ONE-SHOT METHOD ®
One-Shot® C Lower Pillar
Specialists
100% automotive direct supply to Car Makers
Exclusive
Creators of the
One-Shot® Method
Lighter
Less weight and less component costs
Co-Design
We design
with you
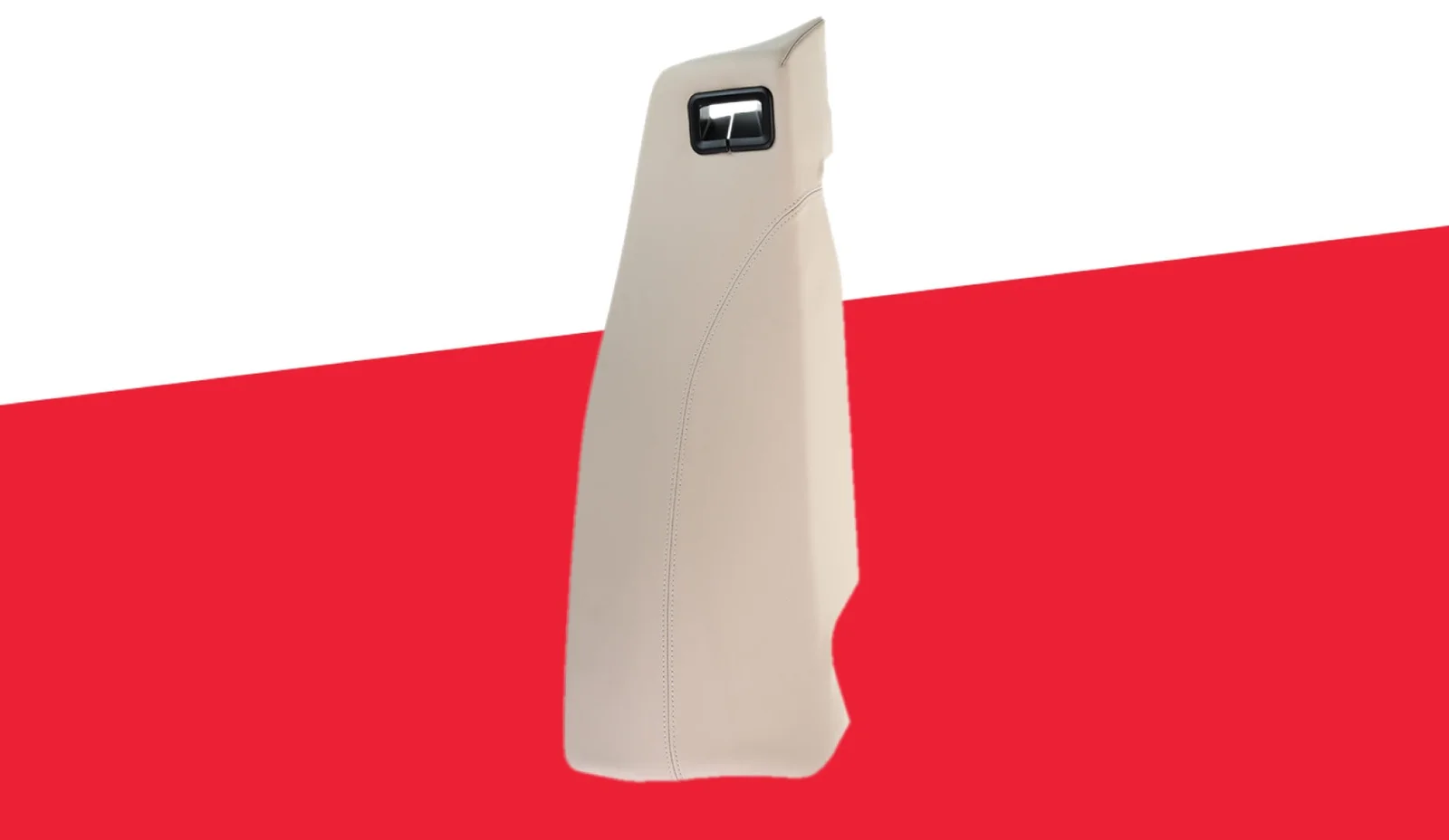
One-Shot® C Lower Pillar
Here is the method that allows you to produce up to 1000 C lower pillars per day, with 80 seconds of cycle time (against 40 C lower pillars per day, with 12 minutes of cycle time in the traditional process!)
We guarantee you:
80 second cycle time (allowing you to order more parts and receive them in less time without compromising quality)
A production of 1000 components per day
A significant reduction in costs, thanks to the automation of the process
Why is this methodology so revolutionary?
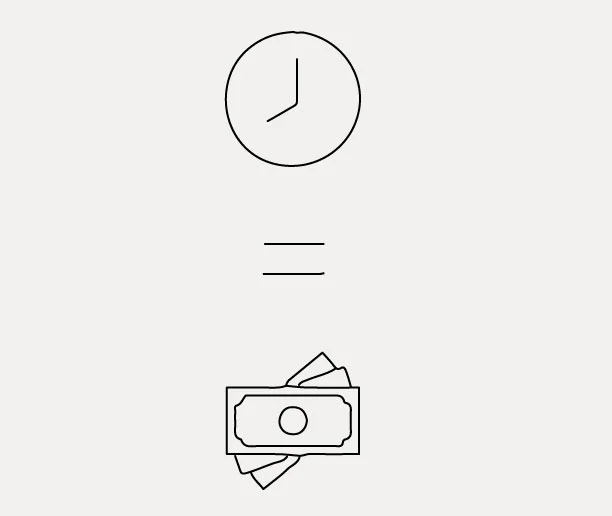
WITH THE TRADITIONAL METHODOLOGY
the production time of a single unit of C Lower Pillar is 40 minutes with the use of skilled workers, because the foaming process is required inside the mold. One day = 40 C Lower Pillar made per operator
PROBLEM
long lead times.

WITH THE TRADITIONAL METHODOLOGY
the seat pad is handmade. This means more possibility of human error, therefore more waste pieces produced and more training costs for personnel.
PROBLEM
the seat pad is handmade. This means more possibility of human error, therefore more waste pieces produced and more training costs for personnel.

WITH THE TRADITIONAL METHODOLOGY
the price of a single piece assembled with this methodology is 40% higher than that produced with the One-Shot® methodology because manual construction requires more workers, therefore more supervision for control quality and more training.
PROBLEM
need to have more quality control personnel, therefore more costs on final orders.
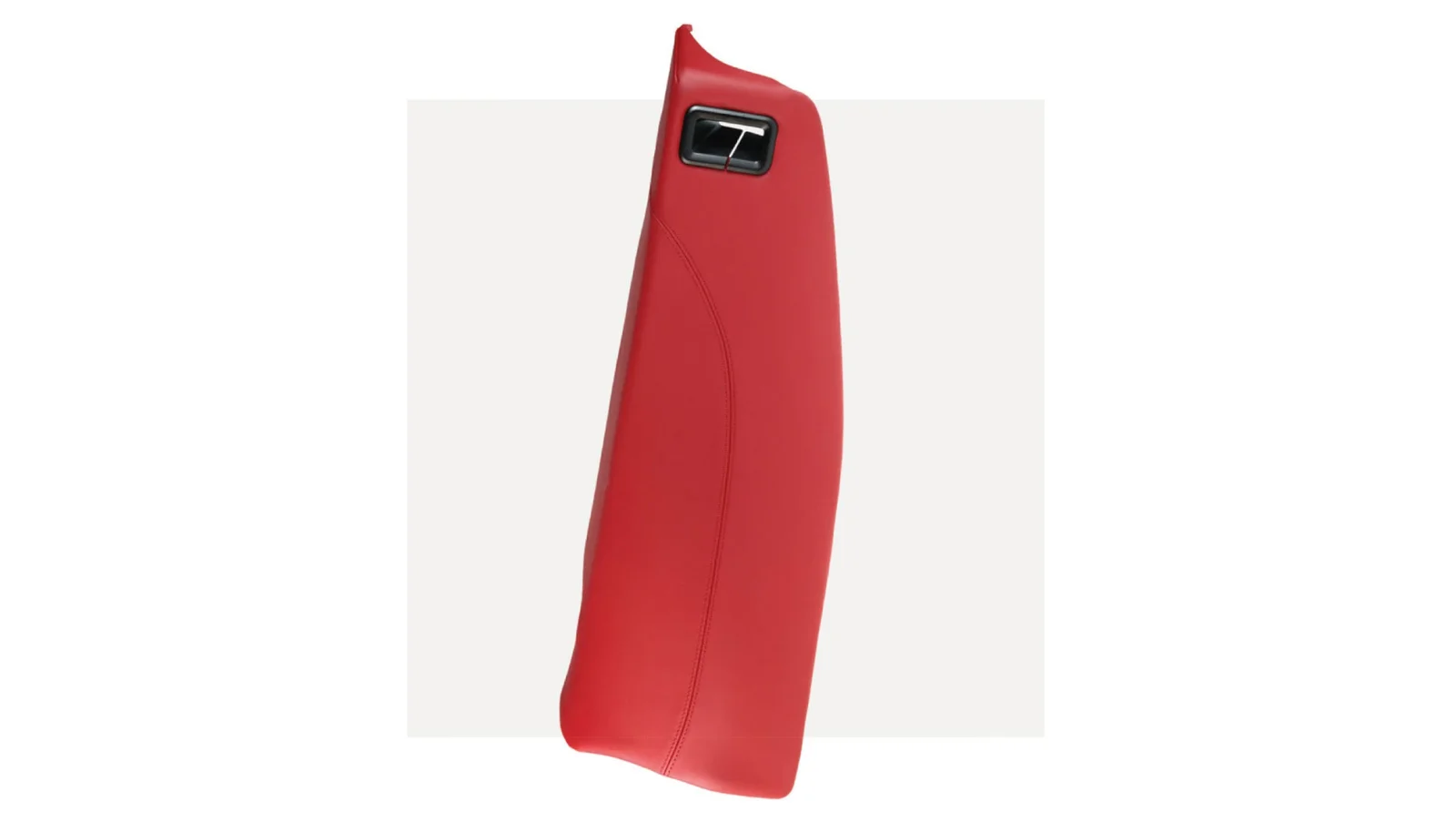
Thus was born the revolutionary One-Shot® process!
One day, however, a group of engineers within sapa began to gather to find a solution to these problems, in a top-secret department called "Innovation Engineering"
3 moulds, dependence on external suppliers, 2 processes (moulding + injection). become:
1 job only
1 component only
1 single press stroke In a single production cell
And the "pleasant consequences" are many:
80 seconds of cycle time
saving time so you can focus on other components
1000 components produced per day
guaranteeing the supply of high volumes of products
110% increase in productivity
Summing up
WITH THE TRADITIONAL METHODOLOGY
Average production time for one component: 12 minutes
Need for specialized workers = +costs
Non-automated process
Use of specialized equipment = +costs
5pcs x 20h = 100pcs/day 40 C-Lower Pillar/day
12 minute time/cycle
ONE-SHOT® METHOD
Average production time for a component: 80 seconds
No need for skilled workers = -costs
Fully automated process
Use of generalist equipment = -costs
1000 C-Lower Pillar/day
80 second time/cycle
Average cost per component: €0.44
But it doesn't end there
Our one-shot® c-lower pillar has already been patented and you will soon find it on Alfa Romeo Stelvio.
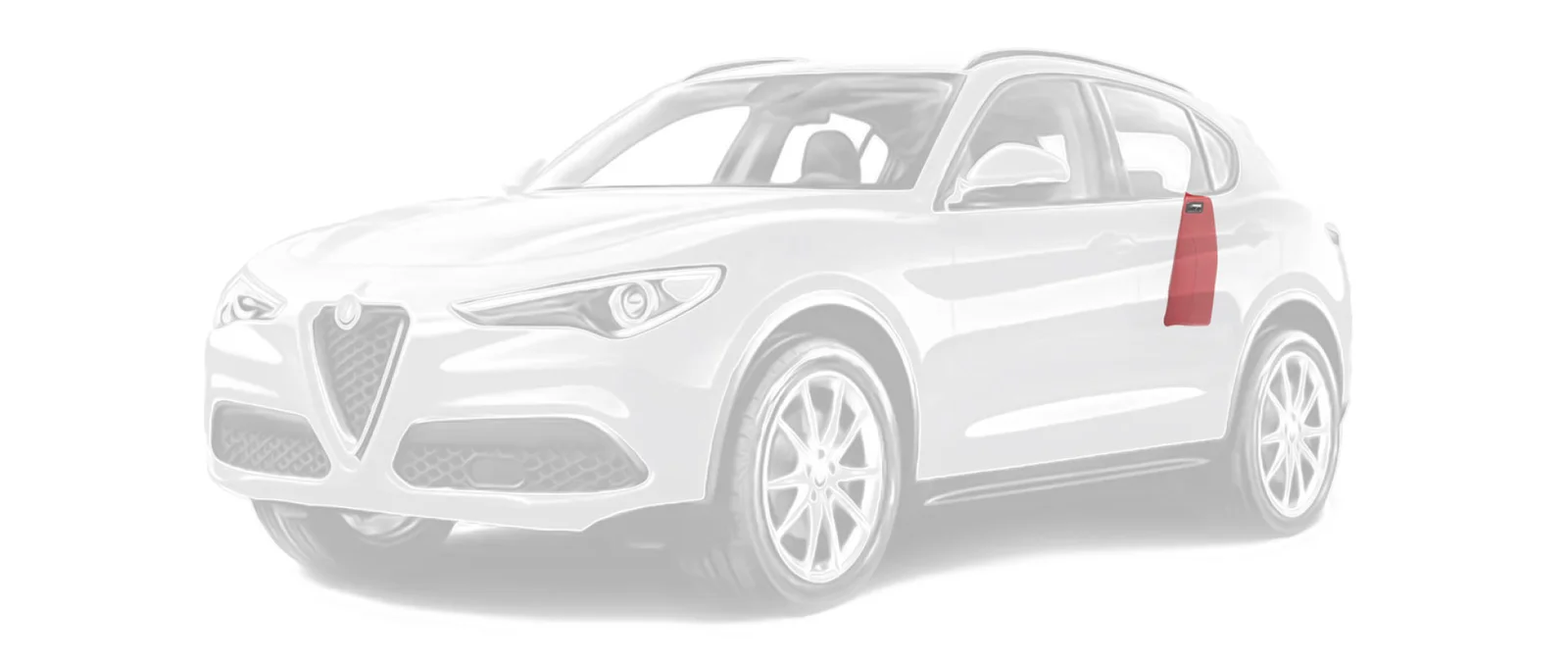
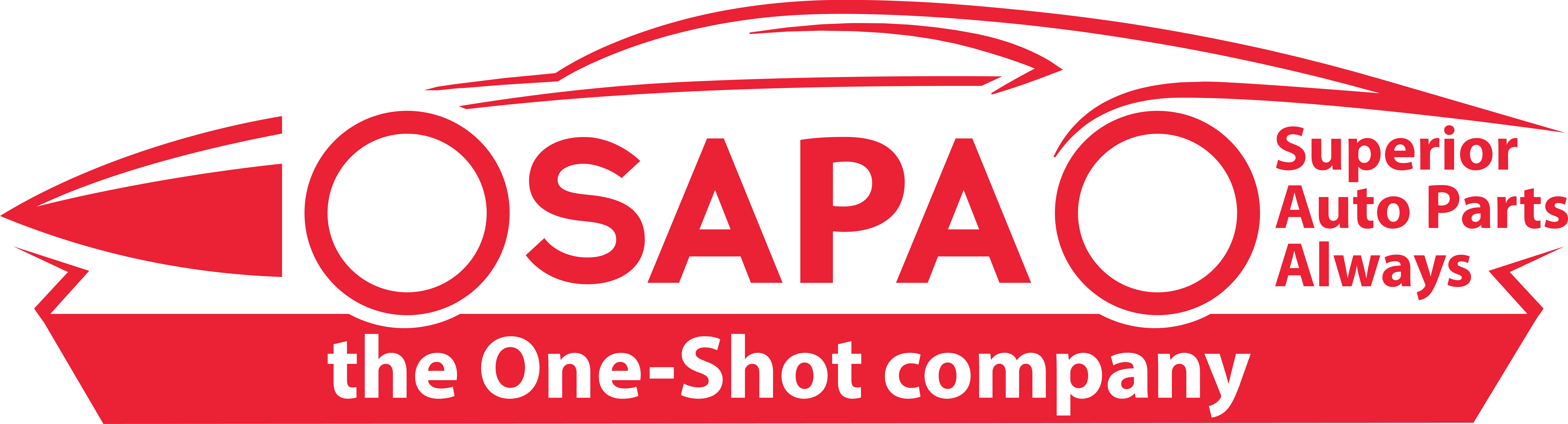
FCA-Supplier of the year 2018
In 2018, the prestigious FCA Supplier of the Year award went to SAPA.

Talk about us
SAPA ON THE MAIN NEWSPAPERS
What the Car Makers say about us

A-pillar bicolor & C-lower Pillar are really 2 interesting components.
Purchasing specialist - Skoda
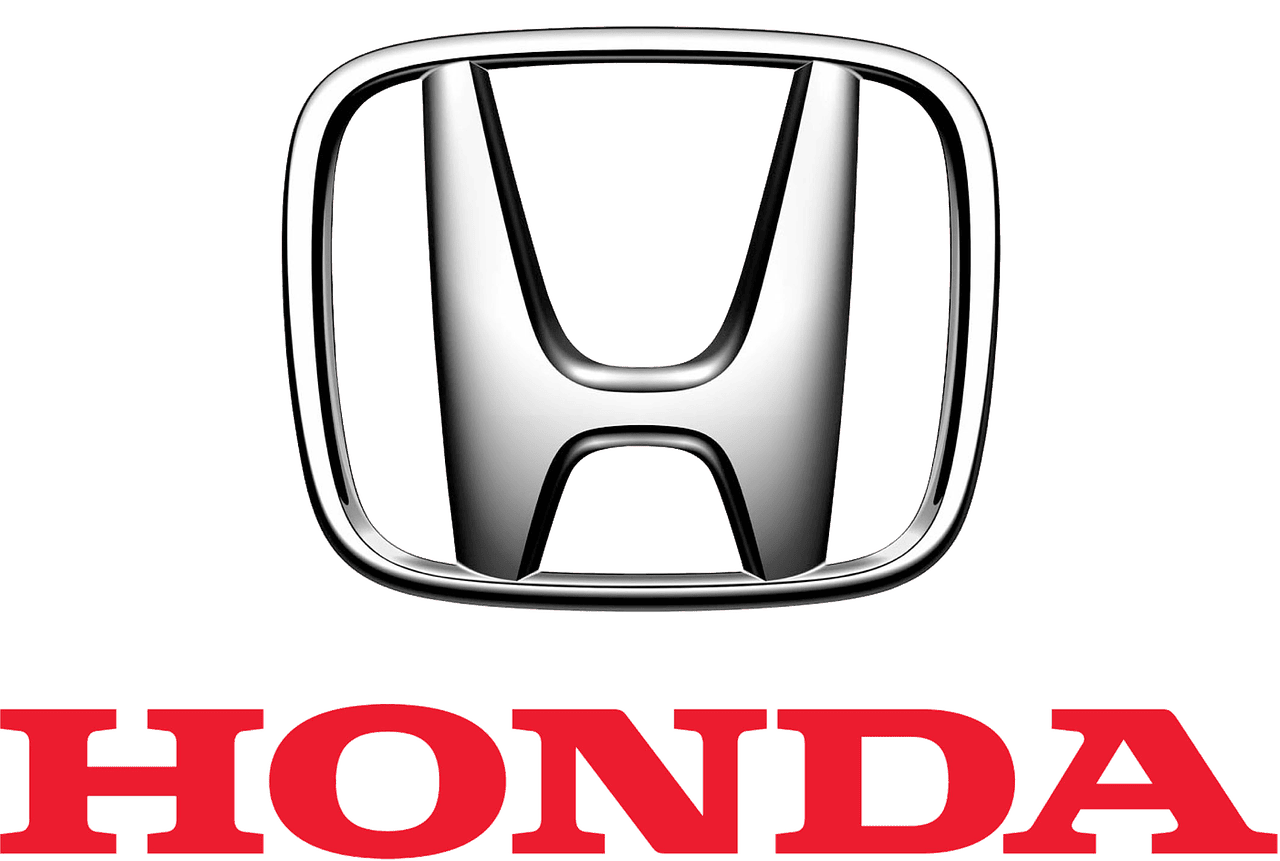
SAPA? Yes, the company with the bullet in the logo for their particular production speed!
Interior, R&D Europe - Honda
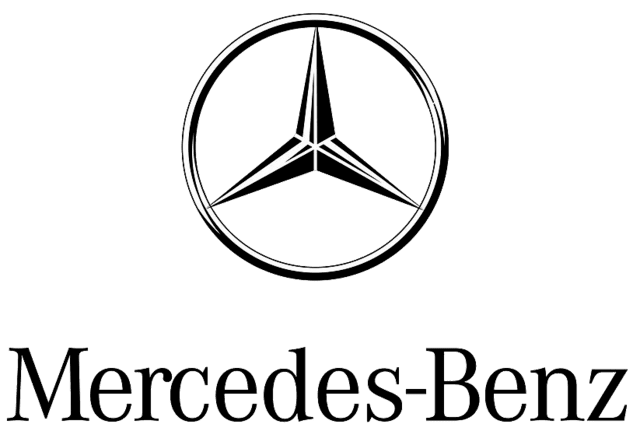
We hope that One-Shot@ technology can be a revolution in the development of the automotive sector, and can eradicate the normal gas injection process.
Car Design Interior and Exterior Modules - Mercedes
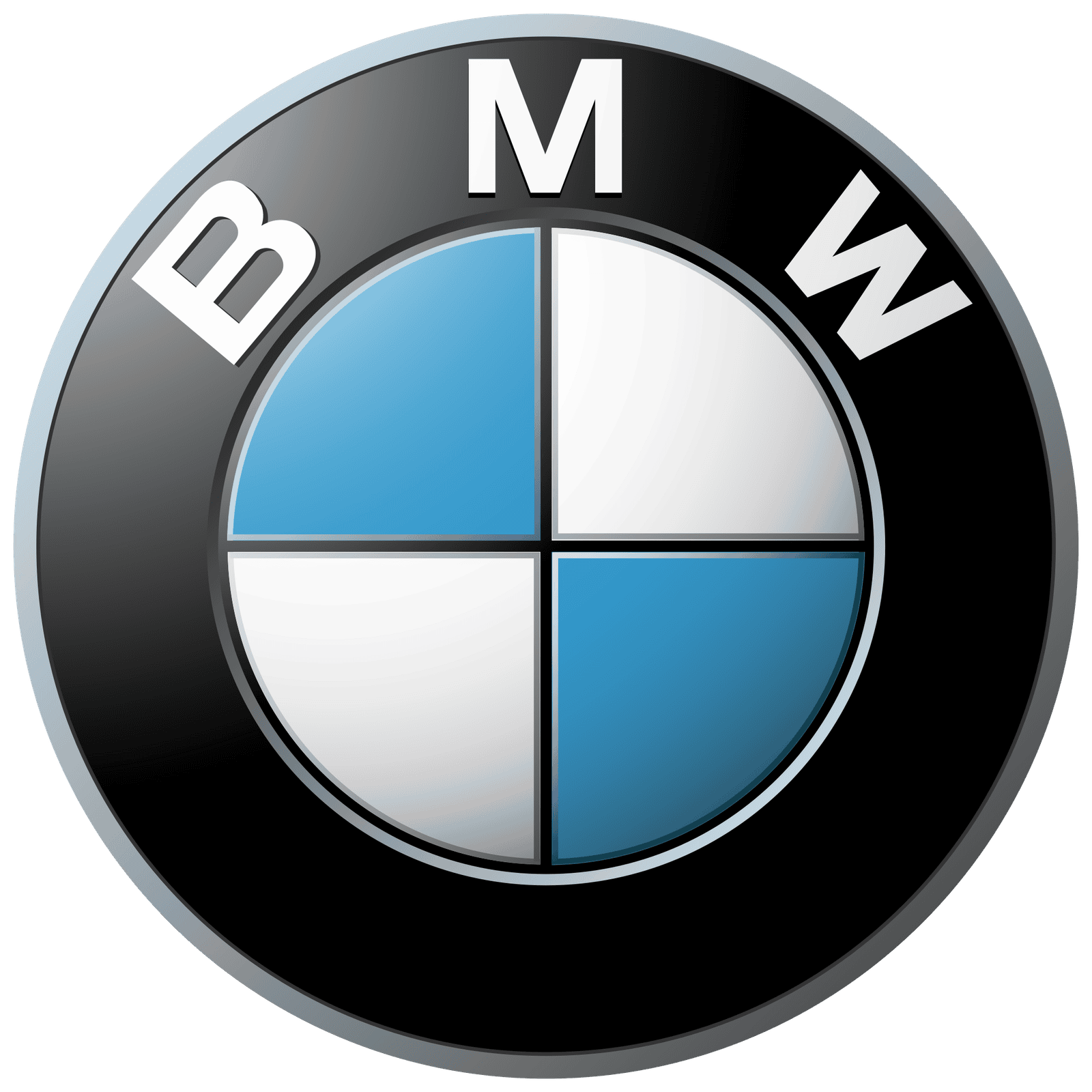
Getting to know SAPA and the One-Shot Method@ at IZB was absolutely interesting. l'd love to dive into the process with an expert!
Interior Design Engineer - BMW
