There is no better solution in terms of cost, design and industrial capabilities than plastics, in any technology. The most demonised product of our times remains a fundamental engineering resource, particularly in the automotive sector where it guarantees enormous advantages. Pollution? The problem is not plastic, but the use we make of it.
If an alien landed on our planet today, soon enough it would have the impression that humans have identified the cause of all evil.
What is it?
Plastic, of course.
Let’s face it, these days “fighting plastic” is in fashion.
The medias are all over it. Politicians take sides and everyone, knowledgeable and less knowledgeable, feels entitled to have their say on the harmful effects that this material causes on the environment after fulfilling its functions.
And as happens more and more often, we end up generalizing.
We hear about plastic all the time. But the type of plastic is never specified. Not a word on processes and materials used. Same thing with respect to the intended use.
“Plastic is always harmful,” they say.
“Hot air!” I say.
The trouble is that a superficial approach to such complex issues has devastating consequences.
First of all, because it takes you away from the core of the problem, whereas there is one and it is real. Plastic is indeed one of the major contributors to global pollution.
Much of it is produced (and production is destined to grow) and not enough attention has ever been paid – especially in a timely manner – to how it should be handled after use. Besides, for too long there has been no real research and evolution in materials and processes.
Plastic has been over-used; it has been used even when it was not strictly necessary.
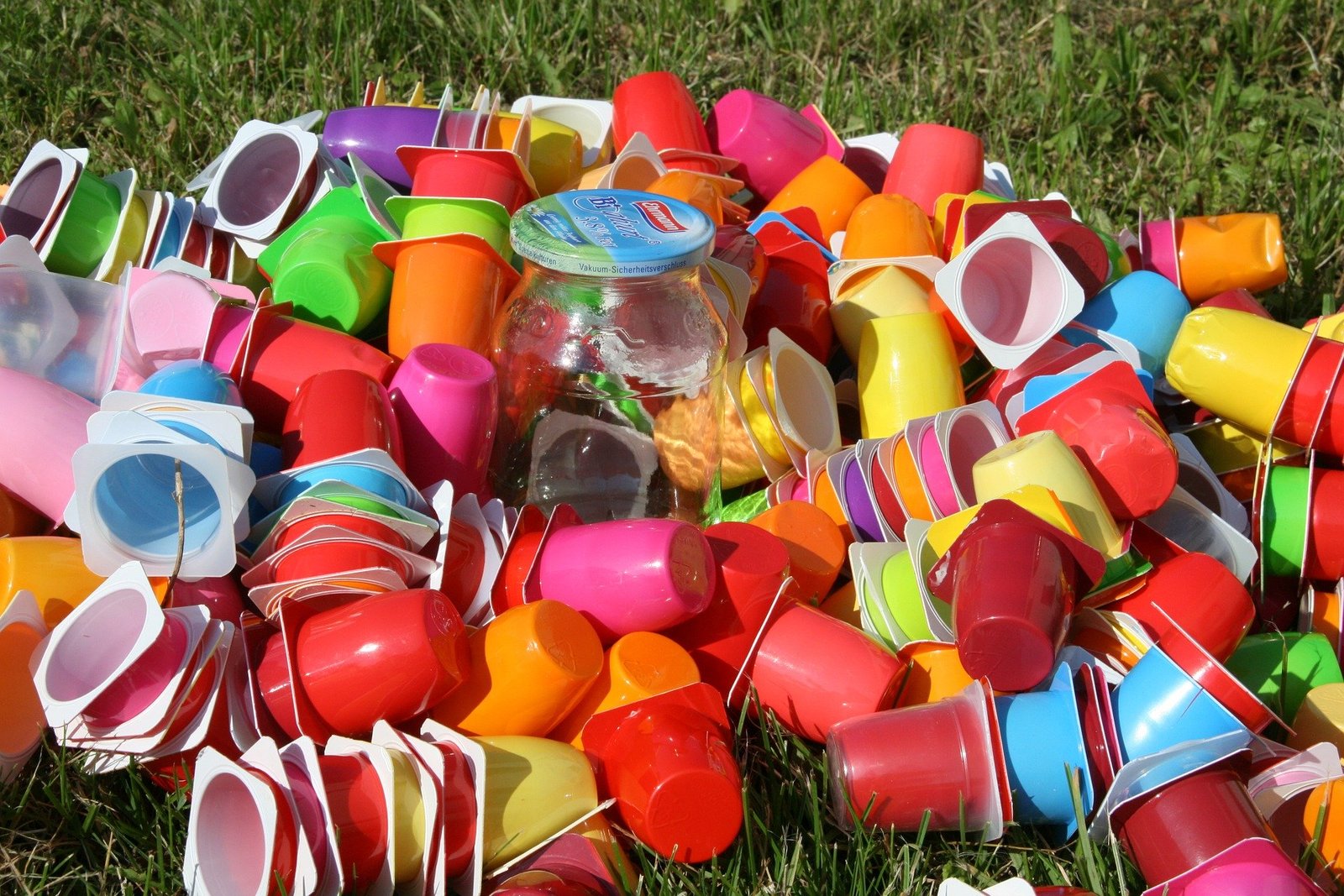
All true. But things are much more complex than that.
Please bear with me.
The normative bases from which to start are well known.
I am talking about the European Strategy on Plastics (with related directive on disposable products) and the Package of directives on the Circular Economy, among which is the directive on packaging (including plastic ones), which sets new recycling targets for 2025 and 2030 (respectively 50 and 55%).
Meanwhile, in Italy we have been talking about a Plastic Tax for months. It is known that it will come into force from July 2020, but how and who will be affected has not yet been defined.
Honestly? I believe that plastic suffers (also) from a gigantic image problem.
Result: the demonization of this product.
DO WE REALLY KNOW WHAT THE ADVANTAGES AND DISADVANTAGES OF USING PLASTIC ARE?
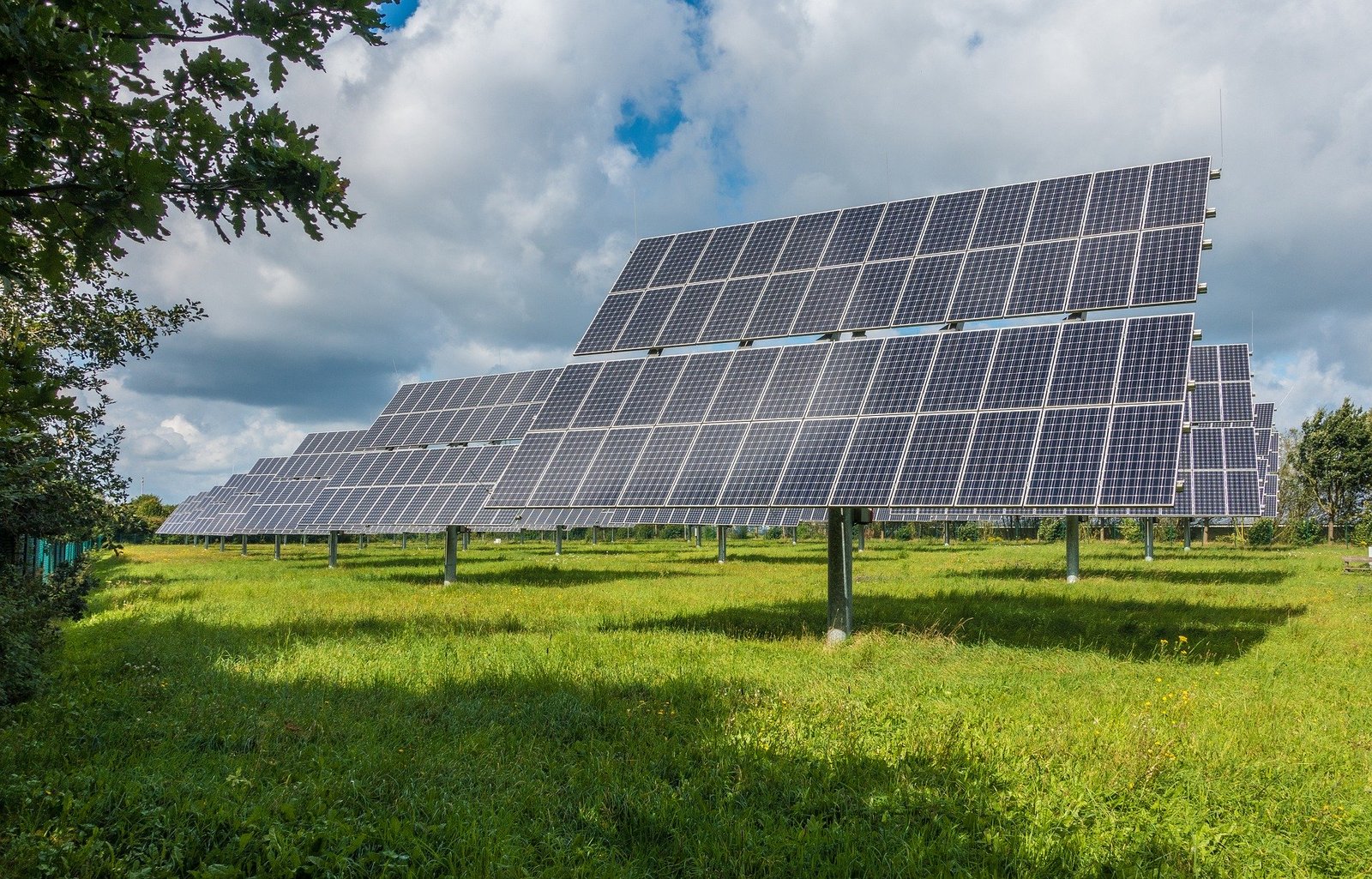
I mean, it is clear that there is a plastic issue, but do we really know what we are criticising?
There is often no full account of the advantages that humanity has gained from using plastics.
It has revolutionised the health industry, we may even carry it in our bodies as part of medical devices.
Without plastics we would not have all the disposable medical provisions that have improved the condition of patients, such as syringes, which were reused in the past, with the possibility of transmitting infections.
Let us think about food preservation, where advanced packaging reduces food waste and extends the shelf life of food.
And again, in the field of personal safety equipment, which depends heavily on plastics to ensure health and protection, through helmets, goggles and other objects.
Thanks to plastics it has been possible to create microchips that have tons of computing power, thus giving life to mobile phones, laptops, flat screen TVs, and the duration of batteries in electronics was also increased.
Plastics are tightly connected with renewable energy; without plastic you could not make solar panels.
I could go on much longer, but we are finally getting to the point that matters to us.
HOW ADVANCED POLYMERS IMPROVE THE AUTOMOTIVE INDUSTRY
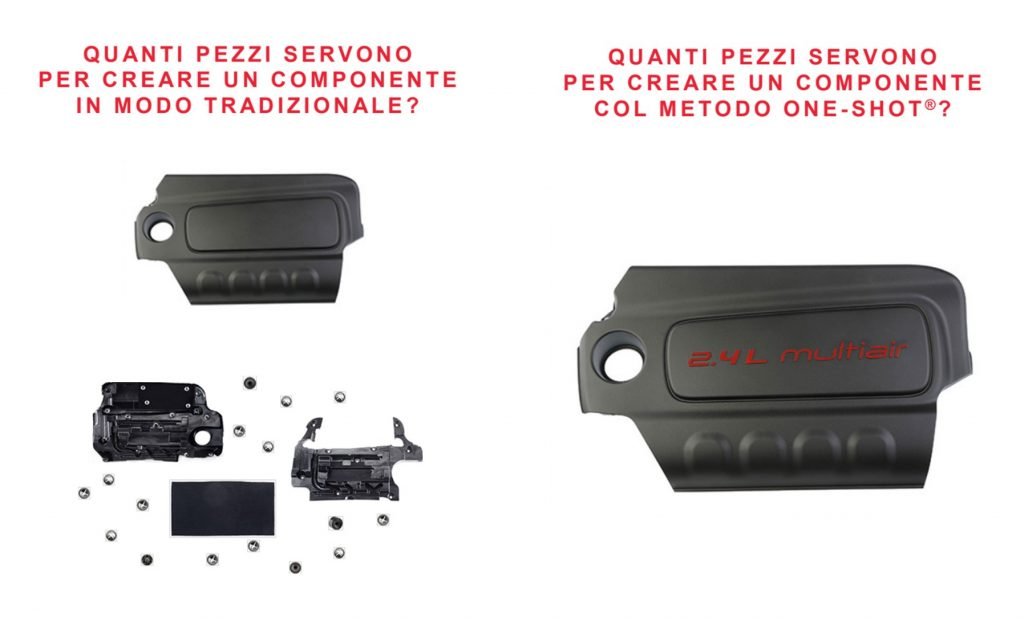
Another huge advantage that’s before everyone’s eyes is the use of lightweight plastics in the transport sector.
Corrosion-resistant, yet robust and lightweight parts for lighter vehicles that save fuel and reduce CO2 emissions.
Plastic is a very important engineering asset and resource, and for this reason it must be protected, studied, certainly improved, but above all it must be better managed.
SAPA specialises in the moulding of plastic components for the automotive sector: what we have been working on for years is lightweighting components from the design phase and using of advanced polymers to improve (among other things) recyclability.
How do we do this?
I would like to explain it to you because it could really help you in your daily work.
Our Innovation Engineering Department – after years of study and research – has created the One-Shot® Method, you’ve probably already heard of it.
It is currently the fastest method in the world to produce car parts, it has already been adopted by car makers such as Volkswagen, FCA, Jeep, Alfa Romeo.
One-Shot® guarantees advantages such as:
- Production cycle up to 900% faster and productivity increased by 300%.
- Reduced costs and commercial performance on your budget
- Lower emissions, lighter and recyclable parts in line with Horizon 2020
How is this possible?
By reducing all the steps of the traditional car part production to one all-in-one method. A lean production that often yields the part in just one single press stroke.
One-Shot®, indeed.
In addition to the process, we have also focused on the materials that this process requires.
The choice to use polymeric materials, instead of metal, is a winning solution, because it allows us to achieve multiple objectives.
- Weight reduction: a primary objective for electric cars, whose weight is already heavily penalized by the presence of batteries, which affects the vehicle’s autonomy and therefore its commercial attractiveness.
- Cost reduction: this is because they can be applied to many parts of the vehicle, from engine components to suspension and body parts.
- Lower vibration transmission: for quieter cars with less vibrations and hence more comfort
- Less friction: for parts that have a relative movement
- Production process: much simpler than with metal
An example of an application?
The polyamide reinforced with 30% glass fibre (PA66 30GF), which SAPA currently uses to produce some engine covers that require a constant operating temperature of 150°C.
EMISSIONS: -8% BY 2021 WITH LIFE BIOBCOMPOUND
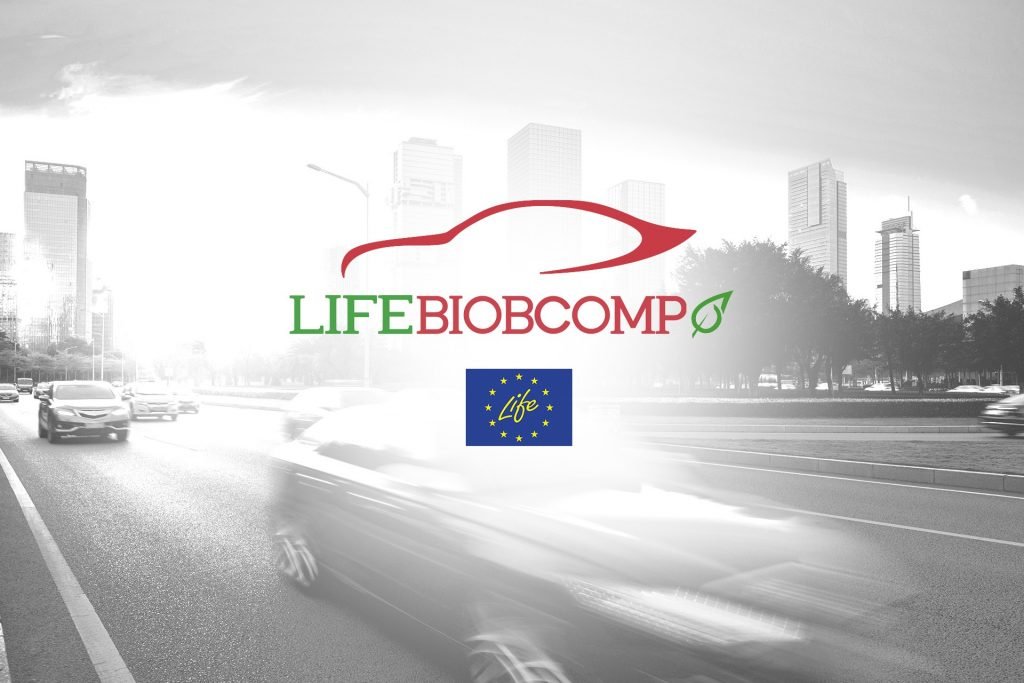
That’s not it.
SAPA is involved in the LIFE BIOBCOMPO project which, in collaboration with SOPHIA, CRF, FCA and with the support of the European Union aims to reduce CO2 emissions by 8%.
By 30 June 2021, SAPA will reduce CO2 emissions by 1.23 kg per km, thanks to the use of new composite materials.
The materials used will be affected in different ways, I will list three here:
– Less density
– Replacing traditional fillers with traditional fibres (bio-based fillers)
– Use of chemical or physical blowing agents
The use of innovative and more sustainable materials in comparison with the traditional methods will have direct positive consequences:
– Improvement in the processability of the new compounds with cycle time and process waste not exceeding those of the current production.
– Improvement of the aesthetic appearance through the optimization of the mixing process and moulding phase.
– Improvement of mechanical properties through the selection of fillers with higher performance than traditional ones.
All this is in line with the Horizon 2020 objectives.
The objective of LIFE BIOBCOMPO is not only to reduce vehicle emissions, but also to produce such light composites at costs compatible with customer requirements and to ensure that the new materials will be fully recyclable at the end of their life cycle.
By carrying out and funding research into more environmentally friendly solutions that reduce waste, we have reiterated a concept that is very dear to our company, that research is essential for modern development.
WHY THE FUTURE BELONGS TO PLASTICS
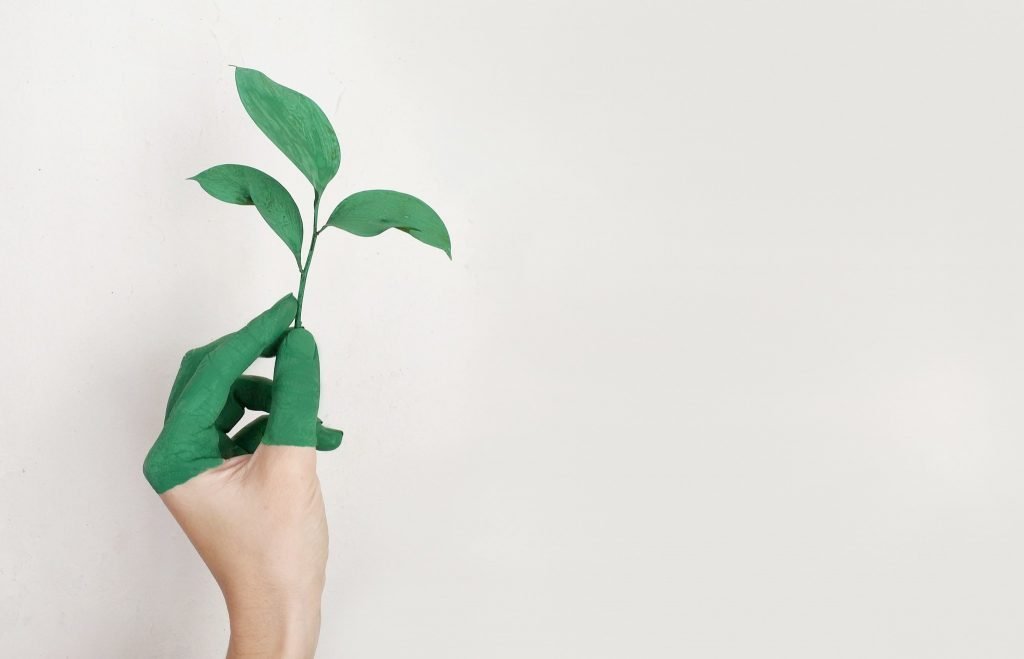
The future will be full of standardized processes, high performance parts (weight, mechanics, materials) and – as always in the car history – low costs.
Those who succeed in capitalizing on these changes will have a significant competitive advantage.
We are Process Specialists, particularly in polymers, and high-performance polymers.
At the moment there are no better solutions in terms of costs, design and industrial capabilities than plastics, in any technology.
In particular, the One-Shot® Method represents the premium level of design and industrial methods, because it allows to reduce the number of production steps and have much higher productivity.
Because plastic is not the problem. The problem is us, the way we produce it and the way we use it.
I can see the results we are achieving both in commercial terms and in the achievement of sustainability goals.
That is why there is one thing I can say without fear of being proven wrong: the future is still made of plastic, and bio plastic!
Kind regards,
Giovanni Affinita
General Manager and Member of the Board of Directors of SAPA