillar Bicolor, bei dem bereits in der Entwurfsphase diejenigen Störfaktoren und Anpassungserfordernisse erkannt und beseitigt werden konnten, die zu einem späteren Zeitpunkt zu sehr lästigen Problemen geführt hätten, die dann zu lösen wären und die eine Menge Zeit in Anspruch nehmen.
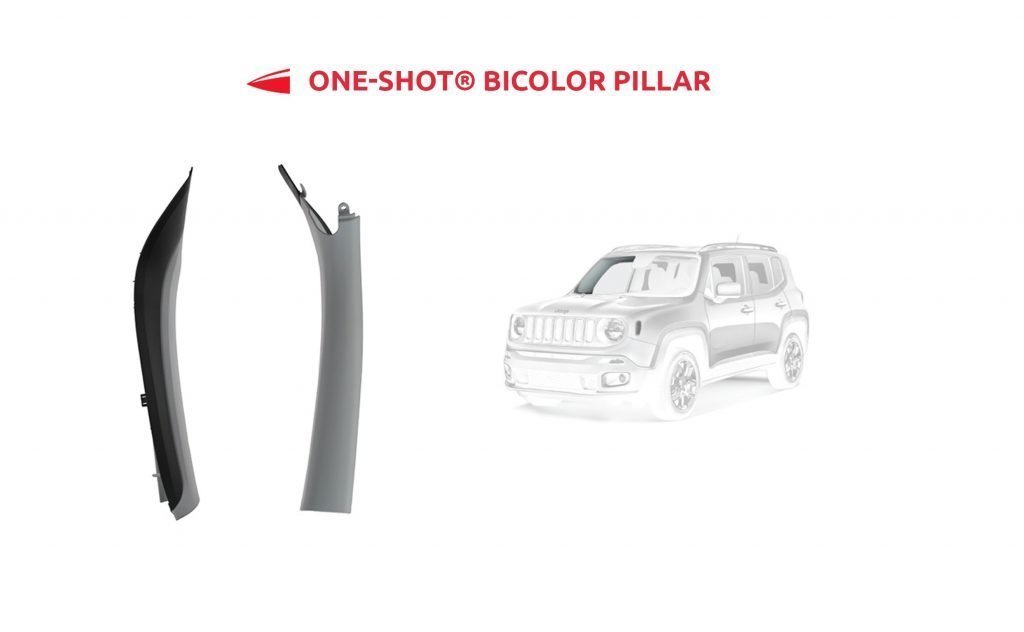
Bei der konventionellen Methode mussten die Teile übereinander gesetzt werden, schwarz auf grau, und dann die einzelnen Haltestifte per Ultraschall, mit einem Heißschneider oder im Vibrationsverfahren verschweißt werden.
Heute werden diese Halterungen, die der mechanischen Befestigung dienen, direkt in der Form selbst mithergestellt.
Das genau ist die ONE-SHOT®-Methode: ein Verfahren zur Vereinfachung, Optimierung und Beschleunigung der Produktion von Automobilkomponenten.
Mit den folgenden, angenehmen Auswirkungen:
- Deine Komponenten haben ein geringeres Gewicht, was zur Verbesserung der Fahrzeugdynamik und dessen Stabilität beiträgt;
- Der Bi-Injektionsmonolith muss nicht mehr montiert werden: Dadurch wird das Risiko von Verformungen bereits während des Zusammenfügens reduziert;
- Die Abfallmenge wird reduziert und damit gleichzeitig die Umweltbelastung gesenkt;
- In nur 70 Sekunden ist das Bauteil fertig, womit du viel Zeit bei der Produktion einsparen kannst. Das ist 2,1 mal schneller.
Diese Technik wurde anschließend beim Modell- Renegade angewendet, bis heute das einzige Auto mit diesem Säulentyp.
Somit ist also das angestrebte Ziel erreicht worden: die Verbesserung des Fahrgastraums und die Lösung des Airbag-Problems, das, wenn man so will, ein absolut entscheidendes Kriterium für die Sicherheit eines Fahrzeugs ist.
Dieses ist das einzige System, das es dir gestattet:
- Zwei Prozesse in nur einem zu vereinen, die Produktionszeiten zu reduzieren und die Lieferzeiten zu verkürzen. Somit hast du weniger Sorgen und mehr Zeit, dich mit anderen Komponenten zu beschäftigen;
- Den Montageschritt zu eliminieren, wodurch du Kosten einsparen kannst und du somit weniger auf die Mittel zur Finanzierung einzelner Entwicklungsbereiche bedacht bist;
- eine maßgeschneiderte Komponente zu erzeugen und dabei besonderen Wert auf die Ästhetik des Produkts zu legen, was, wie wir wissen, ein unerlässliches Qualitätskriterium in der Automobilbranche ist;
- einen vollautomatisierten Produktionsprozess abzuwickeln und sich keine Sorgen mehr um die Fehlerquote machen zu müssen, wissend dass der ” menschliche Faktor ” besonders schwer zu kalkulieren ist.
Bestimmt wirst du dich fragen, worin wohl die Schwachstellen dieses innovativen Prozesses bestehen.
Was das Endresultat betrifft, so gibt es keine.
Einziges offensichtliches Hürde-Kriterium ist die Notwendigkeit einer hochmodernen Pressanlage, eines perfekt effizienten Rotationstisches, was eine erhebliche wirtschaftliche Investition für das Unternehmen darstellen würde, denn die diesbezüglichen Kosten sind um einiges höher als bei einem Standard-Tooling.
Um in der Lage zu sein, ein Produkt mit dieser Bauweise zu reproduzieren, sind daher Investitionen erforderlich.
Wir bei SAPA haben diesen Aufwand nicht nur im Hinblick auf künftige Optimierungsmaßnahmen, sondern vor allem als Instrument unserer Forschungsarbeit, die für uns fundamental ist, unseres Engagements sowie der One-Shot®-Methode, auf uns genommen.
Was bedeutet das nun alles für dich?
- die Entwicklung und die technische Ausrüstung, damit dir mehr Zeit für die Arbeit am Auto bleibt.
- das Auto bekommt weniger Gewicht, entspricht also bereits den Anforderungen von Horizon 2020: Dadurch wird vermieden, dass nachträgliche Anpassungen neu kalkuliert werden müssen.
- eine Straffung des Prozessablaufes und die Möglichkeit, mit einem Partner zusammenzuarbeiten, der sich auf diese Methode spezialisiert hat und die gleichen Ziele wie Du verfolgt.
Du solltest dir in diesem Zusammenhang immer vor Augen halten, dass der gleiche Prozess auf andere Komponenten übertragbar ist.
Ein Beispiel?
Die Heckablage des Panda, die SAPA seit einigen Jahren herstellt: Das Bi-injektionsverfahren könnte an dieser Stelle Schweißarbeiten und Arbeitskräfte einsparen.
Mit anderen Worten: eine zusätzliche Möglichkeit, die Produktion insgesamt schneller und flüssiger abzuwickeln.
Das heißt und du wirst es festgestellt haben, dass die Vorteile wirklich sehr vielfältig sind. Durch den Raum, den SAPA der Forschungsarbeit zur Verfügung stellt, können im Vorfeld Probleme erkannt und reduziert (um nicht zu sagen eliminiert) werden.
Dies alles gibt uns eine enorme Bestätigung in unserer Arbeit und ich bin mir sicher, dass die One-Shot®-Methode deine persönliche Sichtweise auf den Automobilbau wirklich grundlegend verändern könnte.
Bis bald,
Giovanni Affinita
Geschäftsführender Direktor und Mitglied des Verwaltungsrats der SAPA
WENN DU MEHR ÜBER UNSEREN NACH DER ONE-SHOT-METHODE HERGESTELLTEN BICOLOR PILLAR UND DIE ANWENDUNGSMÖGLICHKEITEN BEI DEN ANDEREN KOMPONENTEN ERFAHREN MÖCHTEST, FÜLLE DAS UNTENSTEHENDE FORMULAR AUS. WIR WIERDEN DICH INNERHALB VON 24 STUNDEN KONTAKTIEREN.